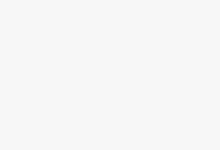
RFID intelligent warehouse logistics management system
[ad_1]
system introduction
RFID warehousing management system is a platform based on RFID identification technology for cargo identification, tracking, management and inspection of cargo information. The tracking mainly includes functional modules such as distribution demand, cargo delivery, cargo warehousing and delivery overtime. It is developed by Shenzhen Aisai Developed by Ke Technology Co., Ltd., this system combines advanced RFID identification technology and computer database management query to automatically identify cargo information, realize the needs of automation, informatization, and intelligence of enterprise logistics operations, and realize RFID technology and enterprise information at the same time The seamless docking of the chemical system ensures that RFID technology can maximize the benefits of enterprise logistics operations.
Radio Frequency IDentification is RFID (Radio Frequency IDentification) technology, also known as electronic tags and radio frequency identification. It is a communication technology that can identify specific targets and read and write related data through radio signals without the need to establish a mechanism between the identification system and specific targets. Or optical contact.
technical background
The development of economic globalization and the rise of the Internet have accelerated the development of the global logistics service industry. The development of global economic integration has made the cooperative relationship of purchasing, warehousing, sales, and distribution of enterprises increasingly complex. The competition between enterprises is not only the competition of product performance and quality, but also the competition of logistics capabilities. Use information technology to replace actual operations, reduce waste, save time and expense, so as to achieve seamless docking and integration of the supply chain. In order to realize the information management of logistics processes, use information management methods to manage the company’s warehousing and logistics information. , In order to promote data sharing, goods and capital turnover rate, improve work efficiency, and achieve an informatization process synchronized with modern logistics enterprise management.
solution
1) Automatic sending of requirements: the production line automatically collects empty containers, and automatically sends and distributes requirements through collection and scanning;
2) Distribution of physical objects: logistics companies deliver goods on time and in quantity according to distribution requirements;
3) Factory physical storage: automatic identification of goods storage, automatic matching of distribution requirements, and improvement of the efficiency of goods storage;
4) Distribution abnormality alarm: during the distribution process, when the system detects the distribution overtime and abnormal distribution, the system will automatically alarm and remind;
5) Collection technology principle: After the goods container enters the collection area, the collection equipment automatically recognizes multiple goods through the collection of RFID tags, thereby efficiently completing the goods in and out of the warehouse, ensuring that the physical goods are consistent with the delivery requirements, and improving the efficiency of goods delivery;
6) Implementation benefits: When the goods are in and out of the warehouse, the equipment can automatically and quickly identify the goods, and at the same time, automatically match the delivery requirements to improve the efficiency of goods in and out of the warehouse;
7) Real-time: Real-time control of the distribution of all goods, accurate control of inventory, optimization of reasonable inventory, and real-time control of warehouse environment status and changes;
8) Scalability: Realize cross-regional centralized management, distributed operation and real-time monitoring functions, efficiently complete various business operations, improve warehouse management, and increase efficiency and value.
System composition
This system is a high-tech product integrating radio frequency automatic identification technology, Webservice communication technology, computing control technology, and network technology. The system network topology is shown in the figure below.

System functions
The RFID warehousing logistics management system performs intelligent and informatized management of enterprise logistics goods, and realizes the functions of automatically sending distribution demand information, real-time tracking of goods delivery, automatic recording of goods warehousing information, automatic system alarm, and real-time docking with WMS system. The system flow chart is shown in the figure below.

Performance characteristics
1) Relying on the advantages of RFID technology, the system has the ability to realize long-distance collection of goods information
2) The system uses the technical advantages of RFID to collect real-time information in each operation link to ensure that the company can accurately grasp the inventory status in a timely and accurate manner;
3) Through the collection of goods data by the warehouse reader, the system can realize the management of anti-crossing goods;
4) When the delivery exceeds the required time, the system will automatically alarm to prevent the production line from stopping;
5) The system software platform adopts an open platform architecture, which can be well connected with enterprise ERP, SAP and WMS systems.
Applicable field
With the gradual maturity of RFID technology, its application becomes more and more extensive. The combination of RFID front-end equipment (tags, card readers) and enterprise core systems can be widely used in the supply chain and warehousing and logistics management fields, effectively solving the input/output of various business operation data in the supply chain, and the control of business processes. Tracking, and reducing the error rate and other problems.
1) Retail link
RFID can improve the inventory management of retailers, realize timely replenishment, effectively track transportation and inventory, improve efficiency, and reduce errors. At the same time, smart tags can monitor the expiration date of some time-sensitive commodities; stores can also use the RFID system to automatically scan and charge at the checkout counter to replace manual collection. RFID tags in the sales link of the supply chain terminal, especially in the supermarket, avoid manual intervention in the tracking process, and can generate 100% accurate business data, so it has a huge appeal.
2) Storage link
In warehouses, the most widely used radio frequency technology is to deposit and withdraw goods and inventory. It can be used to automate operations such as inventory and retrieval. In the entire warehouse management, combining the receiving plan, picking plan, and shipping plan made by the supply chain planning system with radio frequency identification technology can efficiently complete various business operations, such as designating storage areas, picking up on shelves, and Replenishment etc. In this way, the accuracy and speed of operations are enhanced, service quality is improved, costs are reduced, labor and inventory space are saved, and at the same time, the misplacement, misdelivery, theft, damage and inventory and shipment of goods in the entire logistics are reduced. Loss caused by errors, etc. Another benefit of RFID technology is to reduce manpower during inventory counting. The design of RFID is to automate the registration of goods. It does not require manual inspection or scanning bar codes during inventory, which is faster and more accurate, and reduces losses. RFID solutions can provide accurate information about inventory conditions, and managers can quickly identify and correct inefficient operations, thereby achieving fast delivery and minimizing storage costs.
3) Transport link
In transportation management, RFID tags are affixed to goods and vehicles transported in transit, and RFID receiving and forwarding devices are installed at some checkpoints on the transportation line. After receiving the RFID tag information, the receiving device uploads it to the communication satellite along with the location information of the receiving place, and then transmits it to the transportation dispatching center by the satellite, and sends it to the database.
4) Delivery/distribution link
In the distribution link, the use of radio frequency identification technology can greatly accelerate the speed of distribution and improve the efficiency and accuracy of the picking and distribution process, and can reduce labor and reduce distribution costs. If all commodities arriving at the central distribution center are affixed with RFID tags, when entering the central distribution center, the pallet passes through a reader to read the contents of the tags on all the boxes on the pallet. The system checks this information with the shipping record to detect possible errors, and then updates the RFID tag to the latest product storage location and status. This ensures precise inventory control, and even knows exactly how many containers are currently in transit, the origin and destination of the transshipment, and the expected arrival time.
5) Production link
The application of RFID technology in the manufacturing process can complete the operation of automated production lines, realize the identification and tracking of raw materials, parts, semi-finished products and finished products on the entire production line, reduce manual identification costs and error rates, and improve efficiency and benefits. Especially in the assembly line that adopts JIT (Just-in-Time) production method, raw materials and parts must be delivered to the work station on time. After the use of RFID technology, it is possible to quickly and accurately find the raw materials and parts required by the workstation from a wide range of inventory by identifying electronic tags. RFID technology can also help managers send out replenishment information in time according to the production schedule, achieve a balanced and stable production line, and also strengthen quality control and tracking.
success case
Konica Minolta
[ad_2]