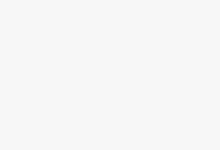
PDA terminal for tracking technology logistics
[ad_1]
Item tracking: logistics PDA terminal
Application area: Item tracking
Application product: Logistics PDA terminal
The PDA terminal for tracking technology logistics around the world consists of modules such as warehouse mobile operations, wireless inbound operations, outbound operations, shifting operations, and inventory operations.
Function 1: Receiving goods according to the order
Function 2: Sending for inspection, lending and picking
Function 3: Sending and returning products for inspection
Function 4: Select other products and lend out according to the order
Function 5: Return of selected products
Function 6: Picking out of the warehouse according to instructions
Function 7: Full library inventory
Function 8: Deliver according to instructions (small package)
Function 9: Warehousing by order (small package)
The network access module uses SIMCom (SIMCom Wireless) SIM900 to realize the wireless data transmission of logistics and distribution item information and management information, and provide a wide-area wireless IP connection.
Barcode production logistics system for manufacturing enterprises based on RFID and PDA wireless technology
1 Introduction
China has become the world’s manufacturing center. After the city has entered the “post-industrial” stage, the manufacturing industry’s dependence on logistics services has become more prominent. The logistics industry is also an emerging industry that realizes the integration of logistics operations and informatization. Its development level has become one of the important indicators for measuring the modernization and comprehensive competitiveness of a country and region. At present, most studies on manufacturing logistics are focused on external logistics such as external distribution and transportation, while research on internal logistics such as logistics in the production process and enterprise warehousing is relatively rare. The rationalization of internal logistics can promote the rationalization of resource allocation in the production process, and the rationalization of technological processes can greatly improve the competitiveness of manufacturing enterprises. The level of internal logistics determines the level of production efficiency and cost of an enterprise, and is the key to be tapped for the third source of profits for an enterprise.
2. Analysis of the status quo of the logistics system
Due to the accelerating process of global economic integration, enterprises are facing a more fierce competition environment, and the flow and allocation of resources on a global scale have been greatly enhanced. Countries around the world are paying more attention to the impact of logistics development on their own economic development, national quality of life, and military strength. , So that modern logistics presents a series of new development trends, but there are still some problems, especially the sharing and integration of information. Based on the analysis of the existing internal logistics system, the following shortcomings are summarized:
(1) The methods of information collection are backward. Most companies adopt manual collection methods, which are relatively inefficient. Even if the barcode technology is adopted, it is impossible to completely break away from the artificial function, so it is difficult to avoid some errors and the efficiency is extremely low.
(2) The information collected is limited. Generally, the collected information is some “static” information, such as existing inventory information, manufacturer information, specific sales information, etc.; for “dynamic” information, it is rarely involved, such as the production process, inventory changes, and sales process. , After-sales service, etc., so it is difficult to monitor in time.
(3) Information cannot be integrated and shared. The informatization construction of some enterprises has not realized the integration and sharing in the true sense, cannot realize the automatic transmission of business information and financial information, and cannot implement real-time control of the enterprise. Even more enterprises still rely on manual operation to a certain extent, and it is difficult to improve the efficiency of the enterprise, and it is impossible to fundamentally reduce the cost of the enterprise. In addition, because the integration of information cannot be achieved, some valuable information of the enterprise may not be applied, and the effectiveness of the information may be lost.
(4) The tracking of information cannot be achieved. Due to the lack of real-time monitoring of logistics information, real-time tracking of process information cannot be achieved, resulting in a lag in information release. Especially for the information in production, if there is a problem, it will often spend huge manpower and material resources in order to find the source of the error, which will affect the normal development of the enterprise and bring huge losses to the enterprise.
3. Application of RFID in logistics
RFID technology has incomparable advantages over other technologies. Combining it with the logistics management information system can create a high-speed operating supply chain, not only with a high degree of automation, but also with a high degree of transparency in the operation process, which is helpful for improving the core competitiveness of enterprises. Important role.
RFID has a wide range of applications in developed countries in Europe and America, and has shown a high degree of professionalism and popularization. It has the prospect of being widely used in logistics, material management, industrial automation and service industries. In addition to third-party logistics companies, more manufacturing companies use RFID in supply chain management, inventory management, distribution and other links involving product circulation. The RFID-based distribution center solution consists of multiple sets of radio frequency identification systems, middleware, database systems, and warehouse management information systems (WMS). in:
-Radio frequency identification system: mainly used to read/write information on electronic tags.
-Middleware: Between the front-end hardware module and the back-end database and application software, it provides mechanisms for program management, signal filtering and collection, event management, security management, and network management.
-Database system: input, analysis, output and management of various data information.
-Warehouse Management Information System (WMS): controls the actions of each link in the process, completes receipt and storage management, inventory allocation management, picking and delivery management, as well as data backup, data query, data statistics, report generation, and report management of the entire system .
The application of RFID in manufacturing enterprises will not only bring about the reduction of circulation and transaction costs and the improvement of management level, but also may bring revolutionary changes to the economy and even the entire social activities. However, the application of RFID in China is relatively small, and it is still in its infancy. There are mainly the following forms: First, in the enterprise, such as placing radio frequency tags on the trays of automated warehouses, it can significantly improve the degree of refinement of management; The second is to use in a supply chain, the use of radio frequency tags in the procurement process reduces management costs, improves product quality, and improves the inventory scheduling level; the third is to apply in a larger network, a typical case is the Ministry of Railways Vehicle management dispatch system.
4. RFID-based logistics system framework for manufacturing enterprises
Within the manufacturing enterprise, from the purchase of raw materials to the sale of the final product, detailed tracking, monitoring and management of information are required. However, the traditional logistics system of manufacturing enterprises often cannot achieve the above functions well. With its unique characteristics, RFID technology can bring unprecedented vitality to manufacturing enterprises after being widely used in logistics systems. The internal use of RFID in manufacturing companies mainly involves the procurement of raw materials, production and assembly, sales, and after-sales services. According to the production process of the product, the internal logistics of the enterprise is divided into supply chain logistics, production system logistics, distribution logistics and after-sales logistics.
4.1 Raw material procurement system
RFID is mainly used in the warehousing of goods in the procurement field.
When warehousing, by installing RFID tags on the goods or containers, and automatically identifying the data in the tags through the RFID-equipped data management program, you can know the status of the goods without opening the goods, and you don’t even need to stay. Directly complete the acceptance work and carry out warehousing management, which greatly improves work efficiency. When performing warehousing management, the reader will automatically identify the tag, record the record in the intermediate database, and transfer the data to the application system, modify the relevant data in the application system, complete the operation of material warehousing, and achieve logistics Consistency with information flow. During the warehousing process, the RFID data management program will select the location according to the volume, size and category of the goods. Then the warehousing information is passed to the cargo location management, and the goods are put into inventory. During the storage process, the goods will be counted regularly. Due to the use of RFID, the information in the inventory is more accurate and timely. As long as the RFID handheld reader device is used to collect the label information of the goods in the warehouse and check the data in the application system, the inventory of the goods can be completed.
RFID is widely used in procurement systems to realize dynamic management. It can speed up the storage and retrieval of goods, improve the accuracy of inventory counting, and efficiently complete various operations in the warehousing system; it can reduce inventory backlog and reduce operating costs.
4.2 Production assembly system
The main method for the production assembly system to use RFID technology is to design and write the data of the electronic label according to the production task order generated in the application system, such as the product’s material usage, completion station, finished product time, specifications and models, inspection results, operators, etc. For production process information and product information, readers are installed at key stations to read label information and guide the entire production process.
In the production assembly system, goods are picked and shipped out of the warehouse according to the production order generated by the application system. Send a picking instruction from the application system, and then leave the warehouse after picking is checked and accepted. When leaving the warehouse, the RFID data management program is used to automatically modify the relevant data in the application system according to the outgoing information to ensure the consistency of logistics and information flow. The electronic label designed according to the data in the application system is installed on the frame of the manufactured article and enters the process in the process. The process here generally refers to a process with molding or semi-molding, because in some refining processes, labels cannot be used. The reader/writer installed in the key process can read the label information, so that the process can be carried out in strict accordance with the instructions in the label and reduce the error rate. When the finished product is off the assembly line, the label can be recycled to reduce the cost of use. You can also keep it in the finished product, rewrite the data in it, and serve the next step of sales and after-sales.
After using RFID tags, staff update the production schedule, confirm whether the process is basically completed correctly, and confirm the supply of materials more effectively. Repeated use of RFID tags can save a lot of costs. And the characteristics of RFID itself, such as automatic acquisition of data, endurance of harsh environments and arbitrariness of attachment positions, enable enterprises to accurately obtain relevant data, and can transmit it to the application system for real-time online analysis and processing of the data, realizing automatic production Real-time tracking and effective monitoring.
4.3 Sales System
The use of RFID technology in the sales system is mainly the process by which items reach customers after being sold from the warehouse. In manufacturing enterprises, the process of outbound management is mainly involved.
The use of RFID technology in the sales system can save labor costs, reduce error rates, improve efficiency, timely improve inventory management, achieve timely replenishment, and effectively track transportation and inventory. At the same time, electronic tags can monitor some special items, such as items with an expiration date and items with special status. When the goods are sold, the RFID data management program can report the status of the goods in time, perform data analysis, and provide guidance to the application system; during the sales process, if the quantity of goods is below the lower limit of inventory, an alarm will be automatically given to notify the system in a timely manner Replenishment. At the same time, it monitors the goods equipped with RFID tags, dynamically adjusts their positions, and records them in the electronic tags.
4.4 After-sales service tracking
In the after-sales service tracking, RFID is mainly used in two aspects: after-sales service and maintenance system.
[ad_2]