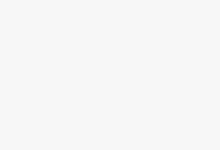
Intelligent warehouse management system based on RFID technology
[ad_1]
Chapter 1 Overview
Warehouse management plays a very important role in the entire management process of an enterprise. If timely and accurate purchase, inventory control and delivery cannot be guaranteed, it will bring huge losses to the enterprise, which is not only reflected in the increase in various management costs of the enterprise. , And it will make it difficult to guarantee the quality of customer service, and ultimately affect the market competitiveness of the company.
Traditional warehouse management generally relies on a non-automated paper document-based system to record and track incoming and outgoing goods. The internal management of the warehouse is completely implemented manually. Therefore, the efficiency of warehouse management is extremely low, and the warehouse that can be managed The scale is also very small.
With the popularization of computer applications, most of the enterprise warehouse management data materials have begun to use computer data systems for management, but the data is still collected and statistically organized by first recording on paper and then manually inputting it into the computer. This not only causes a lot of waste of human resources, but also due to human factors, the data entry speed is slow and the accuracy rate is low.
With the continuous development of the scale of the enterprise, the number of types of materials managed by the warehouse is increasing, the frequency of in and out of the warehouse has increased sharply, and the warehouse management operations have become very complex and diversified. The traditional manual warehouse operation mode and data collection method have been unable to meet the requirements of the warehouse. The rapid and accurate requirements of management have seriously affected the efficiency of the operation of the enterprise and become a major obstacle to the development of the enterprise.
550)this.style.width=550;” border=0>
The RFID-based warehouse management system introduces RFID technology into the existing warehouse management, and automatically collects the data of each operation link such as warehouse arrival inspection, warehousing, outgoing, allocation, shifting, inventory counting, etc. Ensure the speed and accuracy of data input in all aspects of warehouse management, ensure that enterprises grasp the real data of inventory in a timely and accurate manner, and reasonably maintain and control enterprise inventory. Through scientific coding, it is also convenient to manage the batch and shelf life of items. Using the system’s location management function, you can also grasp the current location of all inventory materials in a timely manner, which is conducive to improving the efficiency of warehouse management.
550)this.style.width=550;” border=0>
After adopting RFID technology, it will bring the following benefits to enterprises:
(1) Save the cost of manual data collection;
(2) Automated warehouse management operations to improve work efficiency;
(3) Reduce management costs and human errors;
(4) More precise control of import, sale and inventory;
(5) Enhance partnerships;
(6) Quickly respond to customer needs and expand product sales.
According to the analysis of Accenture Consulting Company, a member of the Automatic Identification Center, the use of RFID can:
* Reduce inventory by 10-30%;
* Increase the utilization rate of inventory space by 20%;
* Reduce labor costs by 10-40%;
* Speed up the picking and delivery speed by 10%;
* Reduce the loss caused by theft and improper storage by 50%;
* Increase sales by 2-10%;
* The transportation cost is reduced by 2 to 13%.
* Shipment accuracy reaches 95% (pallet transportation companies can exceed 99.9% accuracy);
* Billable returns are reduced by 80%;
Chapter 2 Introduction to RFID Technology
2.1, RFID technology
RFID is the abbreviation of Radio Frequency Identification, that is, radio frequency identification.
RFID technology is a non-contact automatic identification technology, which uses radio frequency signals to automatically identify target objects and obtain relevant data. It can identify objects within a distance of several centimeters to tens of meters, and can read in batches, and can identify objects, equipment, vehicles and people in stationary and moving states, thus becoming a dazzling star in the field of automatic identification. .
Barcode is an automatic identification technology that has been widely used, but RFID has obvious advantages compared with it:
(1) Quick scan
Only one barcode can be scanned at a time; the RFID reader can identify and read several RFID tags at the same time.
(2) Small size and diversified shapes
RFID does not need to match the fixed size and printing quality of the paper for reading accuracy, and is more suitable for the development of miniaturization and diversified forms to facilitate embedding or attaching to products of different shapes and types;
(3) Anti-pollution ability and durability
The carrier of traditional bar codes is paper, so it is susceptible to contamination, but RFID is highly resistant to substances such as water, oil, and chemicals. In addition, because the barcode is attached to the plastic bag or the outer packaging carton, it is particularly vulnerable to breakage; the RFID tag stores the data in the chip, so it can be protected from contamination.
(4) Reusable
Nowadays, the barcode cannot be changed after it is printed. The data stored in the RFID tag can be dynamically updated, and it can be recycled and used multiple times.
(5) Penetration and unobstructed reading
Bar code scanners must be close and without obstructions before they can read bar codes. RFID can penetrate non-metallic and non-transparent materials such as paper, wood, and plastics for penetrating communication. It does not require a light source and has a longer reading distance. But it does not recognize through conductive objects such as metals.
(6) Large data memory capacity
The capacity of one-dimensional barcode is 50Bytes, the maximum capacity of two-dimensional barcode can store 2 to 3000 characters, and the maximum capacity of RFID is MegaBytes. With the development of memory carriers, the data capacity also has a trend of continuous expansion. In the future, the amount of information that items need to carry will become larger and larger, and the demand for tags that can expand the capacity will increase accordingly.
(7) Security
Since RFID carries electronic information, its data content can be protected by a password, making the content less likely to be forged and altered, and has higher security.
550)this.style.width=550;” border=0>
2.2, RFID system
The most basic RFID system consists of three parts:
(1) Electronic label (Tag)
Electronic tags, also known as radio frequency tags and transponders, are generally composed of coupling elements (antennas) and dedicated chips.
550)this.style.width=550;” border=0>
The electronic tag is the real data carrier of the radio frequency identification system. Each tag has a unique electronic code (ID number), and the tag generally stores electronic data in an agreed format. In practical applications, RFID tags are usually affixed to the surface of objects of different types and shapes, or even embedded inside the objects, so they will be made into different shapes as needed (see the figure below).
550)this.style.width=550;” border=0>
(2) Reader
The device for reading (and sometimes writing) tag information can be designed as a handheld or fixed type; the reader can read and recognize the electronic data stored in the electronic tag without contact, so as to achieve the purpose of automatically identifying the object. Usually the reader is connected to the computer, and the read label information is transferred to the computer for further processing.
550)this.style.width=550;” border=0>
(3) Antenna: Transmit radio frequency signals between the tag and the reader.
An antenna is a device that receives or radiates radio frequency signals from a radio transceiver in the form of electromagnetic waves.
550)this.style.width=550;” border=0>
2.3 The working principle of RFID
The reader sends out a certain frequency radio frequency signal through the antenna. When the tag enters the antenna radiation field, it generates an induced current to obtain energy, sends out its own coding and other information, which is read and decoded by the reader and sent to the host computer for relevant processing.
550)this.style.width=550;” border=0>
2.4 Application of RFID
Radio frequency identification can be used to track and manage almost all physical objects, so it can be widely used in all walks of life. Typical applications include:
(1) Supply chain and logistics management
(2) Manufacturing and assembly
(3) Baggage, mail and parcel handling
(4) Identity recognition, anti-counterfeiting, access control and anti-theft system
(5) Document tracking/library management
(6) Traffic management and urban planning
(7) Service experience and CRM
(8) Spatial positioning and tracking
(9) Pervasive computing
Chapter III System Scheme
3.1 Objects and tasks
3.1.1 Warehouse management objects
The main body of warehouse management is warehouse administrator, and its management objects include:
(1) Inventory: The items kept in the warehouse are the fundamental object of warehouse management; the inventory is divided into three forms: pallets, boxes and bulk, limited to the current RFID is not suitable for management to each Small single items, so the unit of using RFID to manage items is the whole box and the entire pallet (including large single items);
(2) Storage location: the area in the warehouse that is used to store inventory items and does not overlap each other in space. Generally, one storage location can store multiple inventory; it can also occupy several storage locations for a larger inventory. .
(3) Warehouse management equipment: equipment used for warehouse management, such as forklifts, trolleys, etc.; in large, busy warehouses, these equipment need to be reasonably scheduled and located in real time to improve equipment utilization.
3.1.2 Operational tasks of warehouse management
The main tasks of warehouse management are:
(1) Warehousing (incoming inspection)
(2) Delivery (selection)
(3) Moving warehouse (replenishment)
(4) Disk library
(5) Generate various inventory reports according to needs
3.2. Overall design
3.2.1 Basic ideas
(1) Attach an electronic label to each location, which is called a location tag. When performing warehouse management operations, read the tag number to determine whether the current job location is correct.
(2) When the items are in the warehouse, attach an electronic label to each inventory management item, which is a goods label. The items to be labeled should be the entire pallet, the entire box, or a large item that is easy to install the label. When performing warehouse operations, read the label number to determine whether the work items are correct. In order to save operating costs, cargo labels are designed to be reusable. Remove the goods when they leave the warehouse and send them to the warehouse before reuse.
(3) Set up a wireless network to cover the entire warehouse operation area, and all operation data are transmitted in real time. A fixed wireless data terminal is installed on the forklift, and manual workers are equipped with a handheld wireless data terminal. The wireless data terminal has functions such as accepting operating instructions, confirming whether the operating location and cargo are accurate, and returning to the actual operating status.
(4) Use automatic guided vehicle AGV (Automatic Guided Vehicle) as a platform, install RFID readers, control equipment, and wireless communication equipment on it. AGV vehicles equipped with reader equipment will automatically count the warehouse at a set time every day, and transmit the count results to the system management center.
3.2.2 System Architecture
620)this.style.width=620;” border=0>
The warehouse management system design adopts the following three-tier architecture:
The first layer is Capture, which mainly collects data through radio frequency identification equipment and other automatic identification equipment, including location tags, cargo tags, wireless data terminals, AGV vehicles, etc.;
The second layer is Movement, that is, through wireless communication technology, the collected data is transferred to the central database, including wireless access equipment and related network equipment.
The third layer is Management, which manages the collected data, including database servers, network servers and other equipment and warehouse management system software.
3.3. System composition
620)this.style.width=620;” border=0>
The warehouse management information system consists of three parts:
(1) Warehouse management center subsystem
Responsible for the centralized management and maintenance of the warehouse management database, responsible for the formulation and ordering of purchase plans and outbound plans; print and generate various management reports.
(2) Warehouse management field subsystem
Issue storage labels, perform real-time inventory management (location management), and issue warehouse management instructions through the wireless network.
(3) Warehouse management execution subsystem
Complete specific operations such as storage, storage, removal, inventory, etc., and return to the live execution.
4. System information flow
The information flow of the system is as follows:
620)this.style.width=620;” border=0>
5. Work flow
5.1 Production and installation of location labels
Unless the location is adjusted or the label is damaged, generally the location label only needs to be made and installed once. The operation steps are as follows:
* First encode the location
* Use warehouse management field subsystem computer and RFID reader to write information such as location code into electronic tags;
* Use a label printer to print location coded text and bar code information on paper labels;
* Paste the paper label on the electronic label to generate the location label;
* Install the location label on the location. It is required to be installed firmly to prevent it from falling off; and the labels are required to be installed on the supporting beam directly below the storage location as much as possible.
5.2 Warehousing operation process
The warehousing operation process is shown in the figure below:
620)this.style.width=620;” border=0>
(1) Receipt inspection
Key inspection:
* Whether the delivery note is consistent with the purchase order;
* Whether the actual goods are consistent with the delivery note;
If it does not match, refuse to accept.
(2) Making and sticking labels
The specific method is as follows:
* Use the selected item coding scheme to code the items in the warehouse;
* Make goods label: write the coding information into the electronic label, and print the paper label at the same time (for manual verification), and then glue the paper label and the electronic together to become the goods label.
* Fixing tags on inventory: Considering the high cost of tags, in order to facilitate the recycling of electronic tags, the tags are generally fixed to the items by hanging. If it is not recycled, it can be fixed by pasting.
(3) The on-site computer automatically allocates storage locations, and gradually downloads the storage location number and corresponding item number of each operation to the wireless data terminal (handheld terminal or forklift terminal);
(4) The operator transports the goods to the designated storage location and sends the goods to the storage location after checking the location (if necessary, modify the cargo number and quantity information recorded in the location label);
(5) The wireless data terminal sends the actual status of warehousing to the on-site computer to update the inventory database in time.
5.3 Outbound operation process
See the figure below for the outbound operation process:
620)this.style.width=620;” border=0>
(1) The central computer issues the outbound plan;
(2) The on-site computer compiles the outbound instruction and downloads it to the data terminal;
(3) The operator arrives at the designated storage location according to the prompt of the data terminal;
(4) Take out the specified quantity of goods from the storage location and rewrite the content of the storage location label;
(5) The goods are transported to the exit, and the labels of the goods are removed;
(6) Send back the completed outbound operation information to the on-site computer;
(7) Update the central database.
5.4 Work Process of Moving Library
The workflow of moving the library is as follows:
(1) According to needs, the on-site computer compiles library transfer instructions and downloads them to the data terminal;
(2) The operator arrives at the designated storage location according to the prompt of the data terminal;
(3) Take out the specified quantity of goods from the storage location and rewrite the content of the storage location label;
(4) Transport the goods to the destination location, send the goods to the location, modify the location label content;
(5) Send back the operation information of moving the library to the on-site computer.
5.5 Disk library operation process
The inventory operation process is as follows:
(1) According to the inventory plan, the on-site computer sends inventory instructions to the inventory robot (AGV vehicle equipped with RFID reading equipment);
(2) The inventory robot travels according to the pre-set route and driving speed, and reads the location tag and the item tag code during the traveling process. If it is found that the two cannot match each other, it will send an alarm to the on-site computer;
(3) After the inventory robot drives once along the designated route, it sends an inventory end message to the on-site computer.
6. Discussion on key issues
6.1 Connection with ERP system
At present, large enterprises have begun to use the ERP system, which generally includes a warehouse management subsystem. The relatively simple warehouse management system is just a database management system for warehouse management, while advanced systems have begun to use bar codes to automatically enter data. Therefore, the introduction of a new system based on FRID technology requires a full understanding of the existing system, and the use of the existing foundation that can be used as much as possible to ensure the smooth implementation of the system.
It can be seen from the section system diagram that the characteristics of FRID warehouse management system are mainly reflected in the two parts of “field subsystem” and “execution subsystem”, while the “central subsystem” is not much different from the general warehouse management system.
6.2 Selection of electronic labels
Electronic tags suitable for warehouse management applications are mainly passive electronic tags in the UHF frequency band. This is because:
a) The reading and writing distance of UHF passive tags is long, generally 3-9 meters;
b) The price of the UHF passive tag chip is relatively cheap, and as the number of uses increases, its price will drop;
c) UHF passive tags are small in size, suitable for various forms.
6.3 Labeled cargo unit
The goods are stored in the warehouse in the following forms:
(1) Single product (Unit or Item): that is, each product is stored separately. Commodities stored separately in the warehouse are generally larger items;
(2) Case: multiple commodities are packed in one box and stored;
(3) Pallet: multiple boxes are stacked on a pallet and stored in the form of pallets;
We believe that the most suitable unit for labeling is in the box, and the number of items inside the box is recorded in the label pasted on the box. Labels should be affixed to large items by hanging; if there is no special need, no labels should be affixed to the pallet.
6.4 Storage location and cargo coding scheme
* Try to use mature coding schemes that have been used within the enterprise as much as possible;
* If there is no existing coding scheme, the international standard item coding scheme (EAN/UCC) shall be adopted.
6.5 Information stored on the label (format)
* Warehouse location labels are mainly stored: label category (location category), location number, stored goods code and quantity;
* The main storage on the label of the goods: label category (goods), goods code and quantity, storage time, batch, etc.
6.6 About AGV
The following issues should be considered in the selection of AGV vehicles for automatic storage:
(1) Try to use existing AGV vehicles, which is conducive to dispatch, use and maintenance.
(2) Facilitate the installation of automatic identification equipment on AGV vehicles;
(3) It is easy to automatically identify the equipment, and can control its speed, start, stop, and even reverse at will;
(4) Able to provide power (+24VDC) for automatic identification equipment;
The price is as low as possible, which is conducive to the popularization and application of the system.
[ad_2]