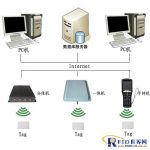
RFID-based intelligent warehouse management solution
[ad_1]
1. System Overview
1.1. System background
Global business competition in the 21st century is not only a single competition in the fields of technology, cost, and management, but also a comprehensive competition between the advantages and disadvantages of the global supply chain. Improving production efficiency and reducing operating costs are vital to companies. They quickly recognize the problems in warehouse management, and improve, design and establish a complete warehouse management process to improve warehouse turnover and reduce The occupation of operating funds turns frozen assets into cash, reducing the cost caused by the elimination of warehousing. The multinational commercial retail giants have invested heavily in their supply chain strategy, planning, operation management, distribution center planning, warehouse planning, etc., using today’s most advanced science and technology to establish a fast and efficient operating system.
RFID technology is used to manage the entry and exit of goods in warehousing and logistics, to identify pallets, simplify the operation process, improve work efficiency, and reduce the labor intensity of workers.
1.2. Status Quo and Analysis
Existing warehouse logistics management systems usually use barcode labels or manual writing of warehouse logistics management documents to support existing warehouse management. However, the shortcomings of barcodes such as easy copying and non-moisture resistance, as well as the cumbersomeness of manual writing of receipts, can easily cause human losses and other unavoidable things. The efficiency of warehouse management based on manual operations is very low, and it is time-consuming and labor-intensive in cargo classification, cargo search, and warehouse inventory inventory, which makes the current warehouse management always suffer from defects.
RFID technology is used for intelligent warehouse logistics management. First, electronic tags are affixed to each goods, and the information of the readers in each channel of the channel warehouse is used to determine the goods in, out, allocation, shifting, inventory counting, etc. Process, automatic data collection through RFID reader data, to ensure the speed and accuracy of data input in each link of warehouse management, to ensure that enterprises can accurately grasp the real data of inventory in a timely and accurate manner, and to achieve efficient cargo search and real-time inventory counting. It is helpful to improve the efficiency of warehouse management, get rid of the time-consuming and laborious traditional warehouse management, reasonably maintain and control enterprise inventory, and enable the enterprise to operate efficiently. Through scientific coding, it is also convenient to manage the batch and shelf life of items. Using the system’s location management function, you can even query the current location of all inventory materials.
2. System Introduction
2.1. System Principle
The warehouse management system design adopts the following three-tier structure:
Information collection layer
The new goods are equipped with RFID tags through card issuance and labeling. The unique ID number of the tag or the code written by the user can identify the goods. The reader can automatically collect tag information, so as to realize the information collection function of the goods.
Data transfer layer
The cargo label information collected by the RFID reader can be transmitted to the back-end system for analysis through the relevant communication interface. The communication interface of the transmission can be selected according to user needs, such as RS-485, RS-232, Ethernet, WIFI Or GPRS, etc.
Cargo management
After the PC terminal or the back-end data center receives the data from the reader, it analyzes the data to determine the flow of goods out of the warehouse, warehousing, shifting, and inventory, and at the same time generates a corresponding report indicating the detailed list, and makes the corresponding in the system的处理。 Treatment.
2.2. System structure
Figure 1: System hardware structure
The hardware of the RFID warehouse management system is mainly composed of RFID tags, fixed readers, handheld readers, servers, personal computers, etc., and realizes mutual connection and data exchange through the network.
The RFID warehouse management system software is composed of a supply chain management system, an RFID tag issuing system and an RFID tag identification collection system. These systems are connected to each other to jointly complete the various processes of item management. The back-end database management system is the core of the entire system, and RFID identification collection is the basis and means to realize the management function.
2.2.1. Supply Chain Management System
The supply chain management system is composed of a database server and a management terminal. It is the data center of the system. It is responsible for data communication with the reader. The data uploaded by the reader is converted and inserted into the database of the supply chain warehouse management system. Label management Information, issuance labels and collected label information are stored and processed in a centralized manner.
2.2.2. RFID Tag Issuing System
The RFID label issuance system is composed of a card issuer and label information management software, and is responsible for completing the information writing of location labels, item labels, and box labels, as well as the change, authorization and encryption of label ID numbers. The label information management software is embedded in the back-end system to achieve one-to-one correspondence with the supply chain system.
2.2.3. RFID tag collection system
The RFID tag collection system is composed of readers, handhelds, and tags. The readers and handhelds automatically identify the tag information on the items, and after the information is sent, the back-end system analyzes and sorts them out, so as to determine whether the items are in or out of the warehouse. , Allocation and maintenance procedures, etc.
2.3. System Function Module
Figure 3: System function modules
The RFID warehousing logistics management system consists of card issuance and labeling, outbound management, inbound management, allocation and shifting, inventory counting and additional functions. The outbound management system includes outbound goods claim, outbound goods identification, and outbound record download. The warehousing management system includes location allocation setting, unloading product identification, and warehousing record management.
2.4. Work flow
2.4.1. Issuance and labeling
Label the newly purchased goods and equip them with electronic labels. The unique ID number of the label or the data written by the user can be used as the identification code of the goods, and the data is used to record the name of the goods, the time of purchase, the warehouse to which they belong, and the attributes of the goods. When the readers installed in each channel recognize the tags, they can automatically obtain all the information of the goods.
2.4.2. Warehousing
First, arrange the storage location on the system for the goods that need to be stored, such as which category the goods belong to, which warehouse and which shelf they need to be placed in; secondly, put all the tagged items into the storage area and transport them in from the inbound channel. In the warehouse; when passing through the channel, the RFID reader will automatically identify the tag information. If the tag information and quantity recognized by the reader are correct, it will be put into the warehouse. If the tag information recognized by the reader is wrong or the quantity is small, the system will prompt ; When entering the warehouse, the operator can accurately store the goods in the corresponding warehouse area according to the label information and system prompts. At the same time, the system will automatically follow the item information (date, material, category, quantity, etc.), and form the warehousing list details.
Figure 4: Schematic diagram of warehousing
2.4.3. Delivery
1) To apply for outbound goods, fill in an application form for outbound goods on a personal computer.
2) After receiving the outbound order, the warehouse manager finds out the corresponding items through the handset or querying the server, and places the goods in the outbound area.
3) The goods to be out of the warehouse with electronic tags are recognized by the reader through the access channel before loading.
4) The outbound channel reader will check the identified electronic tag information with the outbound application form to confirm whether the loaded goods are consistent. If they are inconsistent, repeat the identification or supplement the out of stock.
5) The system automatically updates the item information (date, material, category, quantity, etc.), and forms the details of the outbound order.
Figure 5: Outgoing flow chart
2.4.4. Allocate and move library
The goods to be transferred to the warehouse will be recognized by the reader installed next to the passage when they pass through the passageway. The reader/writer records the current tag information and sends it to the back-end center. The back-end center judges whether it is warehousing, outgoing, or transfer based on the sequence of the entry and exit channel identification tags.
You can also use the handheld to move the goods. When the warehouse manager finds that a certain item is misplaced, he can manually place the goods, and at the same time change the label information through the handheld and send it to the server, realizing quick and convenient shifting Features.
Figure 6: Schematic diagram of goods allocation and transfer warehouse
2.4.5. Inventory Check
Account check
The information in the RFID tag of the cargo location is obtained through the handheld, and the information is checked with the information in the warehouse management system. The manager only needs to take the handheld to walk through the cargo locations to complete the inventory.
Account verification
By checking the label information of specific goods with the storage information points in the warehouse management system, the specific operations are as follows:
The host forms an inventory operation instruction, and the operator carries out the area to be inventory according to the instruction by holding the activated handheld device, and performs inventory in units of each cargo location. Use the handheld machine to scan the electronic labels on all the packages of the goods on the cargo space one by one. After scanning all the goods on the shelf, confirm and get the label inventory information. The operation log containing the information will be sent back to the host through the wireless LAN, and the host will The inventory information is compared with the information in the shelf label and the original inventory information, and the resulting difference information is further processed.
Figure 7: Inventory flow chart
2.4.6. Additional functions
Inventory warning
When the inventory of the warehouse is less than the normal inventory, the system will prompt to replenish the inventory to avoid the phenomenon of insufficient inventory.
If the goods are moved or taken out of the warehouse without permission, an alarm will be issued, etc.
When the goods are moved abnormally or taken out without permission, the reader will alarm the system at the same time as the reader recognizes it to prevent the goods from being lost or stolen.
3. Schematic diagram of reader installation
Figure 8: Schematic diagram of reader installation
Install RFID readers at the gates of import and export to facilitate the identification of goods in and out of the warehouse. Separate readers and display screens are installed at the door of each warehouse in the room to detect the details of the products in the warehouse.
4. System Features
4.1. Realize first-in first-out management of goods
The RFID warehouse management system uses advanced RFID technology, wireless local area network, database and other advanced technologies to combine the entire warehouse management with radio frequency identification technology, which can efficiently complete various business operations, improve warehouse management, and increase efficiency and value. For each batch of goods in the warehouse, the storage time, storage location and other information are automatically recorded by the system. When the goods are out of the warehouse, the first-in first-out management of the goods can be realized on this basis.
4.2. Real-time management of warehouse inventory
The inventory management of the original warehouse relied on manual reports and manual statistics, which led to the inability of various departments to understand inventory information in a timely and accurate manner. In addition, with the development of business, the number and variety of daily incoming and outgoing goods gradually expand, and customer needs are becoming increasingly complex. Whether the warehouse inventory can be managed in real time has become an important factor affecting the establishment of a fast and efficient operating system. The RFID warehouse management system can accurately grasp the inventory situation of the warehouse in real time, and provide a scientific basis for leaders at all levels and related departments to optimize inventory and make production and operation decisions.
4.3. Material tracking and graphical management
On the basis of realizing cargo pallet position management, the system can also realize the functions of material tracking and graphical management. This function allows the stock materials to be reflected in a graphical manner very intuitively and quickly. Greatly improve the storage efficiency and precision of item management. Improve the recognition rate of items in and out of the warehouse, without opening the box for inspection, and identify multiple items at the same time, improving the efficiency of in and out of the warehouse.
4.4. Reduce inventory cycle and reduce distribution costs
The traditional warehouse inventory is time-consuming and laborious. The RFID warehouse management system reduces the warehouse inventory cycle, improves the real-time data, and dynamically grasps the inventory status in real-time to realize the visual management of inventory items. Improve the efficiency and accuracy of the picking and distribution process, accelerate the speed of distribution, and liberate the labor force.
5. Other application areas
1) Management of military supplies for the army
2) Tobacco logistics warehouse management
3) Inventory management of medical drugs
4) Inventory distribution management in the retail industry
5) Warehouse management of materials and finished products for large enterprises
6) Classification and distribution management of airport consignments
7) Related types of applications such as port and terminal container cargo management
6. Hardware equipment selection
[ad_2]