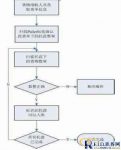
RFID intelligent warehouse management system
[ad_1]
1. Overview of system requirements analysis
As the core business system of a company, the warehouse management system (WMS) uses computer software to simulate the system process of warehouse management. Its comprehensive requirements must be concise and practical, and improve the quality and efficiency of warehouse management.
The centralized placement of materials in a certain place needs to be managed by scientific methods, and efficient and accurate warehousing operations are realized. Under the premise of ensuring basic efficiency, timely cargo update information is submitted to the server database; the upper management system must ensure During the storage period, the quantity of the goods will not change, and the corresponding entry and exit records and regular inventory information will be maintained.
In the storage of goods, the use of space must be maximized, and labor and equipment must be used to the greatest extent and most effectively. The goods can be easily accessed and quickly located when needed. On the other hand, this management system needs to implement an efficient and accurate inspection and verification mechanism for incoming and outgoing goods, so that a larger number of incoming and outgoing operations can be completed within a limited working time on an error-free basis, saving human resources to the greatest extent Consumption, to avoid the occurrence of errors caused by human factors. In addition, the RFID intelligent warehouse management system must also ensure that it can efficiently complete the statistics of the types and quantities of goods, manage the maximum use of storage space and ensure the premise of ensuring the correct quantity of materials. Therefore, an efficient inventory function is indispensable.
2. Drawback analysis and problem improvement of traditional warehousing business process
1. Traditional business analysis
When warehousing, the warehouse management staff receives the warehousing operation instruction, and according to the conditions of the warehousing items, selects the warehouse and arranges the storage area for the items. Warehousing personnel check the inventory with the inventory and physical objects according to the inventory of the warehousing operations, and check and accept the warehousing items. Use barcode scanning method to count and check the total quantity of goods arrived, unit packaging, etc. After the acceptance is completed, the warehouse operator will store the goods in the designated area according to the location arrangement plan, and the warehouse management personnel will complete the corresponding information recording work and input it into the computer. When leaving the warehouse, after receiving the instruction of the operation, the staff understand the details of the relevant operation and find the storage location of the corresponding goods. The warehousing staff will manually tally the goods according to the outgoing list and gather the items in the shipping area. Check the license plate number and the driver’s certificate, check whether the outbound list is consistent with the attached list, and load the vehicle according to the checked list. Warehouse management personnel complete the corresponding information recording work. When counting, select the warehouses, warehouse areas, etc. to be counted according to the count plan, and formulate a count table to generate a count list. The warehousing personnel manually traverse the warehouses, storage areas, etc. to be counted, and transcribe and fill in the corresponding items in the count list. After the inventory is over, the manager will input the inventory information into the computer and compare it with the data in the computer.
2. Existing problems and improvement plans after using RFID intelligent warehouse management system technology
The biggest problem in the inbound and outbound operations is that the barcodes of the items need to be scanned one by one during the verification of the items in the warehouse and the outbound tally. The inventory operation needs to record the items on each location and enter the item information into the information. In the system, this increases the error rate after two turnovers. The essence of the problems in these three operating procedures is the efficiency, accuracy and operating procedures of data collection. From the perspective of warehousing efficiency, data collection efficiency and accuracy are crucial. Barcodes need to be scanned one by one, and it takes 2-3 seconds to scan one barcode on average, which will greatly reduce efficiency. The use of RFID electronic tags can realize the automatic entry and exit of items, automatic inventory, increase the accuracy of query and inventory, and speed up the flow of in and out of the library.
3. RFID intelligent warehouse management system can greatly optimize the above-mentioned warehousing business process by using RFID technology
① In the aspect of warehousing, the check link of the goods and the warehousing items list is scanned by the RFID reader, which improves the checking efficiency. The link between the goods and the cargo space is also completed by the system, and finally the system will submit the corresponding information to the database, reducing the chance of error.
②In terms of outbound goods, outbound goods and cargo location verification, and outbound order review are systematically completed. After the outbound goods are completed, the corresponding goods information in the database needs to be deleted and updated or unused information.
③In terms of inventory, employees only need to scan the cargo location and goods. The verification is completed by the system and the verification results are returned. Compared with the manual verification in the past, the efficiency and quality of the inventory are greatly improved.
Third, the detailed business process after the introduction of RFID intelligent warehouse management system technology
1. RFID intelligent warehouse management system cargo storage
①Preparation stage for supply
The supplier loads the goods into the pallet before supplying the goods, and then writes the goods information on the pallet into the RFID electronic label on the pallet. The goods information includes the product number, batch number, date, quantity, etc. At the same time, the supplier should also provide the inventory list through the Internet, so that the receiver can check and inspect before the harvest.
②Goods acceptance stage (Figure 1)
The goods are transported to the warehouse, and the warehouse staff carry hand-held devices to check, and check the number of pallets in the manifest, the number of goods in each pallet, and the number of boxes in each goods. Each time a pallet is completed, the information in the corresponding RFID pallet tag is modified. When all pallets are checked, the single goods can be put into storage after the inspection is completed.
③The RFID intelligent warehouse management system cargo entry stage (as shown in Figure 2)
After the goods are accepted without error, the forklift driver will select a suitable cargo space after receiving the instruction to place the goods, and send the scanning instructions through the on-board terminal (touch screen) application to control the front RFID reader to control the electronic tags of the pallet and the electronic tags of the cargo space. After scanning, the pallet ID number and cargo location ID number will be displayed on the vehicle terminal. Click “Check Pallet”, and the system will give a prompt: whether the pallet has passed the inspection of the goods receiving stage. If it is confirmed that it has been inspected, the staff Click “Modify Material Quantity” to add the new material information to the database. When all the goods are in the warehouse, return to the previous interface, click “bind pallet” to bind the pallet with the scanned cargo location, put the information in the warehouse, record it in the system, and repeat the above operations until all the goods are in the warehouse In place.
2. RFID intelligent warehouse management system goods out of the warehouse (as shown in Figure 3)
After receiving the shipment order, the truck driver calls up today’s shipment order on the on-board terminal and selects the corresponding shipment order. At this time, the system will prompt the information of the pallet required by the delivery order, including: a list of cargo locations and pallet electronic label numbers. The operator only needs to read the electronic label of the pallet according to the system prompting the cargo position. If the pallet is read incorrectly, the system will prompt an error message and the driver will select the pallet again. If the pallet is correct, select this pallet, enter the material update interface, update the quantity of all related materials under this pallet, and then return to the previous interface, click “separate and bind” to separate the corresponding pallet from the cargo location, when all pallets are out of the warehouse After the update operation is completed, the shipment is completed.
3. RFID intelligent warehouse management system cargo inventory
The staff should regularly check the quantity of goods to ensure that the actual goods are consistent with the system records. Enter the cargo inventory interface, scan the pallet label to obtain the pallet ID, and then click to obtain the inventory, the system will display the number of boxes of all goods in the pallet, and then the staff will scan each box label of this pallet in turn, and the quantity will increase by one for each scan , And finally compare with the quantity given by the RFID intelligent warehouse management system to complete the inventory.
[ad_2]