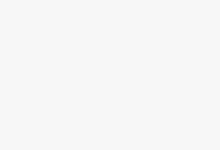
MES barcode quality traceability system solution for automobile and parts industry
[ad_1]
In the modern and large-scale automobile and parts production industry, real-time collection of various production data and quality information, and timely delivery of materials management, production scheduling, product sales, quality assurance, planning and finance, and other information as needed Related departments transmit all kinds of information, which play an important role in raw material supply, production scheduling, sales service, quality monitoring, cost accounting, etc. At the same time, this data has important significance for the quality tracking and after-sales service of the entire vehicle.
Because the production and quality data are dynamic information, not only the amount of data is large, but also the content is complex, and because this data is not only used for production statistics and quality monitoring, but also has functions such as life-long quality tracking of the entire vehicle, it is necessary to ensure that the data is accurate ; In addition, for labor productivity and other considerations, it is impossible to set up a dedicated person to be responsible for data input at every site on the site, so data collection can only be completed by the production workers with the simplest operation, guaranteed by the system The real-time and accurate data is the difficulty in the development and implementation of this system.
Through the organic combination of barcode technology, computer network technology and information system, we have successfully connected various locators, rotating drum test benches, integrated electrical testers (ECOS), sign making machines, barcode scanners, computers and other equipment organically. Together, it forms a real-time assembly line production data and inspection data collection system. It can achieve tasks that cannot be completed by humans (such as vehicle testing data on the Internet, etc.). At the same time, it can truly record the natural conditions of the entire automobile production process, thus realizing the problem of comprehensive vehicle file data recording.
620)this.style.width=620;” border=0>
The automobile or parts production quality management system developed by Beijing Jingcheng Software Information Technology Co., Ltd. (EAS Software) provides comprehensive product production and quality management, covering incoming material management, engine processing and assembly, stamping, welding, painting, final assembly, Testing and commissioning, audit, after-sales service, product traceability and other links, and can realize information interaction with management systems such as ERP and CRM.
MES system overview
Jingcheng EAS-MES manufacturing execution system is a set of production developed by Beijing Jingcheng Zhibo Technology Co., Ltd. on the basis of many years of enterprise information construction experience and ERP system implementation experience, using advanced bar code technology and combining with the actual needs of users. Pipeline control system.
620)this.style.width=620;” border=0>
The Jingcheng EAS-MES manufacturing execution solution integrates the excellent management experience of top international and domestic manufacturing enterprises, integrates personnel, equipment, materials and other manufacturing elements into the supply chain platform with the concept of lean production, reduces human errors and improves the production line Work efficiency, and provide accurate and detailed data for product and production line data statistics, realize the rapid response of the enterprise manufacturing end to the needs of front-end customers, and help customers forge excellent manufacturing enterprises.
The system adopts C/S (Client/Server) structure design, Microsoft SQL Server 2000 database, realizes the unified coordination of internal business systems, and facilitates the storage and query of large amounts of data in the factory. The system runs at high speed and accuracy, and is combined with the Internet. The application, reserved for future Internet query of other branches or factories and offices.
620)this.style.width=620;” border=0>
The Jingcheng manufacturing execution solution fully integrates the Jingcheng EAS-ERP system with the production line code acquisition system, and designs interfaces that integrate with other related information systems, such as ERP, MRP, CRM, etc., and mainstream ERP systems such as SAP, ORACLE, and UFIDA Have successful integration experience.
The Jingcheng EAS-MES manufacturing execution system is based on a large number of network hardware equipment and barcode scanning equipment. The normal operation of these equipment ensures the stability of the system and is the prerequisite for the safe, efficient and stable operation of the production workshop management system. The main hardware equipment includes: Server , Barcode printers, barcode scanners, data collectors, barcode labels and consumables, LED large screen billboards, etc.
The Jingcheng EAS-MES manufacturing execution solution covers the core business process management of the enterprise, helping the enterprise agile manufacturing, exquisite management, quickly reflecting the return on investment, and meeting future growth requirements.
EAS-MES system function
Production planning and scheduling: The production planning and scheduling management module is the link module between the macro planning management and the micro scheduling optimization management. Through effective planning and detailed scheduling of production capacity, it can ensure that customers’ products are delivered on time. The production capacity is maximized. For companies that make to order, with the miniaturization, diversification and randomization of customer orders, this module becomes an effective way to adapt to orders and save production capacity and costs.
Production process control: This module controls the production process according to the production process, prevents the wrong installation, missed installation, and multiple installation of spare parts. It collects data from the workshop in real time and monitors the production status and quality status of the products, finished products and materials. At the same time, it can be used Bar code automatic recognition technology realizes the supervision of the production status of employees.
Data collection: There are mainly two types of data collection, one is data collection based on automatic identification technology (BarCode, RFID), which is mainly used in assembly data collection in discrete industries, and the other is device-based instrument data collection, which is mainly used Material information collection in automatic control equipment and fluid production.
Quality management: Based on the idea of total quality management, the quality management module records and analyzes the quality of the entire production and life cycle of products from suppliers, raw materials to after-sales service, and controls the quality of the production process on the basis of production process control. The problem is strictly controlled. It can effectively prevent the flow of defective products and reduce the rate of defective products.
620)this.style.width=620;” border=0>
Material tracing: The material tracing function can track all finished products that use the batch of materials according to the quality defects of the batch of materials, and also supports reverse tracking from finished products to raw materials to adapt to the recall system of certain industries and assist manufacturers Minimize losses and serve customers better.
Resource management: Technology, staff and equipment are the three important resources of manufacturing enterprises. EAS-MES organically integrates the three into the manufacturing execution system to achieve comprehensive manufacturing resource management.
Statistical process control: This module helps companies stabilize the production process and evaluate process capabilities. By monitoring the stability and development trend of the process, we can find defects or variations in time to solve the problem in time; through the process capability index evaluation, we can clarify the level of work quality and product quality in the process.
Statistical analysis: A large number of reasonably designed and optimized reports provide managers with quick statistical analysis and decision support, real-time grasp of each link in the production, and at the same time, the production progress and defect rate can be displayed through the large LED screen in the workshop. Feedback production status.
620)this.style.width=620;” border=0>
After-sales service system interface: In order to cooperate with the comprehensive quality management process of modern enterprises, the EAS-MES system is designed with a corresponding after-sales (factory) quality management interface, which can be connected with CRM or other after-sales service management software to provide sales and service for finished products after they leave the factory. Effective management of quality-related issues in the process to achieve the root cause traceability of quality issues in the after-sales service process, and quality management throughout the entire life cycle of the product.
ERP/financial system interface: This system can realize the collaborative work with ERP (have collaborative experience with mainstream ERP systems such as SAP).
System management: system user management, authority management, log management, system settings, ERP interface, LED interface and other functional modules.
Implementation benefits
• Transparency of the manufacturing execution process: Through the EAS-MES execution system and equipment control technology, detailed production process data such as process output, process yield, work order transfer status, test parameters and other detailed production process data are collected in real time, and a summary analysis report tool is provided It provides an effective basis for the production management decision-making of managers at different levels of the enterprise.
• Shorten product manufacturing cycle: improve the degree of enterprise production automation, replace and save a lot of manual work processes, and shorten the product manufacturing cycle. At the same time, implement information collection and feedback to eliminate various production process delays caused by information asymmetry, so that production managers can grasp first-hand production information in real time outside the production workshop, and quickly respond to emergencies. The output is more closely integrated with the plan.
• Improve product quality: Through monitoring the entire production process, providing quality control personnel with basic data and analysis tools to help companies conduct daily quality analysis and periodic continuous quality improvement. Through SPC and other process control tools, the stability of the process, the fluctuation of product yield, and the distribution of defective defects are monitored in real time and early warning, and effective prevention and provision of problems on the production line are provided.
• Continuously improve customer satisfaction: Based on a large number of comprehensive summary reports, provide customers with summary data such as production process man, machine, and material data, output, and defective rate, and analyze through intuitive bar graphs, pie graphs, and broken line graphs. , Can accurately and conveniently understand the product data and the company’s overall operating conditions.
• Reduce production costs: Through real-time monitoring and early warning of the production site, prevent the occurrence of problems and reduce the number of product maintenance and heavy work. It also provides various statistical analysis electronic reports, which saves time, manpower and material resources, realizes paperless production in the factory, and reduces the use of manpower and other production resources.
[ad_2]