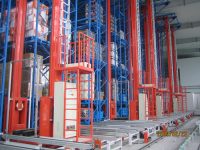
E-commerce warehouse and distribution integrated RFID solution
[ad_1]
1 Project introduction
1.1 Project background
In my country, professional warehousing and logistics services are developing in a hot wave. On the one hand, customers have higher and higher requirements for the quality of warehousing and logistics services. On the other hand, market competition is becoming increasingly fierce. Do logistics companies have modern warehousing and logistics management concepts and core competition? Advantages seem to be extremely important. Only with innovative ideas can we lead step by step. We advocate the combination of advanced information network technology and modern warehousing and logistics technology to establish comprehensive services for modern warehousing and logistics management. With the vigorous development of our economy, especially the rapid development of IT technology, logistics has to develop even more. It helps companies save logistics costs and improve logistics efficiency.
The current third-party warehousing and logistics services generally have the following problems, and the equipment system is backward: Generally, third parties only use equipment such as shelves, simple conveyor lines, paper picking sheets, etc. Higher level. Backward operation methods: Most companies are still in the original management state with manual operations as the mainstay, with low sorting efficiency and high labor costs. Backward information management: Many companies currently do not have their own warehouse management systems, or they do have warehouse management systems but they are an island of information. They have no docking with customers’ systems and express delivery systems, and no integrated warehouse equipment, which prevents them from optimizing business processes. Improve the efficiency of warehouse access and other functions.
In view of the above situation, Ziyue Technology relies on years of hardware foundation and rich experience in warehousing management systems to create e-commerce warehouse and distribution integrated management information system solutions for customers. The system introduces intelligent terminals with barcode scanning or RFID scanning to carry out operations such as storage, storage, and inventory anytime and anywhere, so as to realize the paperless management of the warehouse. The system can realize the real-time business management of each link of the enterprise’s warehouse management until the business process is processed, which improves efficiency and reduces errors, so that managers can understand the status and problems of each link in a timely manner, and deal with them in a timely manner. The upstream of the system is docked with the customer management system, and the downstream is docked with the express management systems to achieve seamless integration of the logistics industry chain, simplify tedious system operations, reduce missed operations and wrong operations, and improve business process efficiency.
1.2 Project goals
For the construction of an integrated management information system for e-commerce warehousing and distribution, we propose the following construction goals:
1. Use the computer information system to support the processing of warehouse management information to the maximum extent, give full play to the effect of man-machine collaboration, and reduce the company’s dependence on employee skills and experience.
2. It can not only realize the refined management of a single customer warehouse, but also realize the management of multiple customers and warehouses distributed in various places.
3. Dynamic management of goods warehousing, location allocation, storage, wave analysis, order picking, express delivery, inventory counting, etc., and the entire warehouse operation is electronically operated.
4. Optimize the order picking process, unified picking by wave, intelligently sorting orders, and improve the efficiency of order delivery.
5. Provide reports such as product information, location, inventory, inventory, order tracking, logistics tracking, customer settlement, express settlement, etc.
6. Realize the docking with many upstream online store management systems, so that the customer system data and order status are consistent with this system;
7. Realize the docking with the downstream express delivery system, and automatically apply for electronic face orders; automatically check and obtain the delivery status of orders, no need to send special personnel to check orders on the websites of various express companies.
8. The system function is extensible, and new functions can be added according to the constantly changing business management in the development of the enterprise.
9. Under the premise of meeting all needs, choose a reasonable system architecture and equipment to make the system have better performance and price advantages, fully protect your unit’s investment, and reduce the operating and use costs of the system.
2 System overall design
2.1 System network architecture
2.2 System application architecture
The system architecture adopts SOA architecture and widely adopts RESTful design. In the three-tier architecture (Presentation layer, Application layer, Data access layer), the interface layer adapts to multi-screen processing (PC , Handheld terminals, industrial tablets, etc.); the business layer widely uses message middleware, service middleware, caching and other technologies to achieve large-scale data concurrent processing; the database adopts distributed deployment, and uses vertical partitioning, horizontal partitioning, NoSQL and other technologies to achieve large Large-scale data storage and instant response.
System scalability mainly includes four aspects: platform, business, software, and hardware. Platform expansion: system supports docking with e-commerce systems, express delivery systems, and enterprise ERP systems; business expansion: the system supports the ever-increasing number of e-commerce customers and warehouse applications; software expansion: the system can add new functions according to your organization’s development needs; hardware expansion: Support the introduction of RFID, electronic tags, automatic sorters and other equipment to create an automated warehouse.
3 Warehouse management system functions
The functions of the warehousing management information system mainly include: basic data, order management, inbound management, outbound management, inventory management, after-sales, settlement, statistical analysis, and interface modules. The functional architecture is as follows:
3.1 Introduction to Warehouse Management Interface
The system design framework supports the docking of the warehouse management system with the e-commerce information system, express delivery information system, and enterprise ERP system to realize the background data interaction between the systems.
Interface function requirements to achieve
The basic data synchronization of the e-commerce system interface ensures the accuracy of interface data interaction and the stability of interface operation;
Give full consideration to special circumstances such as order cancellation, order duplication, order loss, etc., to prevent wrong or missed delivery;
Purchase order and sales order capture
Upload business data of goods in and out of the warehouse
Order status update, face order number update
Inventory result upload
Data upload for after-sales return and exchange
Courier system interface electronic note number reservation
Upload consignee information to ensure the accuracy of interface data interaction and the stability of interface operation;
Batch order logistics status tracking
3.2 Business Process of Warehouse Management System
3.2.1 Commodity storage
1. Purchase order
Your company’s goods come from customers, and store and manage goods on behalf of customers. Whether there are orders for warehousing business depends on whether there are purchase orders in the customer’s information system. If there are purchase orders, you need to grab the order and send it to the warehouse management system.
2. Arrival acceptance
After the customer’s merchandise arrives, the administrator checks the delivery note to learn about the delivery unit, product list and product quantity, and checks whether the merchandise quantity on the delivery note is true. After confirming that it is correct, use the handheld terminal to scan the barcode of the product and transfer the delivery note. The content is entered into the system, and finally the goods are stored in the designated warehouse and designated storage space.
Through the process of scanning the barcode, you can determine whether it is a new product. If it is a new product, you need to add product information to the warehouse management system and maintain the barcode number. If the product does not have a barcode, you need to print the barcode before entering the warehouse and paste it to the designated location of each product to facilitate the smooth flow of the outbound business.
3. Commodity storage
After acceptance of the product, it is ready to be put into the warehouse. The administrator uses the handheld terminal to generate the warehousing list through the receipt. The system automatically assigns recommended locations for each type of commodity. The administrator only needs to refer to the designated location to put the goods into the warehouse. Special circumstances can Modify the storage location.
3.2.2 Commodity delivery
There are extremely high requirements for delivery efficiency and accuracy. It is necessary to give full play to the role of the system and the handheld, and cooperate with manual operations to efficiently and accurately complete the delivery tasks.
At present, most of the most widely used e-commerce warehousing logistics mainly have 3 picking operation modes as follows:
Single-item picking, that is, the order of the order line 1 is picked separately. This type of order can be scanned out of the library in a different way from ordinary orders, which can significantly increase the speed of scanning out of the library, so it is recommended to handle it separately.
Set first and then divide. First gather a batch of orders and complete them in one picking task. After picking the goods, they will go to the distribution area for distribution according to customer orders.
Pick and broadcast. Similar to the second type, it also processes a batch of orders in one trip. The difference from the second type is that the seeding according to the customer’s order is completed at the same time as the goods are picked. After the goods are picked, they will go directly to the review and packaging process.
1. Distribution and delivery of sales orders
The outbound business starts with the receipt of sales orders. Sales orders come from the customer information system. Office operators need to capture customer orders from time to time until all orders within the daily deadline are captured.
After the sales order is captured, the system gives an optimized sorting process, and the priority sorting is: single product order>single product order product category>multi-product order product category number. Individual product orders are handled by dedicated personnel. After multiple product orders are sorted by the number of product categories, processing the same number of product categories in each wave can reduce the error rate.
2. Single product order delivery
When the single-product order has the same goods and the number of orders exceeds 50 or 100, use the single-product order delivery process and assign a special person to handle the delivery business. Office operators can allocate single-product orders in batches to special personnel for processing. After logging in with the terminal, the operator will only display the order tasks assigned to him, make batch appointments, print batches, batch picking, and delivery.
Description of the business process of multi-commodity order shipping:
1) When warehouse operators use handheld terminals to screen orders and generate picking orders, the system detects whether there are cancelled orders and automatically filters cancelled orders.
2) Warehouse operators use handheld terminals to screen orders and generate picking lists. The system picking lists will automatically sort the order items according to the product category, so that pickers can pick goods in batches. When picking, scan the barcode for each product, manually count the number of products, and the system will automatically remind the picking list whether the picking is completed.
3) After the picking is completed, the goods are transferred to the sorting staff (the assembly line can be used in the case of large business volume), and the order can be screened to generate the picking list, and the operation of 1) can be repeated.
4) The sorting staff prepares the box car of the order quantity of the wave, scans each item with the handheld machine and assigns it to the corresponding box car. When an order is allocated, the system will give a reminder and the sorting staff will make an appointment with the order number. , Print the order and the side note, and continue to sort until the wave is all allocated and printed. During the wave sorting process, completed orders can be transferred to the packing and weighing link with priority.
5) The packer takes over the sorted order, scans the order bar code and the product bar code through the handheld terminal, and checks whether the order and the actual quantity are correctly matched, and the packing and weighing are correct.
6) Scan to confirm the delivery, the system checks whether the order status has been cancelled, if it has been cancelled, a reminder will be given, if it is not cancelled, the delivery is successful, and the system automatically updates the order status.
3.2.3 Inventory management
1. Inventory warning
When the inventory level drops to the inventory warning line, the system automatically issues an inventory warning to notify the relevant operators.
1. Inventory allocation
Due to the large volume of goods, the warehouse is divided into a shipping area and a stocking area. The goods in the shipping area are consumed quickly. When the inventory is below the minimum inventory, the system will give an early warning. The operator can use this function to replenish the goods in the shipping area. This function is also suitable for normal commodity shifting or shifting positions.
The operator creates an inventory transfer order on the handheld terminal system. The system automatically screens the list of products with low inventory in the shipping area and gives suggestions for replenishment quantities. According to the list, the goods are transferred from the stocking area to the shipping area. After the allocation is completed, the form is perfected. data.
2. Inventory
1) The warehouse clerk fills in the inventory task on the handheld terminal system, specifies the inventory time and the scope of the inventory, and reviews the inventory task after the inventory task is determined.
2) Generate an inventory table, and the warehouse manager can take a handheld terminal to take inventory in the warehouse in real time, and enter the actual inventory quantity.
3) After the inventory is completed and the actual quantity is entered, the system automatically calculates the difference between the book quantity and the actual quantity, and the auditor will check the inventory result
4) After confirming that the inventory is correct, generate an inventory difference list (a list of products with differences).
5) Adjust the inventory book quantity so that the book quantity is equal to the actual quantity, and the system automatically generates the inbound or outbound order for the difference quantity.
Inventory counting is a special requirement. The counting table obtained by the inventory staff from the system does not contain inventory quantity information. After the inventory is completed, the actual inventory is entered into the system and the auditor will check the actual inventory count and the difference in inventory quantity.
3.2.4 After-sales
After-sales business mainly includes product return and product exchange. I have a preliminary understanding of two situations for this business, as follows:
1) In one case, the customer information system initiates a return or exchange task, the storage system needs to grab the task list, and the warehouse operator processes the task after completing the physical operation, and generates an inbound or outbound list;
2) In another case, the customer information system does not have a return or exchange task, but the warehouse receives the returned goods, the operator needs to create a return and exchange form in the warehousing system, and generate an inbound order and an outbound order after the physical operation is completed. The system uploads the relevant form data to the customer information system.
3.2.5 Settlement
The system can provide account settlement functions between enterprises, customers, and express companies, but the requirements are not yet clear.
3.2.6 Statistical reports
The system provides the following reports according to requirements, which can be modified or added as needed.
Monthly inventory report
Collection of detailed reports
Send and receive summary reports
Courier Status Tracking Form
Monthly Employee Performance Report
Shipment analysis report
[ad_2]