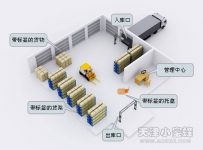
Little Bee RFID Warehouse Management System
[ad_1]
1. Introduction to the system
The goal of Little Bee’s RFID-based warehouse management solution is to change the traditional warehouse management method, seamlessly integrate RFID technology into your business, and realize efficient and information-based smart warehouse management.
In RFID warehouse management solutions, we will work to redefine the meaning of RFID applications and provide the most effective services in the simplest way. According to the characteristics of the industry, we provide multi-level products and services to meet the diverse needs of customers. We optimized the business processing, workflow and inventory control of warehouse management, resulting in improvements in productivity, accuracy, profitability and customer service.
The Tianjin Little Bee RFID warehouse management solution focuses on the most critical work links in your business, completes daily work efficiently and accurately, eliminates uncertainty, and enables our customers to save time, reduce inventory, and improve warehouse utilization Rate, increase productivity to improve warehouse efficiency.
2. Business demand analysis
There are many definitions of inventory and inventory management. Some people think that inventory refers to the reserve of all resources of an enterprise, and the inventory system refers to a whole set of systems and control methods used to control inventory levels, time and order quantities. Some people think that inventory can be regarded as temporarily idle resources used for future purposes, such as raw materials, semi-finished products, finished products, machinery, talents, and technology. From a financial point of view, inventory is money, an asset or capital in the form of materials. Inventory can also be regarded as the temporarily idle state of enterprise resources for future purposes. Some people think that the purpose of inventory management is to control the inventory level of the enterprise under the premise of satisfying customer service requirements, and strive to reduce the inventory level as much as possible and improve the efficiency of the logistics system to strengthen the competitiveness of the enterprise. Now, inventory is regarded as one of the four major driving factors of supply chain management. From the perspective of supply chain management, inventory cannot be viewed solely from benefits or from corresponding capabilities, but should integrate these two aspects to achieve an equilibrium point for inventory management.
Common problems existing in traditional warehouse management:
1. Without the use of barcode and RFID management methods, it is difficult for warehouse management to match the booked quantity with the physical quantity.
2. The warehouse management staff has a heavy workload, high work intensity, slow speed and low efficiency;
3. If manual data recording is used, the probability of error is high;
4. All kinds of warehouse operation data are recorded in various ledgers, which makes it inconvenient to query statistics;
5. Without accurate real-time data, the accuracy of procurement plan management is not predictable.
If there is no efficient warehouse management business processing (such as daily work such as outbound, warehousing, inventory counting, etc.), and no accurate and timely information processing, your business operations will cost a lot of manpower, material resources, and time, resulting in resource constraints in all aspects. waste.
Three, RFID technology is applied to the value analysis of warehouse management
The application of RFID warehouse management system can improve the efficiency of your business and save a lot of labor. At the same time, the waste and loss of goods have also been greatly reduced, thus making the business more competitive.
Now, the new focus is how to use data mining and analysis to turn the collected data into insights into the warehouse management business to promote further improvements in processes and benefits. Real-time update of inventory system information helps managers manage the supply chain more effectively.
RFID transmits not only radio frequency signals or data information, but also information about your business insights. Through these insights, you will have a new understanding of your business operations and discover real problems and business opportunities. In short, the function of modern warehouse management has also evolved from supporting business development to driving business, and then further promoting business development.
Little bee believes that the real value of RFID technology lies in obtaining a kind of insight into the business from long-distance contactless identification, positioning, and control, so that the results of this insight can be applied to the business.
Four, system design summary
The main advantage of RFID warehouse management system over other types of identification systems (barcode identification) lies in its non-contact data collection and radio frequency tag read/write operations. High recognition rate, strong adaptability, resistance to light, temperature, humidity, dust, grease, and chemical reagents are also the reasons why RFID warehouse management systems are particularly suitable for use in special environments in various industries.
RFID technical characteristics:
Suitable for harsh working environments such as dirty, grease, humidity, dust, chemical reagents, etc.;
The recognition speed is very fast, and the batch is unique. The information and data exchange between the reader and the tag is completed within a few milliseconds;
Non-contact remote automatic identification, reducing time, maintenance, and improving work efficiency;
Improve the process management of business operations, optimize the processing of raw materials, work processes and finished product inventory management;
Collecting information is more accurate, fast, and timely? Reduce time, save human resources, and improve productivity;
Bring improvements in productivity, accuracy, profitability and customer service, and increase customer satisfaction.
5. Functions and advantages
1. Warehousing function
Warehouse warehousing management checks and accepts the goods and handles them on the shelves. The warehouse receives orders and notices. The warehouse management system selects the warehouse according to the type of goods, and then allocates the warehouse area and storage location of the goods according to the selected warehouse. When the goods pass through the entrance, the fixed RFID reader reads the goods tags in batches, collects goods information, confirms the actual quantity of goods in the warehouse and checks it with the purchase notice. After the verification is completed, the goods are then distributed, moved or forklifted, and the goods are arranged on the shelves. The result of the storage is finally transmitted to the back-end database.
2. Outgoing function
The system sorts and manages the outbound goods according to the outbound order of the goods, finds out the outbound goods position, prints out the outbound order, and sends out the outbound order to the warehouse. On the manager’s handheld reader, the warehouse manager can accurately and quickly locate the location and quantity of the item. After finding the item, select the item, and finally out of the warehouse as a whole, and finally send the data to the management center to update the database.
3. Inventory function
Inventory count is to count and check the inventory of the current warehouse. It is mainly to check the actual inventory quantity and the book quantity, formulate an inventory plan, inventory list, generate an inventory table, and then arrive at the corresponding regional storage location range, and then inventory the data , Inventory can be remotely identified, fast, and multi-tag reading. The original one day’s work can now be completed in a short time. Finally, the system performs inventory processing and calculates the amount of spillage and loss of inventory in the warehouse.
4. Early warning function
Early warning function, including inventory warning and shelf life warning. When the inventory date or inventory volume of a single product is reduced to a set value, the system will automatically report a poor inventory warning, and provide regular reminders to remind warehouse managers to take corresponding measures. It can monitor inventory information in a timely manner.
5. Report statistics
The system can form statistical reports according to time, quantity and other elements, clarify the turnover period and efficiency, and facilitate the planning and control of the inventory management business process. The unified operation can speed up the speed of goods in and out of the warehouse, thereby increasing the throughput of the inventory center, and can provide Managers and decision makers provide timely and accurate inventory information, which can improve the accuracy of goods inquiries, reduce inventory levels, and improve the efficiency of the logistics system to strengthen the competitiveness of enterprises.
6. Real-time control of inventory information
Track pallets, cartons, cartons and individual products with RFID tags, and keep track of inventory status in real time. Improve inventory utilization and accuracy. Through the information in the data and the RFID tags, the staff can accurately locate the location where they need to go and sort the goods that need to be out of the warehouse in the first time. The reader/writer collects the corresponding information, and the database is updated in real time.
7. Reduce labor costs
In the entire RFID warehouse management operation, RFID remote identification, mass reading and accuracy are applied to the warehouse management process of outbound, inbound, inventory, and sorting, which has changed the traditional manual entry mode, greatly Improved efficiency and reduced labor costs.
8. Reduce TCO and increase ROI
Using the characteristics of RFID to change the traditional inventory management method, intelligently collected data is analyzed and processed to obtain intelligent insights and improve business lean. When the system is implemented, it is necessary to invest in RFID hardware, corresponding software and the services of related solution providers. The Littlebee RFID warehouse management system provides a multi-level and concise solution to reduce the customer’s total cost of ownership (TCO) and increase the return on investment (ROI).
[ad_2]