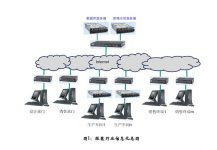
Supply chain management of textile, clothing and fashion product enterprises based on RFID technology and RDN software
[ad_1]
1 Introduction
Competition in the garment processing industry is becoming more and more fierce. To be invincible in the market competition, enterprises in the garment industry must continuously improve production efficiency and shorten the capital turnover time. According to market research and analysis, through informatization of the entire clothing industry, production efficiency can be greatly improved and capital turnover time can be shortened. At present, most of the clothing industry is all manual work, without any informatization, resulting in poor information feedback. When a problem occurs, it cannot be discovered and dealt with in time, which leads to a lack of work in many links. At the same time, the situation of product sales can not be grasped in time, leading to the out-of-stock of the best-selling products and the under-sales products, which also reduces the profit.
If all aspects of product design, raw material procurement, order placement, order execution, product processing, quality inspection, warehousing, logistics transportation, distribution, and product sales are all informatized, it will provide users with real-time dynamic tracking and query throughout the process; realize processing information and systems Monitoring and management of operation status and business operation quality, while providing real, effective, and timely management and decision support information for managers at all levels, providing support for the rapid development of the business, will be able to solve all problems, and thus reduce costs and increase profits. And competitiveness.
The following is a brief introduction to the most important aspects of informatization solutions from product design, raw material procurement, order placement, product processing, and product sales.
System overall design
The program design is based on a large entire clothing company, which has a design department, a sales department, several production workshops, and several sales terminals. And these departments are not in one place. If you are in the same place, the system is equally applicable, but the network is somewhat different. If there are several design departments and several sales departments, just add network equipment and terminal equipment. There is no major change in the overall system.
The overall design principles of the plan: inherit the existing advanced management ideas, use practical, feasible, mature, reliable, safe, advanced, open and scalable technical means, and achieve a good performance-price ratio information system to achieve “a platform Three unified” informatization goals:
Build an integrated management platform, unify application standards, unify operation procedures of all business links, unify data formats, software, hardware, and data exchange.
2.1. Overall system design
In the system center, there is a database server on which database software is installed. The server is a data center, and data from various places is collected in the database through the network. At the same time, the system is also equipped with a management application server, which is used to run application services.
In the design department, n terminal devices are configured, and these n terminal devices are connected to an Ethernet. Through the switch, these devices can access the application server of the system center through the Internet to run the application. Through the assignment of permissions, designers can carry out design work.
In the marketing department, configure n terminal devices, and these n terminal devices are connected to an Ethernet. Through the switch, these devices can access the application server of the system center through the Internet to run the application. Through the distribution of permissions, sales staff can carry out marketing-related work.
In each production workshop, n terminal devices and 1 server are configured. The database and application programs are running on the server, and the terminal device accesses the server to complete the corresponding work. At the same time, the server is connected to the Internet, and regularly sends data to the database in the system center.
In each sales terminal, n terminal devices are configured, and these n terminal devices are connected in an Ethernet. Through the switch, these devices can access the application server of the system center through the Internet to run the application. Through the distribution of permissions, sales staff can carry out sales-related work.
2.2. System Center Design and Architecture
A database server is provided in the system center to store all data. The data can be stored within 3 years.
A management application server is provided in the system center, which is used to run the application programs of the system. The system adopts C/S architecture. The terminal devices of various departments can run the system software as long as they access the server.
2.3. Design department workflow design and system application
2.3.1. Design department workflow
The workflow of the design department is shown in the figure above:
2.3.3. Functions implemented by the design department system
The functions realized by the design department system mainly include:
(1) Determine the clothing brand, serial number, etc. through the system, as the unique identification of the clothing, which is convenient for future maintenance and management.
(2) Through the decomposition of the process department, a piece of clothing can be decomposed into several parts. When an order is placed, the quantity and type of parts required for this batch can be quickly calculated according to the part situation, which is convenient for organizing production.
(3) Through the calculation of the craft department, the main materials and auxiliary materials needed to process a piece of clothing are clarified. When an order is placed, the quantity and type of the main materials and auxiliary materials needed for this batch can be quickly calculated according to the main materials and auxiliary materials, which is convenient for purchasing.
2.4. Marketing department workflow design and system application
2.4.1. Marketing department workflow
The job description of the marketing department is as follows:
(1) After the marketing staff receives the order, they need to enter the order information into the system software.
(2) The marketing personnel first enter the order number, marketing personnel’s name, customer name and other information.
(3) Then enter the order details. Select the name and number of the first garment (if not, the design department needs to do the corresponding work), and then enter, the earliest delivery time and the latest delivery time. Repeat the above work to complete the establishment of order details.
(4) If there are multiple orders, repeat steps (2) and (3) to complete the order entry work.
2.4.2. System supporting situation of marketing department
2.4.3. Functions implemented by the marketing department system
The functions realized by the marketing department system mainly include:
(1) Enter the order status and detailed information in the system to facilitate future production arrangements, including order merging and order splitting.
(2) Enter the order details in the system to facilitate the purchase of main materials and auxiliary materials according to the quantity of the order.
(3) The informationization of orders facilitates order tracking.
(3) Through the calculation of the process department, the main materials and auxiliary materials needed to process a piece of clothing are clarified. When an order is placed, the quantity and type of the main materials and auxiliary materials needed for this batch can be quickly calculated according to the main materials and auxiliary materials, which is convenient for purchasing.
2.5. Production workshop workflow design and system application
2.5.1. Production workshop workflow
The production workshop includes four major aspects: the production comprehensive management area, the raw material area, the processing area, and the finished product warehouse area. The workflows are as follows:
.1.1.1 Comprehensive management area
The comprehensive management area is mainly to realize the pre-production processing of orders, including order decomposition, scheduling, and procurement of main materials and auxiliary materials. The workflow is as follows:
1.1.1.2 Raw material area
The raw material area is mainly to realize the reception and inspection of main materials and auxiliary materials. The workflow is as follows:
The raw material is divided into three parts, one is the main material area, and the other is the auxiliary material area.
1.1.1.3 Processing area
The processing area is mainly to realize the cutting of main materials, the matching of parts and auxiliary materials, the sewing of finished clothes, and the inspection of finished clothes. The processing area can be divided into a tailoring area, an auxiliary material distribution area, a production distribution area, a processing area, and an inspection area. The workflow is as follows:
The following will be divided into 5 sections to explain the working process:
Cutting area
The specific process of the cutting area:
Accessories distribution panel
The specific process of the auxiliary material distribution panel:
The specific process of production and distribution area:
(1) According to the production plan, the production-related personnel query the number and type of the component bundles and auxiliary material trays required by the batch from the system, and issue relevant instructions to transport them to the production distribution area.
(2) Confirm the component bundles and auxiliary material trays one by one in the production distribution panel area. After the confirmation is completed, the RFID tag is recycled.
(3) Relevant management personnel print out an RFID label for each piece of clothing in the plan according to the batch situation. The content of the RFID tag includes: order, clothing name, clothing brand, clothing description, distribution time, etc.
(4) The production staff shall carry out production and distribution in accordance with certain rules. Every time a tray is finished, put the RFID tag into the tray.
Production area
The specific process of the production area is described as follows:
(1) Production is divided into four stages: pre-production, intermediate inspection, post-production, and final inspection.
(2) In production, processing is carried out according to the production line. After processing one process, the disc is transferred to the next process. One process after another process completes the processing of the entire garment.
(3) Under each process, a reader-writer antenna is provided, which can collect the number of disks in each process in real time and write it into the system software.
(4) In each process, 3 buttons are also installed, one for failure, one for backlog, and one for leaving job. Workers click the corresponding button according to their own situation. In this way, the status of each process is also written into the system software.
(5) After the final inspection, install an LED display to display the production status.
(6) Relevant management personnel can monitor the position, backlog, and order production at any time through the monitoring computer, and at the same time, make corresponding treatments based on the above conditions to ensure the maximum efficiency of production and avoid the phenomenon of idle work.
(7) At the inspection site, a reader antenna and a computer are also provided. The problems detected in the final inspection are entered into the system software at any time. The relevant management personnel can keep abreast of the quality status of the inspection at any time.
(8) At the end of the investigation, configure 1 reader antenna and 1 computer at the same time. The problems detected in the inspection department are entered into the system software at any time. The relevant management personnel can keep abreast of the quality of the follow-up inspection at any time.
Inspection area
The specific process of the inspection area is described as follows:
1.1.1.4 Finished product area
The finished product area is mainly to realize the storage and delivery of finished products, and its work flow is as follows:
The specific process of the finished product area is described as follows:
(1) After the worker drags a cart of clothing packaging boxes to the finished product warehouse, they disassemble the packaging boxes into boxes by boxes. Through the RFID reader, the information of each packaging box is read separately, and then the cargo space is automatically allocated according to the distribution of the warehouse area. After a batch of production is completed, workers are required to carry out the inventory through a handheld terminal. If it is correct, confirm it. If there is an error, a library is required.
(2) When there is a bill of lading, check the cargo location according to the bill of lading, and leave the warehouse one box by one. When leaving the warehouse, an RFID reader is required to read the information of the packing box and confirm it.
2.5.2. Supporting situation of production workshop system
In the production workshop, an LED label management computer and a label printer are provided for printing RFID labels in the process. Configure 1 server at the same time to save data and run applications. The server needs to exchange data with the database server in the system center, so it must be connected to the Internet. In the connection with the Internet, a firewall and an intrusion detection system need to be configured to ensure the safety and stability of the system. , According to the personnel situation, 1 to n computers are provided. At the same time, a switch is provided to connect these computers to an Ethernet network.
2.5.3. Functions implemented by the production department system
The functions realized by the production department system mainly include:
(1) Tracking the main materials.
(2) Tracking auxiliary materials.
(3) Track the parts.
(4) Track the distribution of disks.
(5) Tracking the garment processing.
(6) Follow up the inspection.
(7) Carry out sorting identification on garment sorting to avoid sorting errors.
(8) Track the packaging to avoid packaging errors.
(9) Releasing relevant information in time through LED display.
(10) Through the reminders of various alarms, it is convenient for relevant personnel to deal with errors in time.
(11) Improve work efficiency by monitoring and tracking the status of the workstation.
(12) Automatic allocation and verification of finished product locations.
(13) Automatic verification of outbound.
2.6. Workflow design and system application of exhibition room and sample room
In order to facilitate the convenient maintenance and security of the exhibition room. Equipped with 1 RFID reader and 2 antennas in the exhibition room, as well as a computer. The antenna is installed at the door to prevent anyone from taking out the exhibits. At the same time, it is equipped with a handheld RFID reader to facilitate the inventory of the exhibits in the exhibition room. The computer is connected to the Ethernet in the production workshop.
If you have any questions, please contact
Ren Zhixian
15801381484
qq:479017087
[ad_2]