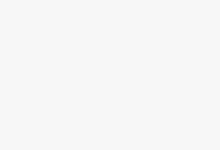
The application and solution of barcode in the footwear and apparel industry
[ad_1]
Use Data Collector to Realize Warehouse Management Automation
1. Problems that can be solved by warehouse management automation
1. Multi-database collaborative operation
For the needs of circulation, the products of enterprises in the footwear and apparel industry are often distributed in different warehouses in various places for transfer, distribution, and replenishment. There are also many types of warehouses, such as: finished product warehouse, raw material warehouse, circulation warehouse, turnover warehouse, scattered small warehouses, etc. The inventory of each warehouse needs to be monitored daily to ensure timely supply. Through warehouse management automation, the inventory of each warehouse can be checked at any time, so that the logistics process of products can be tracked in time.
2. Warehouse receipt and offer operations
One of the most important tasks in warehouse management is to ensure that the booked quantity is consistent with the actual quantity. The use of data collectors can easily realize the accuracy of the goods receipt record and the automation of delivery and distribution, so that there will be no omissions in the inventory. And lost.
3. First in, first out
Each product has a lifespan. Due to the many types of products, it is difficult to ensure accurate first-in, first-out products through manual records and custodian records in actual warehouse management. Through the single tracking technology, a clock can be built in for each product, and the intact state of each product can also be recorded, so that the goods can be shipped out of the warehouse within the specified time limit.
4. Out of stock alarm
When there is a shortage of a certain product in any warehouse, not only can the alarm be automatically prompted, but it can also be subdivided into details of product composition such as model type, color, and size. That is, if a certain size of a certain style is broken, the custodian can immediately be reminded to replenish the goods in time.
5. Statistics of slow-moving goods
The backlog of products in the footwear and apparel industry is a very headache. Through the statistics of unsalable products, the residence time of each product (subdivided into models, colors, and sizes) can be obtained, and you can quickly find out which products are unsalable and out of season. , You can easily provide price reduction decisions to accelerate product sales.
2. Realization of warehouse management automation system
1. System structure
2. Hardware composition
Data collector: configure to each warehouse and the management office of each warehouse
Server: Configured in the headquarters and collect inventory reports from various warehouses
Modem: used to transfer data between different places
Use data collectors to automate sales
Shoes, hats and apparel products are a kind of fashion products. Many factors such as the season of sale, the location of the sale, the taste of consumers, the fashion trend, the price of the product, and many other factors will affect the sales of the product. Therefore, real-time tracking of sales status is a very important management content for footwear and apparel companies.
1. Problems that sales automation can solve
1. Sales statistics
The statistics of the daily sales report are very important to the sales department of a company. It requires accurate results as quickly as possible. Sales statistics include: statistics by style, color, location, size, etc., which can help the sales department allocate and replenish goods in time.
2. Counter sales automation
Using the data collector can realize the functions of the portable POS machine in the monopoly counter, and can complete the functions of sales, return, counter inventory, inventory, collection and other sales automation operations; at the same time, it can generate various statistical reports of the day and send them to the headquarters or The local office conducts sales analysis.
3. Analysis of broken code sales
The best-selling varieties in different locations are different, and the demand for different sizes will not be the same. It is necessary to replenish in time when the size is broken. Sales statistics and analysis can be used to increase the possibility of code breaks that are expected to occur so that timely replenishment can be notified.
4. Allocation between counters
The sales situation is different between different locations. Through the allocation between different counters, the product circulation can be accelerated, and the sales volume can be expanded to the maximum. Some varieties are not easy to sell on certain counters, but if you change a location (or a counter), it will become a good selling variety. This can effectively reduce the number of unsalable varieties on the counter.
5. Return control
In the market competition, all manufacturers are improving the quality of service and allowing customers to return goods. Through statistical analysis of returned goods, product quality problems can be accurately identified, and the responsible department, responsible unit and responsible person can be held accountable.
6. Counter inventory
Counter inventory is a very tedious and error-prone task for each specialty counter. Using the data collector can easily achieve counter inventory, improve work efficiency, and will not produce any inventory errors (especially after using the unique encoding method of a single unit), and the inventory results can be quickly sent to the superior unit.
7. Store reconciliation
Generally, the goods sold in the specialty counters are collected by the shopping malls, so reconciliation and collection with the shopping malls are a headache for corporate accountants every month. Using the sales automation system, the daily sales records in the data collector are automatically corresponded to the various accounts of the shopping mall, so that the reconciliation work is clear at a glance.
Second, the realization of the sales automation system
1. System structure
2. Hardware group
Data collector: configure to each monopoly counter (support barcode scanner)
PC: Configure to each office
Server: Configured in the headquarters, collect sales data from various places, and establish a sales database
Modem: used to transfer data between different places
Use barcode technology to realize production process management automation
The manufacturing process of footwear, hats and apparel enterprises is generally completed in a variety of ways. Such as: production according to order, planned production according to market forecast, contract subcontracting, commissioned processing and production, etc. The key to the production process is to control cost and control quality.
1. Problems solved by automation of production process management
1. Material cost control
All the used production materials have a unique number, attached with a barcode label, and established a strict picking control. Through each type of product material list, the product production plan is broken down into a material use plan, the trim allowance is calculated reasonably, and the material consumption of each batch of products and the deviation from the standard cost are controlled.
2. Operation time control
Through the attendance clock set at each operation point, the working time of each operator is recorded. After statistical analysis, the operation time of each batch of products and the deviation from the standard operation time can be calculated.
3. Order quotation
For each received order, it has always been a headache for customers. Because of the cost data (work time and material consumption) of a single product, the profit margin can be easily calculated.
4. Quality process control
Using single tracking technology (bar code identifier in each product), quality control can be carried out on each operation link of the product in the manufacturing process, and the responsibility of the operator can be held.
5. Production statistics
Through the bar code identification mark, the output statistics, waste statistics and material consumption statistics of the products can be automatically completed.
6. Decomposition of homework tasks
In the manufacturing process, multiple varieties are often mixed and manufactured, and tasks need to be rationally arranged to meet the production tasks of multiple orders at the same time. Decompose a batch into multiple small task orders and assign them to each operator. Through the barcode identifier in the job sheet, the sorting of the job sheet can be completed, and the completion of the job sheet can be controlled.
7. Piece counting statistics
Many companies adopt the piece rate method, and piece rate statistics is a very tedious task. Through the single tracking technology, the bar code identification on each product and the production work sheet, it is easy to count the output completed by each worker, and the responsible personnel can also be held for defective products.
2. The realization of production process management automation
1. System structure
2. Hardware composition
Attendance clock: configure to the workshop or production line
Barcode printer: configure according to production capacity
Collector: Configure according to key operation checkpoints
Server: Configured in the headquarters
PC: Divided and configured according to management department
Use barcode technology to automate supply process management
Shoes, hats and apparel products are a kind of fashion products with many varieties and rapid changes. The goal of supply management for consumer industry enterprises is to increase the speed of supply. It is characterized by a multi-variety, small-batch supply method, and the supply certificate must be timely and accurate to meet the needs of production and sales.
1. Problems solved by automation of supply process management
1. Procurement control
Establishing a file of material supply information can effectively control the quality and price of the material. The code of the purchased material is affixed with a bar code as a unique identification, which is convenient for inventory management.
2. Order matching
Purchase orders are often delivered multiple times, and orders are frequent. In order to ensure that the order and the arrival of the goods will not cause confusion, they must be matched one by one, and the arrival of each order can be checked at any time. The materials ordered should be uniquely identified by bar codes to facilitate the inventory and investigation of the supplier’s product quality problems.
3. Supply cycle control
In order to ensure the needs of production and sales, and to reduce the inventory backlog of materials, the time of supply must be controlled. Through the supplier’s unique number and service quality certification, the supply time of each material is accurately calculated, and orders can be ordered as needed to ensure immediate production.
4. Quality tracking
By matching the barcode identifier of the purchased product with the quality inspection sheet, the supplier’s quality responsibility can be effectively investigated.
5. Entrusted processing control
Many manufacturers only operate their own brands, and generally entrust OEM manufacturers to manufacture and produce, and assign them to various OEM manufacturers to paste on the products through pre-made bar code labels. It is easy to count during acceptance. Any quality problems found in the sales process can be directly investigated to the original manufacturer, and the remaining materials after commissioned processing can also be quickly calculated.
6. Cargo tracking in transit
Shoes, hats and clothing products are a kind of goods with a fast turnover rate. They are often put on the market quickly once production is completed and distributed to counters in various places. The goods account for a large proportion of goods in the transportation process (including transfers between different regions). Using barcodes as unique identifiers can accurately track the goods in transit, and can strictly guarantee the arrival time and quantity of the goods.
7. Payment reconciliation
Many manufacturers use the method of multiple, batch orders, and payment at the end of the month. The reconciliation of payables is a very important task. Through the method of automatic matching between the unique identifier of the order and the unique identification of the payment voucher, the reconciliation can be made clear and easy, and the amount payable can be automatically calculated.
2. Realization of supply management automation
1. System structure
2. Hardware composition
Barcode printer: configure according to production capacity
Collector: Configure according to the key operation points of tracking goods
Server: Configured in the headquarters
PC: According to the configuration of the supply management department
[ad_2]