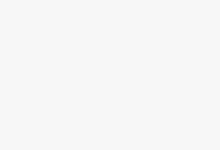
RFID production line management
[ad_1]
620)this.style.width=620;” border=0>
RFID production line management
In order to meet the requirements of ISO 9000, manufacturers have to better track product information and quality control processes in production. The fundamental purpose is to produce better quality products while reducing production costs. There is an indispensable way to implement RFID.
RFID is entering the core of the manufacturing process. By gradually adopting RFID technology at the factory floor level, manufacturers can seamlessly and uninterruptedly obtain information captured from RFID and link to the existing, proven and industrially enhanced control system infrastructure, and the supply chain equipped with RFID functions Coordination, without the need to update the existing manufacturing execution system (MES) and manufacturing information system (MIS), can send accurate and reliable real-time information flow, thereby creating added value, increasing productivity and greatly saving investment.
In a 2004 research report, it was pointed out that accurate and real-time forecasting can significantly improve the performance of the supply chain, thereby reducing inventory by 15%, increasing the completed order rate by 17%, and shortening the cash cycle by 35%.
Real-time information management
For manufacturers, timely and accurate feedback information on the production line is very important. In the past, the information could only be calculated and settled after the end of production, which was time-consuming and laborious, and sometimes it was not very accurate.
620)this.style.width=620;” border=0>
RFID reading equipment can be installed at each node of the production line, and RFID electronic tags that can be read and written repeatedly can be placed on products or trays. In this way, when these products or pallets pass through these nodes, the RFID read-write device can read the information in the labels on the products or pallets, and feed these systems back to the background management system in real time, so that the manufacturer can understand the production line in time Working conditions, even where a product is located. By combining RFID with existing manufacturing information systems such as MES, ERP, CRM and IDM, a stronger information chain can be established so that accurate data can be transmitted in time at the correct time, thereby enhancing productivity and improving asset utilization Rate and a higher level of quality control and various online measurements.
Flexible manufacturing management
Because RFID can provide a constantly updated real-time data stream, combined with the manufacturing execution system, the information provided by RFID can ensure the correct use of labor, machines, tools, and components. With this kind of timely and accurate information management, paperless and contracted production is possible, and it can greatly reduce the downtime of the production line and improve production efficiency.
620)this.style.width=620;” border=0>
If there is a batch or even several batches of contract products, the same production line needs to be used for processing and production, but only some parts are slightly different. In the past production methods, the only way to produce products of the same model was to shut down the production line, make adjustments, and then produce another model of product, which caused losses. By implementing the RFID system, products of different models can be coded and written into the RFID electronic tags. When products of different types enter the processing point, the RFID read-write device reads the information in the RFID active electronic tag, so that the processing equipment can confirm which type of product to process. If there is an automatic sorting conveyor, by identifying the RFID tag, the product classification can be easily completed, so that the product can be sent to the correct production line.
Accurate tracking and tracing
Compliance with FDA quality regulations will encourage manufacturers of consumer packaging products, food and beverages to accurately track and trace product information throughout their entire supply chain. Nowadays, due to the negligence of a certain link, products with quality problems enter the market. These quality problems, the most serious ones, may threaten the lives of consumers. Therefore, it is not uncommon for manufacturers to recall products. Thanks to the help of the RFID system, with accurate and timely information feedback, manufacturers can quickly inquire about the production date, contract number, source of raw materials, and production process of the problematic product, and can even be accurate to a certain problem as needed Product information. In the manufacturing industry, product (tray) identification, intelligent conveyor path selection, date and production time verification, automatic guided vehicles, batch production formulas and other links, the application of RFID systems can achieve real-time information management and flexible Manufacturing management, accurate tracking and tracing of these goals, and improving the level of automated production, production efficiency, making production management more flexible, and ultimately benefiting manufacturers.
[ad_2]