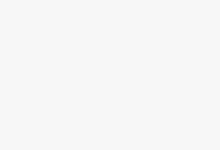
RFID production management system
[ad_1]
Shanghai Yexuan Information Technology RFID Production Management System
One: Project background
1.1 Project status
As market competition intensifies and product life cycles shorten, discrete manufacturing has become more and more sensitive to the market’s response speed. The most representative parameters related to reaction speed are reaction time and delivery date. For this reason, enterprises must adopt information technology and advanced manufacturing technology to improve their production efficiency while guaranteeing quality. This requires managers to strengthen the production process management between the enterprise resource planning layer and the process control layer.
The status quo of traditional discrete manufacturing:
The lack of a supervision mechanism in the production process, opaque production information, and difficulty in production scheduling have led to difficulties in production execution.
It cannot detect and handle product abnormalities in a comprehensive and timely manner, and cannot provide comprehensive performance indicators and management reports.
Bar codes are easy to be damaged and contaminated and difficult to read. The information storage is small and easy to copy.
The manual operation is cumbersome, the form record is prone to errors, and labor is wasted.
It is difficult to connect with existing ERP and other systems and lacks a complete traceability system.
Therefore, changing the current dilemma from manufacturing processes to automatic identification technology requires a new solution and technology to solve these problems and change the current status of low production efficiency, waste of labor, management confusion, and difficulty in traceability.
RFID technology, as an emerging automatic identification technology in recent years. First of all, it has the world’s only code mark. The tag itself has the characteristics of writing function, long-distance recognition, and strong group reading ability. It has undoubtedly become the rescuer of this dilemma and creates the possibility for the implementation of the new pipeline system.
1.2 Significance of project implementation
RFID technology has a unique identification number in the country, its fast transmission speed, good group reading ability, can still work when contaminated and damaged, long service life, and reusability determine its best choice for identification. Faced with the low production efficiency, waste of labor, opaque production process, and difficulty in information scheduling in the discrete manufacturing process, the RFID assembly line management traceability system launched by Shanghai Co., Ltd. Shanghai Co., Ltd. Electronic Technology aims to solve the above problems for enterprises.
Advantages of RFID assembly line management and traceability system:
The production information is transparent, and the managers can watch the progress of the pipeline in real time through the kanban or computer.
It can monitor in real time whether the equipment that needs to be installed on the production line is faulty, avoid duplication of labor, and alarm for product flow.
It solves the drawbacks of the original barcode, has a unique identification TID number, and can be combined with the system to establish a complete traceability system.
Increase the speed of assembly line operations, reduce unnecessary labor costs, and increase corporate profits.
Provide a complete software interface to access the enterprise ERP system.
Two: System Overview
2.1 Principles and principles of system design
This system is based on perfecting and cooperating with the enterprise’s existing software management system, and it has strong customization. Adhering to the concept of improving production efficiency, improving the production system and the follow-up traceability of the enterprise, comprehensively enhance the degree of enterprise informatization.
Install an RFID reader near each station that needs to be tested, install an RFID reader antenna at a reasonable location for each station that needs to be tested, and stick an RFID tag on some production product trays or products that need to be managed. When the product is conveyed along the assembly line to each station that needs to be inspected, the reader will automatically identify the product of the relevant station (the product information can be read: including the product batch, color, model manufacturer, etc.) and will Relevant data is entered into the system for management and scheduling. At the same time, it can be combined with bar codes to bind some important parts, so as to realize the traceability of the product quality in the later stage. Provide reminders and alarms for actions that were not operated at the previous station.
Its content mainly includes the following points
The assembled parts are monitored at each station of the assembly line.
Send an alarm signal when the assembled parts are found to be abnormal at the workstation.
The batch number of each assembled part is archived and a database is established, so that the history of the washing machine can be traced when a quality accident occurs.
System hardware architecture
The hardware architecture of the project is divided into two layers. The first layer is the RFID data collection control layer, and the second layer is the data management layer. The entire RFID system is designed to be able to operate normally in a relatively harsh industrial environment.
The expansion of the system is very easy. This system can be seamlessly connected with the control system of the factory. This system is also very convenient to connect with the factory’s MES system or ERP system. Because the architecture of this system is a small system built on the basis of a large architecture, which fully meets the overall requirements of SIMATIC PLC. The system architecture diagram is as follows.
Graphical description of the system architecture:
The first layer is composed of readers, antennas, T electronic tags, barcode handsets, on-site display screens (kanban boards), leaky wave cables, traffic light rows, etc. As the host of acquisition control, PLC can easily add various input and output devices on site. When RFID acquisition points are increased, it can be easily added through industrial Ethernet. When a large number of acquisition points are added, Ethernet communication boards can be added to meet the needs of large-scale Large-scale RFID collection points are required. And the software can complete the system re-construction work in only a few time through the programming of the configuration software.
The RFID data collection of this layer is completed by the RF four-channel reader and antenna. This assembly line RF reader can be connected to an antenna with a distance of 3 to 20 meters, and a reader with a 4-station antenna is no problem, so that the cost of the reader is greatly reduced.
In this scheme, an on-site display screen is designed as a on-site billboard to display relevant information and alarm prompts of the assembly line to help workers at the station to understand the production status in time. At the same time, each station is equipped with a traffic light row to promptly remind workers to quickly troubleshoot the fault when the current station fails during the assembly line installation process.
The second layer is the data management layer, which is composed of upper-level industrial computers. This solution uses Siemens industrial PCs with extremely high cost performance. It is a sturdy and reliable rack-mounted industrial computer. It adopts a 19-inch standard 4U rack-mounted design and is equipped with an IntelPentium Dual Core G2010 processor. It can ensure that the CPU runs at full speed for 24 hours under industrial conditions with an ambient temperature of up to 40oC. In order to ensure the capacity of the system’s small database, we choose a practical industrial PC with 16G memory and 500G hard disk in this series.
System software structure
The project software provides complete configuration development software. From the lower-level data collection to the on-site control and display, the overall monitoring of the entire system can be programmed with the corresponding configuration software at all levels.
The data collection at the lower level of the software development of this system adopts RFID systems RF, which is the middleware software of the RFID system. It can flexibly configure the configuration, adjustment, collection density, etc. of the on-site monitoring point equipment, and can also configure the data upload, instruction issuance and execution of necessary I/O signals at the collection layer.
The on-site display information and alarm board use Siemens Human Machine Interface configuration software to configure the important information display of the assembly line production process, including: various charts, production process information (planned completion statistical reports, trend graphs), and alarm prompts. If necessary, you can configure the added control functions that need to be controlled individually on site. Taking into account the characteristics of this system that collects batch number data and data management functions of the components assembled at each station of the on-site assembly line, the system does not need to be combined with the actual control of the assembly line. Moreover, this system is not large, and its management function is not too complicated. Our company uses general-purpose software to complete the development of application software for database management, upper-level data forwarding and information interaction with other systems. Through a complete server platform, a Web server extension module can be built on this platform. Provides perfect command windows, buttons, menus, toolbars and other screen elements that can be easily created with the flexibility required to adapt to changing industrial needs.
The system uses IIS7.0 + Framework4.0 + SqlServer 2008 as the upper computer (server and database) software development platform, and uses B/S or C/S architecture to build the system. The development tool is Visual Studio 2012.
Three: RFID system management design
3.1 The composition of the equipment pipeline
Five stations are selected to pilot RFID data collection and information management. After the pilot project is completed, it will be further improved and improved, and will be promoted and applied throughout the entire assembly line.
3.1.1 The five work stations are preliminarily planned as:
Station 1: The initial assembly process, the washing machine drum is placed on the tooling board
Station 2: Load the computer board into the washing machine
Station 3: The mechanical program controller is installed in the washing machine
Station 4: The reducer is installed in the washing machine
Station 5: Load the capacitor into the washing machine
The distribution of the five stations on the assembly line and the layout of the testing equipment for each station are as follows
Illustration of RFID equipment:
1) The reader antenna is installed 30-40 cm in front of the workstation.
2) One reader/writer with 4/2 antenna, respectively, installed at the appropriate workstations.
3) The barcode scanner is placed on the side of the workstation to scan the barcode information.
4) The station traffic light row is placed at a slightly higher position to display component assembly alarm information.
5) Display screen, Siemens HMI display screen, showing related information about pipeline operation
6) Leaky wave cable, as the information media medium of the bar code handset.
3.2 Assembly station inspection process
Station 1: Start assembly station
First, put 250 RFID tags into the bottom of the tooling board before putting the tooling board on the assembly line, and assign fixed numbers to the 250 tooling boards. The numbers are 0001, 0002, 0003…0249, 0250. These numbers are generally relatively fixed. It can also be changed, but less changes are recommended. Put the tooling board equipped with RFID tags on the assembly line station 1, and the reader antenna installed at station 1 automatically read the fixed number of the tooling board. At the same time, the worker at station 1 puts the washing machine drum on the tooling board. The worker scans the one-dimensional bar code on the roller with a scanner. The PLC RFID system reads the relevant information of the roller, including: product number, production date, material grade, etc., and automatically binds this information to the tooling plate number on the current station Set them together and store them in the database of the data management center as the first part of the batch to be installed. The data management center displays the bound information on the station 1 kanban. The data is shown in Table 1-1.
Repeat the above process every time a tooling board is placed in station 1, and the data center will automatically subtract 1 from the parts to be installed in the current batch number and make a judgment.
The on-site HMI display board is divided into red, yellow and green light warning area and data display area. The data center writes down the number of the first roller, and automatically subtracts 1 from the number of rollers to be installed in the batch. The red, yellow, and green lights respectively warn the status of the number of rollers to be loaded. The green light on indicates that the supply of rollers to be loaded is normal, and the yellow light indicates that the number of rollers to be loaded is small (for example, less than 3), reminding workers to prepare a new batch of rollers to be loaded . The red light indicates that the number of rollers waiting to be installed in this batch is zero, reminding workers that they must replace the rollers waiting to be installed in a new batch. If, when the next batch of rollers are put into station 1 on the tooling plate, the first roller is not scanned, and the red light continues to be on until the first roller information is scanned, the red light turns off and the green light turns on. At each station, a traffic light row is installed at the same time, and the traffic light information of the kanban is displayed simultaneously.
The monitoring process of station 1 is shown as follows:

Station 2: Computer board assembly station
When the tooling board moves to station 2, the reader antenna in front of station 2 first reads the tooling board label, indicating that the washing machine enters station 2 for assembly. Workers use a scanner to scan the barcode on the computer crate and read the batch number of the computer crate. The scanner sends the relevant data to the data management center for data binding, and stores the computer board as the first piece of the batch of computer boards. After the tooling board enters station 2 to install the computer board, there is no need to scan the barcode of the computer board box until the batch of computer boards is used up. The other process is the same as above station 1.
Station 3: Mechanical program controller assembly station
When the tooling board moves to station 3, the reader antenna in front of station 3 first reads the tag of the tooling board, and the data management center judges whether the information of the parts moved out of station 2 is normal. The normal kanban will not alarm, otherwise the kanban will alarm At the same time, the traffic light row of station 2 displays the same information as the kanban. Workers in station 2 will quickly recheck and inspect the removed washing machine, and release it after passing the test. When it is unqualified, it shall be dealt with according to the treatment method of unqualified product. The other monitoring functions of station 3 are the same as those of station 2.
Station 4: Reducer assembly station
Same station 3
Station 5: Capacitor assembly station
3.3 Online data management function
After the assembly line runs the RFID system, it dynamically collects information about the entire assembly process in accordance with the production plan issued by the company’s ERP system, and accurately counts the entry and completion time of each assembly process, providing accurate data for timely adjustment of the assembly line’s production capacity. At the same time, the batch number of the parts installed at each station will be recorded and stored in the historical file to provide direct data for tracing the quality of the product. Management functions include:
Monitor the assembled parts at each station of the assembly line;
Send an alarm signal when an abnormality is found in the assembled parts at the workstation;
·Archive the batch number of each assembled part and establish a database, so that the history of the washing machine can be traced in the event of a quality accident;
·Whether it is a normal assembly plan or a temporary increase/change assembly plan, the management of the assembly line will automatically change with the plan change. The above management functions remain unchanged;
·Accurately compare the ERP BOM list with the actual assembled parts, and automatically monitor the accuracy of the installed parts at each station;
·The pilot project has considered that when the monitoring stations are expanded to a full assembly line in the future, the RFID system functions are expandable, and RFID devices such as readers can be easily expanded. Software programming can be completed through middleware software configuration. It is also very convenient if you want to link this system with the upper-level MES or ERP. The software and hardware of the system can meet the requirements of system expansion.
3.4 Problems found in the parts to be installed on the workstation
When the assembler finds that there is a problem with the quality of the component to be installed, the problem component should be moved away and placed in the non-conforming product area. At the same time, the barcode of the station is scanned with a scanner, indicating that the station has found a problematic part, and the data management center receives it. Station bar code information, record the time of the problematic part at the station, the batch number of the problematic part, and automatically subtract 1 from the total number of the batch number.
3.4.1 Problems found after installation of station components
When the washing machine at the current station moves to the next station, the data management center will automatically check the information of the components installed at the previous station. The information is unanimously released. Inconsistent, the worker removes the unqualified washing machine from the assembly line, and then scans the barcode of Station 2 with the scanner of Station 2, and the data management center receives the barcode information of Station 2 and also receives the information of the electronic label of the tooling board of Station 3. , Which means that the washing machine is offline and will be treated as a non-conforming product. The data management center will re-count the number of washing machine assembly plans.
3.4.2 Irregular arrangement of washing machine installation
When the assembly sequence of the washing machine is arranged irregularly or the assembly sequence of various washing machines is mixed and matched, the assembly line board will display the model of the washing machine to be installed and the batch number of the parts to be assembled. Workers are also reminded to check whether the batch number of the assembled parts is consistent with the batch number displayed on the kanban, and to scan the first part batch number in a consistent manner. Then the steps are the same as the monitoring process of each station above. Inconsistent, report to the assembly line leader to check the reason.
3.4.3 Missing parts
If the worker at the next station discovers the missing parts in the previous station, he should immediately notify the worker at the previous station, and the worker at the previous station will handle it according to the abnormal situation handling function 2.
3.4.4 Sudden shutdown of assembly line failure
When such problems occur, the RFID system automatically saves the information of the current stations of the assembly line, and at the same time, the assembly line board displays the relevant information of the five stations of the current assembly line.
3.4.5 Tooling board label failure
When the system finds that the tooling board is faulty, the assembly line board will give an alarm message, and the traffic light row where the faulty board is located will display the fault information. At this time, the workers at the work station should immediately use the barcode scanner to scan the barcode of the tooling board used in emergency situations affixed to the tooling board. Because this barcode has been bound to the tooling plate label, scanning this bar code can be used to replace the tooling plate label in an emergency, which has the same effect as the label.
3.4.6 Station reader failure
When the station reader fails, the system maintenance personnel are required to quickly replace the spare reader. During the period from the failure to the replacement of the new reader, the workers at the work station should use the bar code scanner to scan the emergency bar code of the tooling board. The time to replace the reader will not exceed half an hour, and it will not add too much work to the individual.
3.4.7 System host computer (server) failure
System server failure is a major system accident. This kind of accident should be avoided as much as possible. At this time, the PLC works normally. The data is temporarily stored in the CPU memory of the PLC, and the data is automatically sent to the upper computer after the upper computer is repaired.
3.4.8 Industrial Ethernet failure
Ethernet failure may occur in the following situations:
·The Ethernet connection of individual readers is damaged so that the readers cannot transmit data, so use barcode handsets instead of readers.
·The Ethernet connecting the PLC to the two readers is faulty. At this time, the Ethernet connected to the leaky cable acts as a backup network. The barcode handset at each station replaces the reader’s antenna and reads the tooling board as a backup Barcode.
·The Ethernet connected to the leaky wave cable is faulty. At this time, if there are enough parts in each station, the station reader will still automatically decrement by 1, which does not affect production, but the assembly line kanban will alarm, and the station traffic lights will be arranged at the same time An alarm is displayed, and the Ethernet fault in this segment should be repaired urgently at this time. If there are few parts to be installed at the station, an emergency alarm should be issued to stop the assembly line.
4: Cases of some projects of Shanghai Yexuan Information Technology
[ad_2]