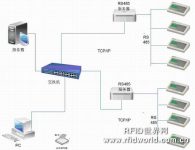
Dongguan Yishili Technology RFID Clothing Production Solution
[ad_1]
Garment manufacturing enterprises are labor-intensive enterprises. As we all know, in the process of garment production management, the biggest management difficulty is the on-site management of the workshop. How to solve the real-time feedback of the data of the workshop production line to ensure the authenticity of the data and the timeliness of solving the problem; how to ensure the smooth flow of the assembly line, how to solve the accumulation of products and how to find the bottleneck process in time; how to ensure that the ready-made clothes can be delivered on time, etc. Factors bother managers. Under such circumstances, RFID production site management solutions based on radio frequency technology have emerged, which can collect production data in real time for analysis and provide corresponding solutions.
From the perspective of the development process of the clothing industry, the information management process of clothing is mainly divided into the following four parts:
1.Manual stage
Workers manually record them in a notebook, and a dedicated person manually summarizes and calculates their wages;
2.Stamping stage
Workers use scissors to cut out the paper labels (ie work ticket records), and then summarize them to the computer (or manual processing by a dedicated person);
3. Semi-computerized stage (paper fei)
Each process is printed out with a bar code, and the bar code is tied to the corresponding fabric to circulate in the production workshop. The worker cuts the bar code of the process he has done as a production certificate. Then, a dedicated person will scan the barcode to the computer system.
4. Automation phase (RFID)
Yishili’s RFID information management system uses radio frequency identification technology (RFID) to provide a set of complete solutions for the factory through real-time collection of worker production information and work efficiency. Help managers obtain real-time production data from the system platform, and can understand comprehensive information about production progress, employee performance, parking space status, and the number of products in progress anytime and anywhere. At the same time, electronic tags establish a connection channel for managers, company executives and front-line workers in the workshop. The production progress of each worker can be directly fed back to the manager, real-time statistics of worker piece rate, assessment of worker performance, and multiple analysis data from different perspectives. So that managers can make objective decisions and dig deeper into more meaningful data. Thereby improving the production efficiency and management decision-making ability of garment enterprises.
1. The value of RFID production management system
Production data can be collected accurately and in real time
Productivity is improved on the original basis
It can realize real-time monitoring of the working status of the production line lathes
Real-time tracking of order progress to ensure timely delivery
Strict quality control, reduce repair rate
Statistics of production capacity and piece rate salary through RFID system
RFID cutting card completely replaces the original cutting card
2. System application process
1) When the sewing worker inserts the employee card into the card reader after going to work, the system shows that the machine is online;
2) After the sewing worker gets the tie bag, remove the tie bag card on the tie bag and insert it into the card reader, the system shows that the machine is working;
3) After the sewing is completed, the sewing worker pulls out the binding card from the card reader, and the system obtains the production quantity and production hours;
4) The card is bundled back and passed to the subsequent process;
System architecture diagram
3. The value of all aspects after the application of RFID
Help companies conduct process analysis, rationally standardize the production process of the company, and make it achieve production balance, so as to maximize the productivity of the factory.
(1) In terms of workers:
Through RFID real-time data collection and the reform of worker performance appraisal, the goal of workers’ self-management is achieved, thereby doubling the efficiency of workers.
Efficient workers can get higher wages and reflect the principle of fairness. RFID helps companies find good workers, retain good workers, and attract good workers.
The process card can only be read once in the same process, eliminating worker fraud and realizing accurate collection of time and quantity.
The data is transparent, and employees can know the number of individual pieces at any time (this depends on the wishes of the manager, and it is also possible to keep the workers from knowing).
Combined with performance appraisal, it effectively stimulates the enthusiasm of employees and enables employees to manage themselves, thereby reducing the difficulty of factory management.
(2) Middle management:
Know the production progress of each process, reasonably balance the production line, and maximize the production capacity of the production line.
Know the working status of each worker, and conduct personalized management for each worker based on data.
The factory’s requirements for the experience of middle-level management are reduced, and the capacity of the entire production line is no longer affected by the level of a certain middle-level ability, so that the middle-level management ability is transformed from experience to knowledge and data.
(3) Production management:
Managers can clearly know the production schedule of a certain order or a certain style, so as to easily cope with the shipping schedule of the foreign order.
Managers no longer need to go to the workshop to understand the production progress of the entire factory, saving valuable time.
To clearly understand the production bottleneck, it is only necessary to require workers to work overtime in the process where the work-in-process is blocked, and other workers may not arrange overtime, thereby reducing wage costs.
(4) Equipment management:
Equipment asset management makes the factory’s machinery and equipment clear at a glance.
Be clear about the operation and usage of each production equipment, and plan the investment of production equipment reasonably.
4. Benefit analysis after application
(1) Staff reduction
After the introduction of RFID, the original Philippine cleaning staff and the dedicated Philippine cleaning staff are no longer needed. At the same time, it reduces the staff’s operating error rate and reduces the economic losses suffered due to operating errors. It can save labor cost by about 8%;
(2) Efficiency improvement
It turned out that it took about 27s for workers to cut the Philippine and sweep the Philippine. After the introduction of RFID, the time it takes to swipe the card to return the information to the system is reduced to 1~2s, and the efficiency is greatly improved. Increase productivity by about 30%;
(3) Cost reduction
The paper and printing ink of the existing system can not be recycled. After the introduction of RFID, the labels used by the system can be reused many times, which can save a lot of costs;
(4) Facilitate production scheduling
After the RFID system is introduced, the machine utilization rate of the production workshop and the actual production efficiency of the workers can be counted, which is convenient for timely adjustment of production scheduling. Cycle time is shortened by 18%. Corresponding reduction in production loss can be up to 10%.
Five, successful cases
Jeanswest Apparel (China) Co., Ltd.
Dongguan Yixun Industrial Co., Ltd.
[ad_2]