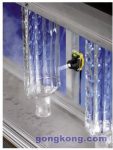
Banner’s flexible solution for easy-to-use ultrasonic sensors
[ad_1]
Technological advances have made today’s ultrasonic sensors very durable and precise sensing capabilities. These new technologies make ultrasonic sensors simpler, more flexible, and more cost-effective. These newly enhanced features have opened up a new application field, completely surpassing the application of traditional ultrasonic sensors. Today’s ultrasonic sensors provide mechanical designers with a new and creative solution in the industrial field.
A few years ago, in the field of sensor technology, ultrasonic sensors have always been a backup choice. Designers will only choose ultrasonic technology when other sensing technologies cannot work. It usually occurs when detecting transparent objects, long-distance sensing or when This technique is only used when the target color changes.
The application of new technology enables today’s ultrasonic sensors to withstand the test of harsh environments: Ultrasonic sensors with IP67 and IP69K protection levels can be used in humid environments, such as bottle cleaning machines. Built-in temperature compensation circuit, under normal or changing operating conditions, when there is an obvious temperature change, the temperature compensation circuit will perform calibration. The surface of the Teflon model ultrasonic sensor has a special coating that can be used to resist the erosion of harmful chemicals. The advanced filtering circuit allows the ultrasonic sensor to shield the field interference. The new sensor head has stronger self-protection ability, can resist material damage and adapt to a messy environment.
Ease of use
A notable feature of the new generation of ultrasonic sensors is that it is easier to use, which includes button settings, DIP switch programming and some multiple program options. The switch button is completely embedded in the sensor device, which makes it very easy to adjust the distance of installing the sensor. It is a simple matter to place the target in front of the sensor and then press the button.
This kind of sensor can automatically grasp the size and distance of the window. Easy installation means that the same sensor can be adapted to many different applications. The programming method of the DIP switch means that a simple sensor can be customized for some special applications. These personalized features include response time, output type, switch and analog selection, and special features for level/liquid level control. set up.
Ultrasonic sensors generally contain multiple output types in a single sensor. The model with two switch outputs can use one sensor to sense two objects at different distances at the same time, and it has one switch output and one analog output at the same time. It can be used to measure and provide alarm output. The above characteristics make ultrasonic sensors more flexible and selective in use compared with sensors of other technologies.
Basic principles of using ultrasonic sensors
Ultrasonic sensors use the vibration of the pressure-vibrating ceramic on the sensor head to produce high-frequency sound waves that are inaudible to human ears. If this sound wave hits an object, the sensor can receive the return wave.
The sensor can determine the distance of the object through the wavelength of the sound wave and the time difference between the transmitted sound wave and the received return sound wave. Typically, a sensor can be set by a button to have two settings of close range and long range, regardless of the object Within that kind of limit, the sensor can detect it. For example: an ultrasonic sensor can be installed on a tank filled with liquid or a box filled with small balls. Sound waves are sent to the container. The time it takes to receive the return wave can determine whether the container is full, empty or Is partially full. Ultrasonic sensors also use independent transmitter and receiver models. When detecting slow-moving objects, or requiring rapid response or application in a humid environment, this kind of cross-radiation or separate ultrasonic sensor is very useful. Be applicable. Ultrasonic sensors are the first choice when detecting transparent objects, liquids, detecting smooth, rough and shiny surfaces, translucent materials, and detecting irregular objects. Unsuitable situations for ultrasonic sensors include: outdoors, extremely hot environments, and pressured containers, and objects with foam cannot be detected as well.
Key points of ultrasonic sensor selection:
Range and size
The size of the detected object will affect the maximum effective range of the ultrasonic sensor. The sensor must detect a certain level of sound waves to be excited and output signals. A larger object can reflect most of the sound waves to the sensor, so the sensor can be in its This object can be sensed to the maximum extent, and a small object can only reflect very few sound waves, which significantly reduces the range of sensing.
Measured object
The most ideal object that can be detected by an ultrasonic sensor should be a large, flat, high-density object, which is placed vertically facing the sensing surface of the sensor. The most difficult to detect are those that are very small in area, or are made of materials that can absorb sound waves, such as foamed plastic, or have corners facing the sensor. Some objects that are more difficult to be detected can be taught on the background surface of the object first, and then react to the object placed between the sensor and the background.
When used for liquid measurement, the surface of the liquid needs to face the ultrasonic sensor vertically. If the surface of the liquid is very uneven, the response time of the sensor should be adjusted longer. It will average these changes, which can be read more fixedly. Pick.
Using ultrasonic sensors in retrosonic mode makes it possible to detect irregular objects. In retrosonic mode, ultrasonic sensors can first detect a flat background, such as a wall. When any object passes between the sensor and the wall, it will obstruct With sound waves, the sensor senses the interruption, and then realizes that there is an object.
vibration
Whether it is the vibration of the sensor itself or the surrounding machinery, it will affect the accuracy of the distance measurement. At this time, you can consider taking some shock absorption measures, such as using rubber anti-vibration equipment as a base for the sensor to reduce vibration, or use a fixed rod. Eliminate or minimize vibration. Attenuation When the ambient temperature changes slowly, the temperature-compensated ultrasonic sensor can make adjustments, but if the temperature changes too fast, the sensor will not be able to make adjustments.
Misjudgment
Sound waves may be reflected by some nearby objects, such as guide rails or fixed fixtures. In order to ensure the reliability of detection, the influence of surrounding objects on the reflection of sound waves must be reduced or eliminated. In order to avoid false detection of surrounding objects, many ultrasonic sensors have a The LED indicator is used to guide the operator to install to ensure that the sensor is installed correctly and reduce the risk of error.
Typical applications of ultrasonic sensors
Ultrasonic sensors were once considered too difficult or too expensive to operate, but with the reduction in cost and convenient use, more and more mechanical designers have incorporated ultrasonic sensors into their machines. The industrial applications of ultrasonic sensors include detecting filling conditions, detecting reflective objects and substances, controlling the expansion of the loop rope and measuring distance. The following are a few application examples:
In the filling workshop, inspect the bottles (using the picture of QS18U)
In the food processing workshop, inspect and control the filling of the container (using the picture of QT50U)
In the packaging workshop, the rotation speed of the raw materials is controlled by detecting the tension between the two rollers. (Use the picture of T30U)
Inspection of bolt heads of automobile engines. (Use the picture of Q45UR)
The application of ultrasonic sensors in industry is developing rapidly. This once very expensive and inaccurate technology has now become simple and easy to use, with high accuracy and low cost. Ultrasonic sensors have become a conventional equipment to improve product quality in process control, and are used in detecting defective products, confirming appearance or disappearance, and other fields. This sensor can also increase productivity, it can reduce waste and avoid downtime due to damaged parts. In the future, the development of such products in this technical field will continue this trend. This is a challenge, but a consensus has been reached in the industrial field that ultrasonic sensors are used in all manufacturing fields, including quality control, process Both control and detection have great potential for development.
[ad_2]