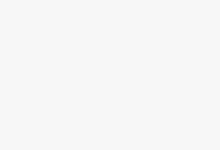
Sanrui Information-RFID Warehouse Management System Solution
[ad_1]
1. The advantages of a warehouse management system composed of RFID technology
RFID technology has unique performance, so it has the following advantages in warehouse management:
Automatic recognition:
In the RFID warehouse management system, all objects in the warehouse that need to be identified are affixed with RFID electronic tags, and the RFID electronic tags also record information corresponding to their status, as long as the information of the RFID electronic tags is read through the reader, The management system can determine the object based on the unique number read that cannot be modified. The whole process does not require manual intervention.
Quick operation:
RFID identification technology is a non-visual identification technology. It uses the inquiry mechanism of radio signals to interact with RFID electronic tags through RFID readers (such as handheld readers, forklift truck readers), so the identification process It is quite fast.
High reliability:
In the operation of the RFID warehouse management system, the information transmission and changes in the intermediate process are completed automatically, and there is no man-operable entrance, which can completely avoid the error of the information in the intermediate process due to manual operation, so the reliability of the information is improved. sex.
Good monitoring:
Because the RFID warehouse management system has the function of automatic object identification, any operating system for warehouse operations can know it. Through the alarm of the error operation alarm subsystem in the system, it can immediately warn the staff and urge them to correct the error operation. Otherwise, the alarm status will not change and will be automatically recorded into the database.
Obviously improved efficiency:
On the basis of eliminating manual information change and active error prevention, the entire warehousing operation will become smooth, with tight links, orderly operations, conclusive credentials, and evidence-based records. Therefore, the work quality can be greatly improved, and the work efficiency can be greatly improved.
2. The basic working principle of the system
1. The initial process of the system
In order for the RFID warehouse management system to be able to identify all warehouse areas, cargo locations, pallets and forklifts, as well as staff, it is first necessary to attach RFID tags to all objects in the warehouse that need to be identified. A UHF 915MHz RFID tag is attached to the entrance and exit of each warehouse area so that the forklift can identify the warehouse area when it is moving; a high-frequency (UHF) 915MHz RFID tag is buried on the ground of each cargo bay. To enable forklifts to identify the cargo position when loading and unloading; affix UHF 915MHz RFID tags to each forklift, so that the system can identify the moving forklifts and pallets with the readers installed at the passages and exits ; Issue tag-style identification cards embedded with high-frequency (HF) 13.56MHz RFID tags to all warehouse staff, so that the system can identify who is operating a certain smart handset, a certain forklift, etc.
When staff in different positions want to start work, they must use their own tag-style identification cards to read and verify the system before they can enter the system. For example: After the forklift driver opens the on-board terminal equipment, he needs to check the “Inbound Operation Sheet” or “Outbound Operation Sheet” handed to him by the system, and he must first perform the system login operation, that is, use his own tag-type identification card to the vehicle. The RFID reader reads it. Once the system is successfully verified, the forklift driver can immediately enter the system to see the “Warehousing Operation Sheet” or “Outgoing Operation Sheet” handed over to him by the system, and then the staff can proceed according to the document information operate. Smart handset operators also need to use the smart handset to scan their own electronic tag work permits when they start to enter the system, perform verification and login, and then start working after being confirmed by the system.
2. Receiving process
The goods sent from the factory to be put into storage are first placed in the receiving area of the warehouse to wait for storage preparations. First, the receiving area manager outputs RFID labels corresponding to the packaging and quantity of the goods in the warehouse through the fixed RFID terminal equipment RFID label printer in the receiving area according to the packaging and quantity of the goods, and completes the RFID label configuration.
Then the staff will affix the corresponding label to the goods according to the packaging. Pallets or large boxes use UHF tags, and internal small boxes or goods use HF tags. Then, the staff uses the mobile RFID terminal equipment smart RFID handset to associate information with each labeled goods. The storage location of the goods is allocated by the warehouse management system (WMS) to complete the preparatory work before warehousing. At this time, the receiving area administrator has also assigned the goods that can be stored to a forklift driver. The forklift driver can see the job order issued to him from the touch system terminal installed on the forklift he drives.
3. The process of warehousing and shelves
The forklift driver will carry the corresponding goods to the designated receiving area according to the warehousing operation order information displayed by the mobile RFID terminal device installed on the forklift. At this time, the RFID fixed reader/writer installed on the forklift will paste the goods on the load. The RFID tag reads the information and automatically determines whether the goods carried are correct. If it is not correct, the on-board equipment will immediately call the police.
Then the staff drove the forklift to transport the goods to the designated warehouse area. Because the entrance and exit of each warehouse area are affixed with RFID tags, the system can automatically identify whether the forklift has driven the wrong warehouse area. If the forklift drives in the wrong storage area, the system will also immediately alarm through the on-board equipment. Similarly, the system can also automatically recognize whether the forklift has entered the correct cargo position.
Only after the forklift driver unloads the goods in the correct storage location (storage area, cargo location), can he press the “Finish” button on the on-board equipment to complete the warehousing and shelving work and leave the storage area normally. If there are still goods in the warehouse on the forklift, when the forklift has to leave the warehouse area and pass the entrance and exit of the warehouse area, the on-board equipment will always alarm. At the same time, the system will automatically cancel the “finished” operation of this storage. At this time, only after the forklift driver corrects the wrong action, the system will stop the alarm and return to normal, otherwise, manual intervention will be required to return to normal.
4. Picking and outgoing process
When the forklift driver receives and confirms the outbound work order information on the vehicle-mounted mobile RFID terminal device, he must carry the corresponding goods to the designated storage location based on the outbound work order information. At this time, the system can automatically identify whether the forklift is driving the wrong way. Library area. If the forklift drives the wrong storage area, the system will immediately alarm through the on-board equipment. When the forklift driver is loading the goods out of the warehouse, the RFID reader installed on the forklift will read the information on the RFID tags affixed to the loaded goods, and automatically determine whether the carried goods are correct. If it is not correct, the on-board equipment will immediately call the police. Once the forklift enters the storage area, it must be driven out without loading the unloaded goods, otherwise it will call the police.
Then the forklift driver drives the forklift to transport the goods to the designated shipping area to be inspected. After unloading the goods, press the “Finish” button on the on-board equipment. If he does not transport the outbound goods to the outgoing inspection area, the system will not let him complete the operation.
5. Shipping process
In the shipping waiting area, first, the staff will use the mobile RFID terminal equipment smart RFID handset to check and confirm the shipment order information for each labeled goods. Then, the staff will take back the RFID tags affixed to the goods placed in the warehouse to be inspected.
Finally, the staff uses a fixed RFID terminal device RFID reader to perform a batch processing operation of disassociating the recycled RFID tags, so that the RFID tags can be reused again.
6. Inventory process
Because the inbound and outbound all have manual participation, the system cannot ensure that the location of the goods in the warehouse does not go wrong. In view of this situation, the only way to find out the existing problems is to use the mobile smart RFID handset to carry out the inventory of the warehouse locations (or all the warehouse locations) that may have errors. When taking inventory, staff use mobile smart RFID handsets to read the RFID tags on the cargo space and the goods in the cargo space. If there is an error, the system will immediately alarm and point out the correct location of the misplaced goods. Then the forklift driver will immediately put the misplaced goods back to the correct location.
7. Abnormal shipment monitoring process
In order to prevent the situation that the goods are sent out of the outgoing inspection area before the completion of the shipment process, fixed RFID readers are installed at each external exit of the warehouse. If the goods have not completed the shipping procedures, they will be posted on the pallet at this time. The RFID tag is not disassociated. When the goods are going to pass the exit, the fixed RFID reader can read the RFID tag information on the goods, and the system immediately alarms.
Three, the composition function of the management system
1. Receiving management subsystem
The receiving management subsystem in the RFID warehouse management system is mainly based on the receipt information in the system database to carry out the pre-processing of goods warehousing. Finish the work of labeling, labeling, information association, and receiving check and confirmation of the goods in the warehouse.
2. Storage and shelf management subsystem
The warehousing and shelf management subsystem in the RFID warehouse management system mainly completes the allocation of the storage location of the warehousing goods. The system guides the staff to store the warehousing goods in the designated storage location according to the location information of the goods. The system uses the vehicle-mounted RFID mobile terminal device to display the warehousing work order information, and uses the vehicle-mounted alarm device to point out the wrong operation of the staff.
3. Picking and outbound management subsystem
The picking and outbound management subsystem in the RFID warehouse management system mainly completes the determination of the outbound goods. The system guides the staff to the designated storage location and transports the outbound goods to the outbound waiting area according to the information of the outbound goods. . The system uses the vehicle-mounted RFID mobile terminal device to display the information of the outbound work order, and the vehicle-mounted alarm device points out the wrong operation of the staff.
4. Shipment management subsystem
The shipping management subsystem in the RFID warehouse management system is mainly based on the shipping order information in the system database for the final processing of the warehouse. Complete the work of receiving bids, canceling information association and shipping verification and confirmation of outbound goods.
5. Inventory management subsystem
The inventory management subsystem in the RFID warehouse management system is mainly to complete the statistical query of the receipt, inventory, shipment, forklift movement and other information in the system database. Because the warehousing process has adopted an automatic monitoring mechanism, manual operations are no longer required for the main inventory work.
6. Warehouse forklift personnel management subsystem
The warehouse forklift personnel management subsystem in the RFID warehouse management system is mainly to complete the coding management of warehouse areas, cargo locations, forklifts, and personnel, and the production of corresponding RFID tags. All objects in the system can be recognized and confirmed by the system.
[ad_2]