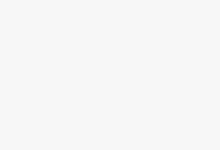
Dongfeng Motor: Electronic Management Solution for Vehicle Storage
[ad_1]
The business departments involved in the electronic management project of the whole vehicle storage of Dongfeng Motor Co., Ltd. are: the assembly operation department of the production department of the automobile branch, the inspection storage and transportation department and the marketing department of the sales company. It is a complete warehouse management business line starting from the off-line of the products of the General Assembly Operations Department to the departure of the commodity trucks.
The solution is based on the powerful logistics management system of ES/1 Logistics products, using ES/1’s own development platform, according to the characteristics of the automotive industry warehousing and logistics management, developed and formed an international management level, second to none in the domestic automotive industry Complete vehicle warehousing and logistics management solutions.
The solution is centered on the automation management of vehicle warehousing and transportation management, and can be extended to automobile production management, inventory management, sales management and financial management, and can be arbitrarily extended to ES/1 Logistics and ES/1 Manufacturing to form a car The overall solution for industry informatization.
The solution manages all warehouse inventory through a full range of barcode scanning instead of manual entry, realizes automatic suggestion of storage location and automatic suggestion of storage location according to the rules, and achieves the management effect of maximizing the use of storage space and avoiding reversing in the warehouse. Reversing tracking and long-distance transportation tracking between warehouses are used to control vehicle transportation time and avoid vehicle losses, thereby greatly improving the management level of vehicle logistics in the automotive industry and reducing huge management costs.
The program starts with production management, adopts the repetitive production model most suitable for the automotive industry to manage the schedule of production operations, and automatically generates the corresponding relationship between the vehicle model and the chassis number through this plan, without manual maintenance.
The program manages sales orders, waybills, sales invoices, accounts receivable, and can manage and control the inventory in the dealer’s warehouse to ensure the smooth flow of corporate funds and avoid financial risks.
Demand characteristics of vehicle warehouse management and logistics management:
1. Serial number management: Each car of each model has its own chassis number, engine number, and VIN code, and they correspond one by one.
2. Reversing management: There is a considerable distance between the production line temporary storage warehouse and the vehicle departure warehouse, and the time and personnel of reversing must be managed and controlled.
3. The whole vehicles are parked in different areas in the depot according to the series.
4. In the standard warehouse area, the whole vehicle can only be placed in the same warehouse of the same model, and the color must be the same.
5. The length of the storage locations in the storage area may be different. Since the length of different vehicles of different models is also different, the relationship between the number of vehicles stored in the storage area needs to be calculated and managed.
6. The vehicle warehouse has a large area and is relatively difficult to manage. Therefore, the use of space is limited by manual management and waste is large. Computer management is required to achieve the greatest possible use of parking space.
7. The delivery of the whole vehicle is based on the principle of first-in, first-out. However, due to the limitation of manual management, the information is not accurate and timely. At the same time, due to the influence of various related businesses, the vehicles cannot be delivered in order according to this principle. Reverse a lot to drive out the designated car.
8. When the vehicle is sold, it is necessary to apply for the waybill, and to track the arrival of the vehicle to the destination, and to calculate the freight.
9. The entire vehicle management process is complex, including adjustment, inspection, reversing, new vehicle preparation, sales, borrowing, repairing, returning to warehouse, unpacking, etc., and it is difficult to standardize management.
10. A large number of timely business reports and information are needed to support business operations, and a large number of accurate and timely management reports are needed to provide decision support.
Among the above points, the most difficult to manage is the vehicle warehouse, which is more difficult to manage, and there is also a big gap between good and bad management. Poor management: the same car models are mixed in different colors, and the space is not fully utilized. There are vacancies in the front, rear, and middle, and it is difficult to park in a first-in-first-out manner if they are not parked at intervals. Good management: the same model, the same color, and the same row, make full use of space, compare the length of the vehicle with the length of the storage location, first in, first out is very smooth.
Functions and features of the solution:
1. All vehicles are managed by barcodes, and the management of vehicle entry and exit are all realized through barcode scanning.
2. After the warehousing is scanned, the warehousing suggestion sheet is automatically generated and printed according to the rule setting system, and the driver can enter the warehouse completely according to the location specified by the warehousing suggestion sheet, without manual intervention.
3. It is recommended to ensure that the same model of the same color is placed in the same row in accordance with the rules.
4. It is recommended to calculate the storage quantity of the storage location according to the length of the vehicle and the storage location to maximize the utilization rate of the warehouse space.
5. It is recommended to set a certain warehouse area or the type of vehicle types stored in the warehouse according to the rules.
6. The warehousing suggestion automatically finds the location according to the priority of the set location to ensure that the vehicles are placed in a compact and orderly manner.
7. According to the principle of first-in, first-out, the system will automatically give out suggestions for the models to be out of the warehouse according to the time sequence of the vehicle’s entry time. The driver will receive the car keys and pick up the car in order according to the exit suggestions.
8. Scan the barcode of the delivery order and the barcode of the whole vehicle when leaving the warehouse, and automatically correspond to the receiving unit and the vehicle information mentioned.
9. Waybill management can track the status of each vehicle in transit, and check whether the actual arrival date and return date of the vehicle meet the date requirements calculated by the system.
10. The repetitive production model most suitable for the automotive industry is adopted to manage the schedule plan of the production operation, and the corresponding relationship between the vehicle model and the chassis number is automatically generated through this plan, without manual maintenance.
Through the above scheme, it is possible to manage all the vehicle inventory placed in the dealer’s warehouse, manage the sales information of all dealers and direct customers, so that the enterprise has a good grasp of market information, and it is convenient for the managers to make correct and timely management decisions.
[ad_2]