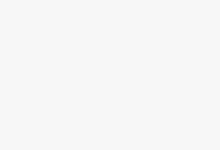
Application of Barcode Technology in Automobile Production Line
[ad_1]
Bar code technology has been widely used in my country’s commercial retail industry, and data collection for industrial online production is also of great significance. FAW-Volkswagen first used the barcode data acquisition system. Statistics and inquiries can be made at all relevant outlets of the system at any time, providing real-time and reliable information for production statistics and cost accounting. Another important content of its data collection is the complete record of various vehicle inspection data and various natural data of the production process, which can track the quality of the entire vehicle for life. Provide first-hand information for accident analysis, responsibility tracking, etc.
This article starts with the settings of the system. The basic principles and specific methods of system structure, data structure, program design, module setting, etc. are introduced in all aspects of function and management.
In the modern, large-scale automobile production industry, all kinds of production data. Real-time collection of quality information, and timely delivery of various types of information to material management, production scheduling, product sales, quality assurance, planning and finance, and other related departments as needed. This is important for raw material supply, production scheduling, sales service, and quality monitoring. , Cost accounting, etc., all play an important role. At the same time, this data is of great significance to the quality tracking and after-sales service of the entire vehicle.
Because the production and quality data are dynamic information, not only the amount of data is large, but also the content is complex, and because this data is not only used for production statistics and quality monitoring, but also has functions such as life-long quality tracking of the entire vehicle, it is necessary to ensure that the data is accurate ; In addition, for labor productivity and other considerations, it is impossible to set up a dedicated person to be responsible for data input at every site on the site, so data collection can only be completed by the production workers with the simplest operation, guaranteed by the system The real-time and accurate data is the difficulty in the development and implementation of this system.
The application of bar code and computer network technology provides a reliable guarantee for the realization of the above-mentioned functional requirements.
System Overview
The production data acquisition system of FAW-Volkswagen assembly line is the application of bar code technology, computer network technology and vehicle test bench test data transmission and other advanced high-tech in the contemporary world. It successfully integrates one front wheel alignment device and two rotating drum test benches. , An integrated electrical tester (ECOS), two sign making machines, 13 laser scanning guns, and 18 electronic computers are successfully and organically linked together to form a real-time assembly line production data and inspection data acquisition system . It can achieve tasks that cannot be completed by humans (such as vehicle testing data on the Internet, etc.). At the same time, it can truly record the natural conditions of the entire automobile production process, thus realizing the problem of comprehensive vehicle file data recording. The opening and running of this system marks that our company’s computer application has entered a brand new stage. In the large-scale automobile production industry, the successful opening of a complete computer data acquisition system such as the function has a leading level in our country.
The system uses the chassis number as the key word, and the bar code production station is based on the model. For different types of equipment, 3 chassis number barcodes are produced for each vehicle, and 4 copies of the “Assembly Line Supporting Work Instructions” are printed. When the CP6 body goes online, the barcode is affixed to the door, front cover, and vehicle card, and the final assembly line supporting operation instructions are sent to the engine sub-assembly, instrument panel sub-assembly, CP7 engine assembly, and logistics delivery. Instruct the relevant supporting workstations to organize supporting production and delivery in strict accordance with the on-line order of all kinds of bodies in the final assembly. Since then, laser gun scanning technology is used throughout the line, and the system automatically records the time of the car body CP6 on-line, optional variants, production shifts, operators and colors, and can print “optional parts operation guidance on CP6 according to user needs.” “Book”, and the assembler shall assemble optional parts and variant cars according to this instruction book. So as to ensure the smooth progress of mixed-flow production.
The sign making station can make car signs according to the results of laser scanning, eliminating the problem of wrong signs:
In the car body number printing station, the system automatically displays the car body number, model, type, equipment and other information on the 2.8×0.8m2 display screen according to the scanning results, and guides the assembly workers to print the car body number.
At CP7 offline, CP8 delivery, quality assurance department pick-up, sales department pick-up and other workstations, this system uses laser scanning technology, retrieves and data processing by a computer, and automatically completes data entry, proofreading, and time and shifts. The operator automatically records and other tasks. So as to achieve the purpose of not only reducing the tedious labor of workers, but also improving labor efficiency and ensuring the accuracy of data. If the system is implemented carefully according to the operating procedures, it can fundamentally solve the problem of the wrong number of the quadruple form and the certificate; at the same time, the encrypted barcode printed on the certificate by the system according to the special coding rules can also be used as a reference to the certificate of our company. The anti-counterfeiting effect will be incalculable for maintaining the reputation of our company, Jetta and Audi.
The real-time collection of testing data of the vehicle test bench is the difficulty of this system. The testing equipment of the vehicle test bench currently used by our company belongs to the contemporary advanced testing equipment of Schenck in Germany. It combines computer, PLC and high-precision testing. The machinery and equipment are combined. Due to factors such as technical patents and confidentiality, the company refuses to provide any information other than the equipment operation manual and the necessary spare parts list, especially the necessary information such as source programs, communication protocols, interfaces and addresses. The company is strictly confidential. Under extremely difficult circumstances, the comrades of the development team have gone through dozens of visits, experiments, and researches, and finally found the best way to solve this problem, and successfully realized that the original vehicle test bench equipment was not carried out. In the case of changes, the purpose of sending the test data to the computer network. The entry of this part of the data into the network is a very important expansion of the vehicle archive database. At present, our company produces various inspection data of automobiles. Various natural data of the production process are completely recorded in the vehicle archive database, which will be very important first-hand information for vehicle quality tracking, accident analysis, and responsibility tracking. At this point, foreign experts attach great importance to it, and they believe that the entire vehicle file. In particular, the entire vehicle inspection data must be retained until the vehicle is scrapped, but under our original manual conditions, this can only be an illusion and cannot be achieved at all. The opening of this system will fundamentally solve this technical and management problem.
Another important function of the real-time data collection of the vehicle test bench is that we did not expect at the initial stage of development. At the beginning of February 1997, the Ministry of Public Security issued a decision to exempt some domestic cars from inspection, and required that from July 1, 1997, all new cars manufactured by our company must be equipped with “complete vehicle quality assurance inspection line inspection data sheet”. The 27 items required for this review are 20 items of data that can be collected by the system, accounting for 74% of the required data. The existence of these data creates a very favorable prerequisite for this inspection and acceptance. At the same time, it also illustrates the leadership’s vision for the decision-making of the final assembly data acquisition system in 1994.
System functions
The real-time collection of field data lays the foundation for the development of system functions. On the basis of system data collection, the general assembly information application system software was developed. The system software can run in Windows and DOS environments with stable system performance and reliable operation. At present, the following functions can be realized by running this system:
Real-time production statistics This functional module can complete the following statistics:
Real-time output statistics: It can display the planned tasks of the day, month, and year at any time on the computer screen, the quantity that should be completed at that moment, CP7 offline, CP8 delivery, quality assurance pickup, sales pickup, etc. The actual completed quantity and the actual completed number Data such as the difference with the planned number of completions. This data can provide a reliable basis for production command and scheduling of production command and planning and coordination departments.
Monthly daily output statistics: According to the needs of the model, the daily production plan of the designated month of the year and the actual output of CP7 offline, CP8 delivery, quality assurance and sales pickup can be calculated according to the model, and the comprehensive data of the month can be calculated.
Vehicle information query This module can complete the following query functions:
1. Query by number: This query is more convenient, you can query by any item of factory number, chassis number, engine number and key number. It also includes the first one and the first two of the factory number; the first two and the first three of the engine number; the first two characters of the chassis number are required for special queries. You only need to enter the query conditions, and the computer will do the other things. This query can display all the data of the car. It is mainly used to query the details of the specified car. This query displays a screen for each car. If necessary, you can copy the screen and print it.
2. Query by personnel: This item can be queried by designated personnel codes (including CP6 on-line loading, CPcp7 line pick-up, CP8 inspection, quality assurance inspection, and sales pick-up personnel codes). Libraries (including workshop car storage database, sales database and historical database), various times (including CP6 online, CP7 offline, CP8 delivery, warranty pick-up, sales pick-up, etc.), color, optional equipment, engine type And other information to query. This function is mainly used to count the work status of designated personnel, and can be used for performance evaluation and bonus distribution.
3. Query by time: This query can be used to query various data within a specified time period (including CP6 online, CP7 offline, CP8 delivery, warranty pickup, sales pickup, etc.), and it can also be based on model, Information such as library type, color, optional equipment, engine type, etc. can be inquired. This function is mainly used to count the production data in a specified time period, and can be used for production statistics and query.
Comprehensive classification statistics module
Since our company’s current assembly line mixed production of various types of vehicles, each type is divided into multiple colors. It is very difficult to distinguish the number of vehicles of various colors in various types of vehicles. For example, it is very difficult to count the classification data of a batch of vehicles by manual methods. , And the error is unavoidable. It is almost impossible to count the hundreds of thousands of vehicles produced a year. In view of this situation, the comrade in charge of statistics in the Planning and Coordination Section of the Manufacturing Department hopes that we will develop a statistical query module based on colors and models, types, options and equipment. According to their requirements, we have developed a comprehensive classification statistical query sub The functions of the system are as follows:
1. Statistics by color and car model: When 1 is selected, the system will perform statistical query based on car model and color as key words.
2. Statistics by color type: When 2 is selected, the system uses type and color as keywords for statistical query.
3. Statistics by color selection: When 3 is selected, the system will perform statistical query based on the selection and color as keywords.
4. Statistics by color equipment: When 4 is selected, the system searches for equipment (that is, engine type) and color as keywords.
5. Statistics by model options: When 5 is selected, the system searches by model and options.
This statistical module is very powerful. It can count up to 99 colors, 99 models, 99 types, 99 options, and various combinations of 99 equipment. It can count all kinds of information in a few seconds to a few minutes. Such comprehensive data is very convenient and fast to use. It can also count the cars in the workshop, the cars produced this year, and any types of cars produced in 1996 (including CP6 online time, CP7 offline time, CP8 delivery time, warranty pick-up time Time and sales pick-up time data), production data at any time period (accurate to year, month, day and hour).
Various report printing
This module can print various reports, including:
1. Print according to various numbers
2. Print according to various types of personnel
Three, print according to various times
The functions and operations of the above three options are basically equivalent to the vehicle information query module, so I won’t repeat them here.
1. List printing of stagnant vehicles: This module is specially designed for final assembly inventory. It can print the list of stagnant vehicles sold by CP7-CP8 and CP8 at any time as needed.
2. CP7 Completion Report: This module can print the CP7 offline report for any date, which is mainly designed for the production statistics of the manufacturing department. In order to increase the printing speed, the system has a special reminder of “Printing CP7 Report Form before Class”. When this option is selected, the system only retrieves the internal database of the workshop, so the speed is very fast.
3. CP8 Completion Report: This module can print the CP8 offline report of any date, which is mainly designed for the production statistics of the manufacturing department. Like CP7, in order to increase the printing speed, the system specially sets up a reminder of “Reporting to CP8 before printing”.
4. Vehicle production daily report: This option can print the vehicle production daily report on any date of the year. This report includes the current day, month, and year CP7 off-line, CP8 delivery and sales pickup of various models and types of vehicles. The data required for production statistics such as the number of production, the number of stays, and the total number of production.
Since the computer network of our company has been basically completed, the development of the functional modules of this system is completely carried out on the basis of eliminating manual reports and realizing the requirements of computer network information transmission. The successful development of this system has laid a solid foundation for the computerization of our company’s production management.
System Management
The safe and reliable operation of any modern management system is inseparable from two factors. One is the reliability and safety of the system itself. Because the system runs on the production site, it is required to have high fault tolerance and correction. Error ability, as far as possible to avoid any errors due to misoperation and other possible reasons, this should be ensured by the system design and development; another point, and the most important point, must establish a complete set to ensure the normal operation of the system The application of modern technology must be based on scientific and strict management. Here is a brief introduction to some of the methods we have adopted in these two areas:
1. The system itself is safe and reliable:
Because this system is a real-time online production data collection system, it is different from the general management information system. Due to the nature of online production, no system failure is allowed during production. Any small problem in the system may cause Stop production, so the safe and reliable operation of the system is a very important issue that must be seriously considered and resolved in the system design.
(1) Network server: The final assembly data acquisition system is an important part of our company’s computer LAN (Local Area Network). The barcode reading equipment mainly refers to the laser scanner and its supporting equipment and barcode reading software; the server runs It is Window NT Server 3.51 network software. The server adopts the dual-system hot backup mode to ensure that when Server 01 fails, Server 02 can immediately switch to working state to ensure the normal operation of the system.
(2) Hardware configuration of each site: During the development of this system, we adhered to the principle of saving expenses as much as possible and doing everything diligently and thriftily on the premise of meeting the functional requirements of the system. For the data collection nodes on site, although the system has high requirements for reliability, the amount of data transmitted is small after all. Therefore, in terms of hardware configuration, we have simplified the hardware configuration and replaced the original design with the 386 microcomputer eliminated by the management department of our company. The INITEL industrial computer in China uses an ordinary 586 microcomputer to replace the network server. The ordinary computer cannot catch up with the industrial computer in terms of anti-interference and stability. To overcome this lack of function, we mainly solve it from the design of improving the anti-interference performance of the cabinet. This alone has saved the company more than 700,000 yuan. Since the system was opened in October, 1995, we have taken effective measures in anti-interference and other aspects, and all the replacement machines are operating normally, fully implementing the functions of the industrial computer, and the system has never had any problems due to this.
(3) Equipped with general backup equipment for outlets: As the system has 18 outlets at the final assembly site, the hardware configuration and software of each outlet are different. Therefore, when any outlet fails, hardware repairs and software debugging will take a long time. In general, it will cause a downtime of about 0.5-4 hours, which will threaten the smooth progress of online production. In view of this situation, we have set up a set of general backup equipment for the outlets. The hardware of the equipment is configured according to the highest demand, and the dedicated software of each branch is installed, so that no matter which branch fails, the backup equipment can be installed in the shortest time (usually within 10 minutes), and the faulty equipment can be removed Carry out repairs and replace them with spare equipment after repairs. For more than a year, online production has never been affected by this system problem, thus ensuring the smooth progress of online production.
(4) Safety precautions: At present, some systems are often paralyzed due to viruses. Because online production data is the company’s most important information, any mistakes will cause irreparable losses to the company. Since the main transmission route of computer viruses is floppy disks, and the system is started by hard disk, and the data is transmitted through the network, the system does not require a large amount of floppy drives. In view of this situation, we will turn off the floppy drive of the microcomputer on site. Cut off the virus transmission medium to ensure the safe and reliable operation of the system.
2.Management
(1) Establishment of standard process card: At the beginning of the system operation, we first carefully analyzed the essentials of system operation, and established standard operating process cards for each branch, and included the use of this system in the scope of the company’s process management and process inspection. This laid the foundation for the normal operation of this system.
(2) Establishment of standard operating procedures: Although the operation of this system is relatively simple, since our users are basically workers engaged in production, most of them know nothing about computers, and the mobility of workers is relatively high. Therefore, we have established a standard operating procedure for each branch and posted this procedure on the relevant work station. According to this operating procedure, any operator can learn the operation of this system in a relatively short time, thus effectively avoiding Possible errors caused by incorrect operation.
(3) System training of operators: Despite the above measures, the training of operators is also indispensable. In the initial stage of system operation, we use centralized training methods to conduct theoretical training and practical operation training for relevant personnel, and issue system operation cards to qualified staff who are trained. This card is also an information entry card for system identification and recording; after the system runs normally , We mainly conduct on-site training for personnel who are added at any time, and we adhere to the system that all personnel who are on duty must be trained and hold a card to work.
(4) Drafting of the management assessment system: To ensure the actual realization of the above management measures and methods, the management assessment system is also a key part. In February 1996, we drafted the “About Assessment Regulations for Ensuring the Normal Operation of the General Assembly Production Data Collection System. The formal implementation of this regulation will surely play a major role in ensuring the good operation of the system.
(5) The establishment of a network operation record book: to ensure the reliable operation of the system, according to our years of network operation experience, the “system operation record book” of each branch is also necessary. This record book mainly records the operation of the system Some abnormalities or changes have a great effect on the analysis and handling of accidents.
The above are some of the measures and methods we have taken to ensure the reliable operation of the system. These measures and methods have played a key role in ensuring the operation of the system.
Concluding remarks
The production data collection system of FAW-Volkswagen’s final assembly line took about one year with the attention and care of the company leaders, the strong support of the management service department and relevant departments of the company, and the guidance of the leaders of the car factory and workshop. Going through the stages of system investigation, system preliminary design, detailed design, hardware production, program design, equipment installation, system debugging, etc., a lot of hard work has been done, and the technical indicators proposed by the system design have been basically reached. Expected functionality. The system was put into operation in early October 1995. The opening of this system brings great convenience to our company’s production, quality, finance, management and other aspects. The successful operation and application of the system will surely promote the computer application of our company, FAW and the national automobile industry. effect.
[ad_2]