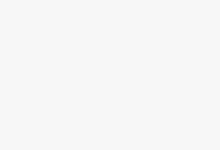
RFID application solution for hanger management of Shijia electroplating production line
[ad_1]
1. Introduction
Workers on the electroplating production line must manually set the working parameters of the equipment used in the electroplating process by observing the types of hangers and parts and other information to ensure that the process parameters of the parts to be processed are accurate. Manual settings will not only affect the production The production efficiency of the line is extremely easy to make mistakes; the life span of the hanger used in the electroplating process is limited, and it may need to be repaired many times during the entire use process. After the accumulation reaches a certain level, the hanger needs to be scrapped, otherwise it will cause Defects in electroplating process of parts.
Due to the large amount of dust, high temperature and humidity, corrosion, and poor visibility in the electroplating production environment, automatic barcode recognition technology cannot be applied.RFIDCompared with the barcode technology, the technology has many advantages, such as long recognition distance, no need for visual visibility of tags during recognition, use in harsh environments, update content, ability to read multiple tags in batches, and recognition of high-speed motion Items and information are large, not easy to imitate, etc. Therefore, the use of UHF RFID technology to realize the data collection of the key processes of the electroplating production line, and the efficient cooperation with the automatic conveying system, overcomes the existing problems in the current system, and improves the reliability and accuracy of the data collection of the electroplating production line. Improve production efficiency and reduce product failure rate.
Second, the key process
1. Label initialization and hanger labeling: each component can only be hung on one kind of hanger (the hanger has a one-to-one relationship with the part type), and the unique code of the hanger and the hanged parts The information is written into the temperature-resistant and corrosion-resistant metal-resistant electronic tag, and then the RFID tag is fixed to the upper edge of the hanger by screws or rivets for identification;
2. Tag identification of hanger: When workers hang parts, the RFID reader will automatically identify all hangers that enter the spraying process, count the times of use of the hangers and prompt maintenance, scrapping and other information, and will identify the parts at the same time The types and process information are passed to the relevant process equipment to ensure correct operation.
Three, equipment configuration
1. Reading and writing equipment: According to the requirements of the on-site environment, equipped with our company’s high-protection, integrated, high-performance industrial-grade integrated reader;

Physical environment indicators
Working temperature: -20℃~75℃
Storage temperature: -40℃~85℃
Working humidity: 5%~95% non-condensing
Power supply: 88~264VAC/47~63Hz(<1A)
Size/weight: 278*177*91mm/ about 2.5kg
Shell material: metal (die-cast aluminum alloy)
Protection level: IP65
Main performance index
Air interface protocol: EPC Global Class1 Gen2/ISO 18000-6C
Frequency characteristics: National standard: 920.625MHz~924.375MHz, channel spacing 250kHz
American standard: 902.75MHz~927.25MHz, channel spacing 500kHz
Frequency mode: fixed frequency/frequency hopping, 10 frequency hopping points
Output power: 16~31dBm, step interval 1dB
Reading label distance: Reading label distance> 10 meters, writing label is about 50% of reading label distance
Antenna port: 2 SMA/N radio frequency connection cables (can be expanded to 4 as required)
Communication interface: RS232 (built-in), 10/100M Ethernet or WIFI
Working mode: interval T cycle/continuous work
Input/output port: none
2. Electronic tag: special temperature-resistant, corrosion-resistant and metal-resistant electronic tag ST-E600.

ST-E600 UHF anti-metal tag
Applicable fields: logistics and warehousing, postal industry, automobile industry and retail, etc.
RF parameters: EPC Class 1 Gen2 (860-940 MHz, EPC 96 bits, User512 bits)
Material compatibility: For metal or plastic substrates.
Reading range: fixed reader 6m; mobile reader 3m
Appearance size: 80*15*12mm (with hole); 60*15*12mm (without hole)
Weight: 12.5g (with holes); 11.5g (without holes)
Packaging material: ABS plastic hard shell
Working temperature: -40℃ — +85℃
*Long-term exposure can withstand the highest temperature +85℃
*Short-term exposure can withstand the highest temperature +105℃
Water resistance: IP 68
Seismic and compression resistance: MIL STD 810-F
Impact resistance: 10kg from 1m
Installation method: Use rivet mechanical assembly or adhesive paste.
Certification: RoHS, CE.
3. Card issuing equipment
You can use our SR-3200B card issuing machine or SR-6601 handheld machine.

Main performance indicators of SR-6601 handheld
Processor: Samsung S3C2440A, clocked at 400MHz
Operating system: WinCE 5.0/Android
Memory: 64M SDRAM/128M FLASH
Display: 3.2 inches TFT 240*320 resolution with handwriting touch screen
Barcode scanning: optional one-dimensional laser barcode/two-dimensional barcode
RFID: optional LF/HF/UHF RFID
Communication interface: USB2.0, UART
Wireless transmission: standard WiFi/BlueTooth 2.0, optional GPRS/WCDMA
Positioning: GPS optional
Multimedia: video playback, camera, video, 3.2 inch touch screen, 16G large capacity TF card expansion, etc.;
Environmental specifications
Specification size: length 170cm, width 70cm, height 35cm, weighs about 220 grams
Protection level: IP54
Working environment: use 0℃-50℃, storage -20℃-70℃
Working time: 3400mA polymer battery, 3mAH standby current, longer standby and working time

SR-3200B
Working temperature: -10℃~55℃
Storage temperature: -20℃~75℃
Working humidity: 5%~95% non-condensing
Working power supply: DC: +5V/500mA (standard USB power supply, optional adapter power supply)
Current consumption: operating mode: maximum 400mA, average less than 200mA
Parameter configuration mode (standby): less than 130mA
Dimensions: length * width * height: 168*108*40mm
Shell material: plastic
Weight: about 0.4kg
Air interface protocol: EPC Global Class1 Gen2/ISO 18000-6C
Tag data rate: 40~640 kbps
Modulation method: ASK/PR-ASK
Frequency hopping frequency point: maximum 10 frequency hopping frequency points can be selected under the condition of meeting the national standard or the American standard
Channel bandwidth <250kHz
Frequency range: National standard: 920.625MHz~924.375MHz
American Standard: 902.75MHz~927.25MHz
Radio specification: CHN/FCC
Frequency mode: fixed frequency/frequency hopping optional, maximum 10 frequency hopping points
Output power (erp): control range 7~22±1dBm, maximum 22dBm, minimum step size 1dB
Reading label distance: Read label distance> 1 meter (related to label); writing label distance is about 30% of reading label distance
Antenna port: No external antenna port, built-in 1dBi ceramic antenna
Communication interface: USB virtual serial port (default)/RS232, choose one
Working mode: interval T cycle/continuous work
LED indicator lights: 2 indicator lights (power indicator and communication indicator)
4. Implementation benefits
1. Automatically collect information about hangers and parts in the electroplating process, which provides an information basis for equipment related to the electroplating process;
2. Information technology combines sensor technology, automation technology and RFID technology to realize the automation of the whole process of the electroplating production line and realize the real integration of the two;
3. Realize the whole life cycle management of the hanger, and reduce the unqualified rate of the product;
4. Improve the production efficiency of the enterprise, reduce the labor intensity, and reduce the mistakes in the selection of manual process parameters;
5. Improved the enterprise’s information management level.
[ad_2]