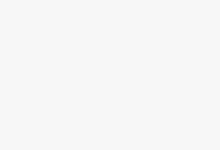
Power metering equipment management system based on RFID electronic tags
[ad_1]
1 Brief introduction of RFID technology
RFID (Radio Frequency Identification), that is, radio frequency identification. Also known as electronic tags. RFID technology is a non-contact automatic identification technology that has matured from the 1980s. Compared with traditional barcode recognition technology, it has many advantages: First, it can identify a single very specific object, rather than just like a barcode. Able to identify a class of objects: the second is the use of radio frequency, which can read data through external materials, and the barcode must be read by laser; the third is that multiple objects can be read at the same time, and the barcode can only be read one by one. Reading III; In addition, it also has the characteristics of waterproof, anti-magnetic, high temperature resistance, long reading distance and repeatable reading and writing of label data that are not available in ordinary barcodes.
The most basic RFID system consists of three parts: Tag. Composed of coupling elements and chips, each tag has a unique electronic code, which is attached to the object to identify the target object; Reader, a device that reads (and sometimes writes) tag information, can be designed as a handheld Or fixed type; Antenna, which transmits radio frequency signals between tags and readers.
The working principle of the RFID system: As shown in Figure 1 below, after the tag enters the magnetic field, it receives the radio frequency signal from the reader. Rely on the energy obtained by the induced current to send out product information stored in the chip (Passive Tag, passive tag or passive tag), or actively send a signal of a certain frequency (Active Tag, active tag or active tag); read and write After the information is read and decoded by the device, it is sent to the central information system for relevant data processing.
620)this.style.width=620;” border=0>
Chart 1 RFID structure diagram
Ø The reader/writer sends a certain frequency radio frequency signal through the transmitting antenna. When the radio frequency card enters the working area of the transmitting antenna, an induced current is generated, and the radio frequency card gains energy and is activated.
Ø The radio frequency card transmits its own encoding and other information through the antenna in the card.
Ø The reader-writer receiving antenna receives the carrier signal sent from the radio frequency card, and transmits it to the reader-writer via the antenna adjuster. The reader-writer demodulates and decodes the received signal and then sends it to the background software system for processing.
Ø The background software system judges the legitimacy of the card based on logical operations, makes corresponding processing and control for different settings, and sends out instruction signals to control the execution of corresponding actions.
1.1 Advantages of RFID electronic tags compared to barcode labels
Barcode technology has been around for many years, and it plays a vital role in the management of the asset life cycle, improving work efficiency to a certain extent. Because of its low price, it is well received by all walks of life and is widely used. However, compared with RFID electronic tags, barcode labels also have many weaknesses.
1) The bar code label can only be read once at a time, while the RFID electronic label has the function of rereading, which can identify multiple tags at a time, which can realize rapid exchange identification in large quantities and improve production efficiency. For example, group identification can be realized at the entry and exit of power measuring instruments.
2) Barcode tags are easily contaminated and have a short lifespan, while RFID tags are resistant to abrasion and contamination, and their lifespan can reach 15 years.
3) Barcode tags must be identified from the front, while RFID tags have a weak sense of direction and can be identified on any side. For example: during the power inspection, the power facilities in the equipment cabinet can be identified.
4) The barcode scanning recognition distance is limited, while the RFID recognition distance is between 5-8M. For example: during power patrols, identify high-altitude power devices, while staying away from high voltages to increase personal safety.
5) The bar code label can be read directly and can be copied, while the content of the RFID label cannot be changed or copied, and has a certain anti-counterfeiting and anti-theft function.
6) The application of RFID technology can further informatize and digitize the entire asset management, thereby bringing management to a higher level.
1.2 Overview of power meter management
The power system companies in the provinces and municipalities directly under the Central Government have their own unique management methods in terms of power measurement instruments. For a certain electric energy metering center, the principle of “local bureau demand → centralized procurement → centralized verification → unified distribution” is adopted. In order to achieve the management of the entire life cycle of the appliance, each appliance is set with more than 30 states such as “waiting arrival → arrival → stock pending inspection → work area pending inspection →…… → scrap verification → scrap”. These states are All changes require specific operations, that is, to perform at least one recognition operation on each appliance. At present, there are about 500,000 equipment verification work every year. For such a digital equipment, its storage and exit and customs handover are necessary. As you can imagine, the workload is huge. If you need to manually enter or use barcode scanning, it is not practical. This requires us to find a way to quickly and accurately identify batch equipment, which is radio frequency identification.
According to the specific needs of the power and energy metering center, we designed a complete set of RFID application solutions-based on UHF electronic tag power metering equipment system. The system realizes the group identification of measurement tools, makes it easy to identify and confirm the transfer of each joint of warehouse, verification, distribution, etc., which greatly improves the production efficiency of the electric power center, and at the same time, realizes a higher level of electric energy measurement instruments. The management of the whole life cycle has raised the level of power asset management to a new level, which is well received by users.
620)this.style.width=620;” border=0>
Chart 2
2 The composition of the system
2.1 Introduction to user workflow
For a certain electric energy metering center, the operation flow of the management of metering equipment is shown in Figure 2:
620)this.style.width=620;” border=0>
Chart 3 RFID planning operation process
It can be seen from the figure that the self-purchasing and warehousing of electricity metering and delivery to users are basically completed between the warehouse and the verification room. For this kind of work process, it is necessary to automatically collect the data of the equipment by RFID at the key points. To this end, we have carried out RFID design planning for its existing process, as shown in Figure 3 RFID planning operation process:
620)this.style.width=620;” border=0>
Chart 4 Operation Process after RFID Planning
2.1.1 RFID overall design
The overall design of RFID is as shown in Figure 4
620)this.style.width=620;” border=0>
Chart 5
The RFID system can basically be divided into two subsystems
2.1.1.1 Batch production of RFID electronic tags
Electronic tags are divided into two types according to the power supply mode: active and passive. Passive tags have no power source, and the current generated by induction electrification is used to supply power to the tags. The operating distance is relatively short, but the battery does not need to be replaced, which is particularly suitable for power system applications, and is also the mainstream direction of current market applications.
Electronic tags are classified according to frequency: low frequency (125K), high frequency (13.56M), and ultra high frequency (915M-48G). For this project, we use ultra high frequency, passive electronic tags. Through a large number of experiments, this type of electronic tag is suitable for sticking on power equipment for a long time, with a long reading distance (5-8M), and the group reading effect is better than other frequency bands. It can fully meet the requirements of this project.
Due to the process requirements of the metrology center to ensure the directness of the individual identification of the inspection station and the bar code, we design the bar code label and the electronic label to coexist at the same time to mark the equipment. An electronic label with bar code at the same time.
Before the electronic tag is officially used, there must be a read-write device to initialize it-assign an ID number. Small batches of irregular electronic labels can be assigned by the reader, and large batches of electronic labels can be written one by one using an RFID printer. According to the requirements of this system, we use RFID printers for ID number assignment. The electronic label defined by I am printed with an ID number in advance through the card issuer. The ID number is generated by the background (MIS) according to the user’s requirements, and it is unique. RFID printers, one is to write the electronic label ID, and the other is to print the barcode electronic label, and paste it inside the power metering equipment for group identification.
620)this.style.width=620;” border=0>
Chart 6
620)this.style.width=620;” border=0>
Chart 7
Ø Group identification system with RFID tag equipment
The fixed reader is fixedly installed at the demarcation point of supply and demand to complete group reading, input, identification, and confirmation functions. The number of readings is required to be accurate, without missing reading, and the more group readings, the better. We customize four sets of fixed readers, which are installed at the demarcation point of warehouse A and the outside; B demarcation point of three-phase watt-hour meter inspection room and the outside; C demarcation point of single-phase watt-hour meter inspection room and the outside world; D transformer inspection room The point of demarcation with the outside world. Each demarcation point reader is equipped with four antennas, which can read the tags on the equipment in a group, and interface with MIS to realize the group entry function. The hardware interface is LAN and serial port optional.
A number of electrical equipment with electronic tags are identified by a fixed reader group when entering and exiting the warehouse, entering and exiting the verification room, and the identified ID number enters the database to complete the data collection.
Group identification equipment installed at each joint: 1) Identification door
620)this.style.width=620;” border=0>
Chart 8
2.2 System function indicators and characteristics
1. Batch printing of finished electronic labels, production capacity: 20,000-40,000 pcs/day.
2. Using the form of radio frequency gate, 128 electronic tags (at a speed of ≤0.5M/S) are all read out through the identification area, and the correct rate of data reading and writing reaches 100%.
3. Using the form of identification room, 128 electronic tags can be read out in the indoor identification area, and the correct rate of data reading and writing reaches 100%.
4. Establish an RFID middleware system (MIS interface) based on UHF electronic tags.
620)this.style.width=620;” border=0>
Chart 9
[ad_2]