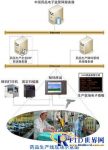
Beijing Huonbode Pharmaceutical Warehousing and Logistics Solutions
[ad_1]
1 Introduction
At present, the types of warehouses in the pharmaceutical industry are mainly divided into pharmaceutical raw materials and finished products warehouses in production logistics and strategic warehouses in sales logistics. Most companies prefer to adopt three-dimensional warehouses with racks combined with narrow aisles and high-drive three-way stacking forklifts. Models, such as Xi’an Janssen, Tonghua Dongbao, Qihuadun Pharmaceutical, Sino-US SmithKline, etc. On this basis, according to actual needs, as far as possible the introduction of foreign advanced warehousing management experience and modern logistics technology, effectively improve the warehouse storage and distribution efficiency and service quality.
2. Improve warehouse functions and gradually realize the socialization of warehouses
Accelerating the realization of the diversification of warehouse functions is an objective requirement for the development of the market economy, and it is also an important way for warehouses to increase service functions, improve service levels, enhance competitiveness, and realize the socialization of warehouses. Under the conditions of a market economy, warehouses should no longer be just a place to store goods, but should also undertake functions such as product classification, selection, sorting, processing, packaging, and sales agents. They should also become a collection of business flow, logistics, and information flow. Commodity distribution center, circulation center. Now in developed countries such as the United States and Japan, the original warehouses are basically transformed into commodity distribution processing and distribution centers. Based on Yunnan Shuanghe’s current scale and corporate strength, companies should transform their existing warehouses into stock-based distribution centers for common distribution. After commodities enter the distribution center, they are first classified and stored, and then sorted, inspected, and inspected according to the user’s order requirements. Finally, it is delivered to various chain stores and medical units. This kind of distribution center operation is simple, only need to unbundle the purchased goods, and each warehouse area is stored with pallets as a unit.
3. Establish a complete warehouse management system
The recent bankruptcy of Kmart in the United States once again warned that companies that have problems with inventory management will eventually find it difficult to avoid bankruptcy. Many subsidiaries acquired by Double Crane Pharmaceuticals also suffer from poor inventory management of varying degrees. Various overdue and slow-moving inventories and receivables make these state-owned commercial companies difficult. Therefore, the construction of Yunnan Shuanghe logistics management must solve the low efficiency status of inventory management, reduce inventory costs and inventory slow-moving risks, and solve the problem of information transmission in the entire management chain.
Successful experience shows that WMS is a low-risk, high-return option, and its payback period is usually less than one and a half years, and some even within one year. It is precisely because of this that WMS is favored by the world and is widely used in Fortune 500 companies. Its application industries are also very wide, including the pharmaceutical industry, food industry, printing factory, fashion and apparel industry, publishing industry, telecommunications industry and hardware manufacturing. Wait. Use the world’s latest and most advanced information management system to strengthen the company’s internal management and control capabilities, rationally and scientifically integrate the supply chain that runs through all aspects of the company’s production, supply and marketing, and secure, secure remote data by creating a highly shared data platform. Efficient transmission and processing provide decision-makers with effective prediction, control and analysis of basic data. A study conducted by the “Warehouse Education and Research Association” showed that the best warehouse operation mechanism can achieve 99.9% order accuracy and 99.2% punctual shipment rate. “Zero error” is considered an acceptable goal.
If the logistics hardware equipment is like the human body, then the logistics software solution constitutes the human wisdom and soul, and the combination of the soul and the flesh is the complete human. In the same way, if you want to build an advanced logistics system and improve the level of logistics management, logistics equipment alone is not enough.
At present, the widespread application of Internet technology makes global business models undergoing unprecedented changes. Every enterprise is facing the challenge of rebuilding supply chain management, especially logistics processes. Only by restructuring or optimizing supply chain management and reducing operating costs can companies have sufficient competitiveness to survive in their respective markets. The advanced and mature logistics information system is the integration of many industry experts’ years of experience. It is the fusion and crystallization of good management ideas. It can help companies optimize business processes, reduce logistics costs, improve the transparency of the supply chain, and ensure accurate and timely delivery of goods. Improve the level of customer service, and thus obtain customer loyalty, which is exactly where the core competitiveness of the enterprise lies.
According to the data provided by the Ministry of Information Industry of my country, the logistics cost of Chinese enterprises is about 18%, while that of the United States is only 9%. With the help of good logistics software, the logistics cost of Chinese enterprises can be reduced to about 10%. Warehouse management software such as EXE, which supports online and offline warehouse management, is suitable for the needs of e-commerce. Another example is the warehouse management software provided by the Australian PULSE Logistics System. In addition to managing the quantity and location of the inventory, it also pays more attention to optimizing various resources in the warehouse, such as human resources, logistics equipment resources, etc., through RF equipment and scanners. And other material handling equipment to realize the operation management of goods, personnel, and logistics equipment. Practice has shown that the use of PULSE warehouse management system brings significant benefits to customers: it can shorten picking time by 50%, reduce direct labor costs by more than 40%, increase warehouse space utilization by 20%, and reduce inventory levels by 15%. The reported warehouse errors dropped to zero.
Yunnan Shuanghe can selectively learn from these softwares according to its economic strength and development needs.
4. Reduce work links
Every operation link requires a certain amount of living labor and materialized labor consumption. The use of modern technology and scientific management methods to reduce some operation links as much as possible is not only conducive to speeding up the progress of the operation, but also conducive to reducing costs.
(1) Adopt the “two-on-direct dial” method.
Direct dial from the factory. Companies can directly pick up the goods at the pharmaceutical factory according to the order requirements, and ship the goods directly to various stores or sales units without going through the warehouse after acceptance.
Just dial directly. For goods shipped from other places, companies can arrange short-distance transportation in advance, distribute them at the side of the original vehicle, load other vehicles, and transfer the goods to the receiving unit, eliminating the need for warehouse-in and then-transport procedures.
The above two methods not only reduce all the operations in the warehouse, but also reduce the storage cost.
(2) Reduce loading, unloading and handling links
To improve loading and unloading operations, it means trying to improve the mechanization of loading and unloading operations, and it is necessary to realize the continuity of operations as much as possible, so as to improve loading and unloading efficiency, shorten loading and unloading time, and reduce logistics costs. The rationalization measures include:
Prevent and eliminate invalid operations. Minimizing the number of loading and unloading, striving to improve the purity of the items being loaded and unloading, and choosing the shortest operation route can prevent and eliminate invalid operations.
Improve the loading and unloading activity index of items
When stacking items, enterprises should consider the convenience of loading, unloading and handling operations in advance, put the classified items on pallets and store them in units of pallets, which is convenient for loading, unloading, and handling, as well as keeping the items properly.
Actively and prudently use the principle of gravity to achieve labor-saving loading and unloading operations
Loading, unloading and handling causes vertical and horizontal displacement of items, which can only be completed by doing work. As my country’s current level of mechanization of loading and unloading is not high, many still require manual operations, and the labor intensity is high. Therefore, gravity must be used for loading and unloading under conditions. Loading and unloading on trucks makes goods move on inclined conveyor belts (boards), which can reduce labor intensity and energy consumption.
Carry out correct facility layout
The “L” and “U” layouts are adopted to ensure the single flow direction of the items, which not only avoids the roundabout and backflow of the items, but also reduces the handling links.
5. Reduce the cost of returns
With the return of goods, there will be a series of logistics costs, the costs incurred by the damage or unsalable goods of the returned goods, and the personnel costs required to process the returned goods. Moreover, due to the small number of returned goods and the wide variety, the delivery costs are There is a tendency to increase, and the processing business is also very complicated. These expenses constitute an important part of the logistics costs of enterprises and must be controlled.
To control the cost of returns, we must first analyze the reasons for returns. Generally speaking, as long as you grasp the sales status of the company’s products in the store and the customer’s order status, make short-term sales forecasts, and adjust the number and types of the company’s products can fundamentally solve the problem. Return phenomenon caused by the user. In addition, the reason for the return should be found from the perspective of the company. In order to pursue the largest sales target, the company always sells the product to the end user, regardless of the actual sales status of the product and the possible problems in the sales, resulting in circulation in the warehouse. Increases, sluggish sales, and high return costs. Therefore, companies should change their goal strategy of one-sided pursuit of sales. While tracking the final demand trends and circulation, they should implement sales promotion strategies to achieve the increase in final demand.
Associated with the above problems, in order to fundamentally prevent the cost of returns, companies must also change the employee performance evaluation system, that is, not based on employee’s monthly sales as the basis for rewards and punishments, but on the basis of employee’s annual and monthly Average sales are used as an incentive standard, so that operating efficiency can be improved while preventing returns. Of course, the system must also clearly divide the responsibility for returning the goods, correct the work attitude of the employees, and deliver the goods accurately and accurately according to the user’s requirements.
6. Other specific operational requirements
(1) Commodities that have undergone strict quality inspections should be stored in different areas according to drugs and non-drugs, prescription drugs and non-prescription drugs, internal and external drugs, and dangerous goods. The refrigerated medicines are stored at the required temperature, the cool storage is less than 20℃, the normal temperature storage is 0–30℃, the suitable temperature range is 60%-75%, and the temperature range is 2-10℃. Check and adjust in time in the morning and afternoon.
(2) The stacking is neat, the five distances are reasonable (bottom, wall, top, column, space), no inversion.
(3) Different batch numbers are not mixed. When it is unavoidable, the mixing time limit shall not exceed 1 month.
(4) Special management drug warehouse/counter, double locks, special account records, and account items match.
(5) Clean the warehouse regularly to keep the warehouse tidy and orderly. Labor tools and packaging items are placed in designated locations.
(6) Carry out regular maintenance inspections on the commodities in the warehouse, keep a good maintenance record, and notify the Quality Management Division as soon as possible for the commodities with quality problems.
(7) Strictly control the quality of the outgoing warehouse, and make a good review record account.
(8) The returned goods should be managed by a dedicated person and stored in the return area, and the re-quality acceptance procedure must be carried out, and the account must be recorded. Only qualified products can be entered into the qualified product library, and those with quality problems can be entered into the unqualified product library.
(9) The unqualified products are stored in the unqualified product warehouse area for controlled management, reported in accordance with the procedures, and the reasons are identified and handled in a timely manner.
7. Cultivate warehousing technical talents and strengthen logistics management
To transform, we must start with the introduction of high-quality talents and the training of corporate employees. While widely absorbing useful talents from the society, we must also accelerate the improvement of the business technology and moral quality of existing personnel, and establish a high-quality and high-tech content team. The workforce.
8. Speed up the establishment of a modern enterprise system and the implementation of the ISO9000 family standard management model
Realizing the integration of modern logistics functions, the systematization of services and the standardization of operations are inseparable from the constraints of the system, so it is very important to establish a modern enterprise system as soon as possible. At present, the storage of Yunnan Double Crane has formed the phenomenon of drag, push, laziness, and laziness. There is no separation of responsibilities, powers and benefits. If you want to break the old concept, you must import a strong market economy concept, and ideologically establish and strengthen the awareness of reform and opening up. In terms of style, we must establish a sense of vigorous behavior and spirit of hard work, etc., replace the old management model with a modern enterprise management system, and standardize every operation link, procedure and responsible person.
[ad_2]