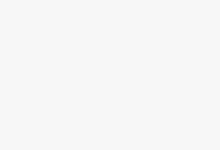
Barcode Warehouse Management Solution (WMS)
[ad_1]
After the barcode is introduced into the warehouse management system, the steps of manually writing bills and sending them to the computer room for input are removed, and the shortcomings of outdated and lagging warehouse information are solved. No matter where the item goes, we can track it automatically. The combination of bar code technology and information technology helps companies make reasonable and effective use of warehouse space. The bar code warehouse management system provides customers with the best service in a fast, accurate, and low-cost manner. The warehouse management information system software is powerful.
Co-pay barcode warehouse management solution introduces barcode technology into warehouse management, and automatically collects the data of each operation link such as warehouse arrival inspection, warehousing, outgoing, allocation, warehouse shifting, inventory counting, etc., to ensure The warehouse manages the efficiency and accuracy of data input in each operation link to ensure that the company has a timely and accurate grasp of the true data of the inventory, and reasonably maintains and controls the company’s inventory. Through scientific coding, it is also convenient to manage the batch and usage status of the items.
1. Barcode warehouse management system WMS benefits
* Paperless operation reduces paper expenses;
* High accuracy of barcode recognition, reducing human error input;
* Increase the accuracy of inventory;
* Fast and efficient logistics links;
* Effective use of inventory space, reducing operating costs;
* Various statistical reports of current and historical affairs provide decision makers with accurate and useful information;
* The connection of the data exchange interface enhances the management of the enterprise’s existing application system;
* Effective inventory management and control, reducing additional purchases, while ensuring that the inventory level meets the needs of customers’ orders or production plans;
* Record the time spent by the staff to complete the work, grasp the work efficiency of the staff, and enhance the management of the staff;
* After the completion of the warehouse management system, the management of the enterprise warehouse will reach a new level, and it will provide more valuable and time-efficient analysis data for the command and decision-making of the production department;
* Convert a large amount of paper text information required by the receipt into electronic data, which simplifies the future query steps. The staff no longer need to manually browse and find various registers and receipt books, just input
Query conditions, the computer will find the required records in a short time and display the content on the screen, which greatly speeds up the query.
* Improve the speed and accuracy of production data statistics, and reduce the difficulty of the work of summary statisticians.
Two, solution ideas
(1) Production plan and purchase plan
The production department formulates a production plan based on the sales order, and the purchasing department generates a purchase plan based on the production plan and inventory, and issues it to the supplier.
(2) Supplier label
We recommend that suppliers stick bar code labels on the outer packaging of their products to identify the category, batch, and quantity.
There are several ways to generate:
A. Suppliers purchase barcode printers to print and paste by themselves;
B. When the purchase plan is released, print the label and send it to the parts supplier together with the order sheet (the supplier can be requested to purchase).
(3) Receipt of raw materials
If the material is delivered, if there is a prescribed barcode label, the warehouse manager will receive the goods; if there is no barcode label, according to the delivered product, print the corresponding barcode label and paste it.
(4) Raw materials are put into storage and put on shelves
Scan the barcode on the shelf and the barcode on the material box, upload the system after the operation is completed, and generate the material warehousing receipt.
(5) Production picking
Before the start of the production operation, the planner determines the batch number of the finished product according to the production plan, and enters the production feed list in the system with the batch number of the finished product as the unit. The picking operator scans the barcode on the packing box and the corresponding stacking position barcode. After the operation is completed, it will be in the system Import the collected data and generate the production pick list. Review the documents in the system.
(6) Into the warehouse of semi-finished products
After the semi-finished product is processed, the semi-finished product bar code label is affixed, and the warehouse manager scans the bar code on the packing box and the corresponding stacking position bar code. After the operation is completed, the collected data is imported into the system to generate a semi-finished product receipt.
(7) Release of semi-finished products
Before the start of the production operation, the planner determines the batch number of the finished product according to the production plan, and enters the production feed list in the system based on the batch number of the finished product. The picking operator scans the barcode on the semi-finished product box and the corresponding stacking position barcode. After the operation is completed, the system Import the collected data in the middle, and generate the semi-finished product picking list.
(8) Finished products enter the warehouse
After the finished product is produced, the finished product barcode label is affixed, and the warehouse manager scans the barcode on the packing box and the corresponding stacking position barcode. After the operation is completed, the collected data is imported into the system to generate the finished product warehouse receipt.
(9) Finished product out of warehouse
Enter the sales order number, the system lists the storage positions of the products in the order (the warehouse clerk can print it out and pick up the goods according to the inventory list), download the sales order to the data collector, and find the product to be shipped. Scan the barcode on the storage location and the barcode on the packing box of the product, and import the collected data into the system after the job is completed, and generate the finished product out-of-warehouse receipt.
(10) Data query and report
Perform data analysis on the data of this system, and generate various related reports, such as: inventory report, product inventory age report, return status table, inventory difference table, etc. Statistics, query and analysis of relevant data. The system can query the tracking information of products out of the warehouse, receiving, sending and receiving directions and locations according to the product barcode, model, time, plan number, warehouse, unit of dealing and other keywords, and provide the quantity of in and out of the warehouse, the quantity in the warehouse, the quantity of materials picked, etc. Statistical information is convenient for finance and suppliers to settle the payment. The material supplier can be traced through the product.
(11) Data collection program
The data collector can scan the barcode information according to the barcode compilation rules, and display the product name, model, batch number, warehouse location and other information, which facilitates the receipt, picking, inventory, and shipping of raw materials, semi-finished products, and finished products.
(12) Inventory inventory
Before the operation, select the inventory materials (raw materials or finished products, etc.) to generate an inventory receipt. After the operator downloads the inventory order to the data collector, scan the barcode and cargo location on the material package to collect data. After the operation is completed, the collected data will be collected Import the system, and the system will summarize the imported inventory data and check it with the original inventory report of the system to generate adjustment vouchers and adjustment reports.
For more detailed program consultation, please contact Hexin Technology!
[ad_2]