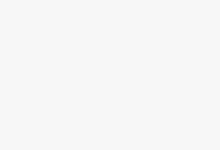
RFID smart warehouse logistics management solution
[ad_1]
1 Project Overview
1.1 Project background
Warehousing management occupies a core position in logistics management. There are many problems in the traditional warehousing industry, such as: inbound and outbound personnel operations are confused, inventory reports are not timely, the attributes of warehouse goods are not clear, the stacking is chaotic, the inventory is inaccurate, etc., all need A complete transformation based on information management technology.
Warehouse management based on RFID technology will change the traditional working methods and processes of warehouse management. All key factors will be affixed to RFID tags and implemented in the core business processes of warehouse management: outbound, inbound, inventory, and inventory control. More efficient and accurate management. RFID technology has the incomparable advantages of long-distance identification, fast identification, hard to damage, large capacity, and other bar codes, simplifying complicated work processes, effectively improving warehouse management efficiency and transparency, and maintaining lean business operations.
Large retailers like the world’s retail giant Wal-Mart have begun to deploy RFID warehouse management systems in their warehouses and distribution centers. Some research institutions estimate that Wal-Mart’s RFID system generates approximately 7 megabytes of data per day. Therefore, for the RFID warehouse management system, how to store and retrieve massive RFID data is also an urgent problem to be solved.
1.2 Project goals
Warehouse Management System (WMS), as a company’s core business system, uses computer software to simulate the system process of warehouse management. Its comprehensive requirements are concise and practical, and the purpose of improving the quality and efficiency of warehouse management.
The centralized placement of materials in a certain place needs to be managed by scientific methods, and efficient and accurate warehousing operations are realized. Under the premise of ensuring basic efficiency, timely cargo update information is submitted to the server database; the upper management system must ensure During the storage period, the quantity of the goods will not change, and the corresponding entry and exit records and regular inventory information will be maintained.
When storing goods, it is necessary to maximize the use of space, and the labor and equipment must be used to the greatest extent and most effectively. The goods can be easily accessed and quickly located when needed. On the other hand, this management system must implement an efficient and accurate inspection and verification mechanism for incoming and outgoing goods, so that a larger number of incoming and outgoing operations can be completed on the basis of no errors in the limited working time, saving manpower to the greatest extent Resource consumption, to avoid errors caused by human factors.
2 project requirements
2.1 Warehouse management system requirements
Traditional warehouse management generally relies on a non-automated, paper-based system combined with manual memory to achieve inventory management. This method is not only time-consuming and labor-intensive, but also error-prone, resulting in low efficiency in the storage of goods and causing immeasurable losses to the enterprise. In order to make up for the shortcomings of traditional warehouse management systems, we design a warehouse management system based on RFID.

The main function of the system
2.1.1 Requirement description of warehousing module
In the finished product packaging workshop, workers first affix RFID electronic tags to the products, and then affix the box label after packing in batches. Those who need to be palletized can also affix the pallet label after the pallet is finished. The general labeling methods are: 1. Single product labeling; 2. Multiple products are packed together, and the outer package is labelled; 3. Pallet labeling, and is associated with the single product label or outer package label data.
The packaged products are put into the warehouse by the loading and unloading tools through the channel composed of RFID readers and antennas. The RFID equipment automatically obtains the warehoused quantity and records it in the system. If the pallet label is affixed, the information of each pallet is written by the import port reader. Pallet labels, at the same time, form the order data association, and then calculate the location through the computer warehouse management information system (or manually specify the location for the batch at the beginning).

2.1.1.1 Business description of warehousing module
Deploy fixed RFID readers at the door of the warehouse, and carry out radio frequency planning according to the on-site environment. For example, four antennas can be installed up, down, left and right to ensure that RFID electronic tags are not missed.
After receiving the warehousing order, put the product into the warehouse according to certain rules. When the RFID electronic tag (ultra high frequency) enters the electromagnetic wave range of the RFID fixed reader, it will be activated automatically, and then the RFID electronic label and RFID fixed reading The writer communicates. When the RFID tag is collected, it will be compared with the order to check whether the quantity and model of the goods are correct. If there are errors or omissions, they will be processed manually. Finally, the goods will be transported to the designated location and placed in accordance with the rules. The main advantage of RFID in warehouse management applications is non-contact long-distance identification, and can be read in batches, which improves efficiency and accuracy.

2.1.1.2 Description of the realization requirements of the warehousing module
The location, quantity, specification and model of each item in the warehouse can be displayed clearly in the warehouse management software, which realizes the visualization of the storage status. After completing the warehousing operation, a warehousing product data sheet should be generated to record the name, type, production date, warehousing time, warehousing batch, quality status, warehousing quantity, warehousing manager, and warehouse code of the warehousing product Wait for information in order to inquire.
2.1.2 Description of requirements for outbound modules
The consignor of the department generates an outbound order according to the invoice required by the sales: that is, according to the outbound priority (such as the first out of the warehouse before the production date) to query the warehouse for outbound goods storage location and inventory status, if specified by the customer The batch number is queried according to the designated batch number, and the outbound cargo pick-up bin and the corresponding pallet belonging to the cargo are generated.
The consignee brings the outbound order to the warehouse manager, and the warehouse manager checks the information to arrange for the loading and unloading personnel to carry out the corresponding product out of the warehouse.
The loading and unloading personnel pick up the goods and pass through the exit gate. The exit gate RFID reader reads the label on the pallet to obtain the outbound information, and verifies whether the product batch number and location listed in the shipped product and the outbound order are correct.
After the delivery is completed, the warehousing terminal prompts the delivery details for the administrator to confirm, and automatically updates the data to the database.
2.1.2.1 Business description of outbound module
According to the pick-up plan, the goods out of the warehouse are sorted and processed and managed out of the warehouse. If the quantity out of the warehouse is large, push the goods to the door of the warehouse in batches, use a fixed reader to communicate with the tags, collect the RFID electronic tags of the goods out of the warehouse, and check whether they correspond to the plan. If there are errors, manually as soon as possible deal with. For a small amount of goods, RFID handheld terminals can be used to collect information from RFID electronic tags (handheld scanners or RFID tablet computers). When an error occurs, an alarm will be issued, and the staff should deal with it in time, and finally send the data to the management center Update the database to complete the delivery.

2.1.2.2 Description of the realization requirements of the outbound module
The loading and unloading personnel receive the shipping instruction and pick up the goods at the designated cargo location. Before taking the loading and unloading personnel’s reader to confirm the accuracy of the goods again, and then send the goods to the conveyor belt at the outbound port, the conveyor belt reader at the outbound port reads whether the label information of the goods is accurate, and the shipment is verified without error.
2.1.3 Description of inventory module requirements
Warehouse management personnel use RFID handheld terminals to walk by each shelf or pallet. They can read the quantity and type of goods on the shelf or pallet, and accumulate them. After the inventory is completed, an inventory report is generated and provided in the system. The data information is compared with the actual inventory quantity in the warehouse for reference by warehouse management personnel. At the same time, the data information in the system can be modified as needed to ensure that the goods and accounts are consistent.
2.1.3.1 Business description of inventory module
In accordance with the requirements of warehouse management, carry out regular and irregular inventory. Traditional inventory is time-consuming, labor-intensive, and error-prone. And all these RFID solves these problems. When there is an inventory plan, the RFID handheld terminal is used to carry out the inventory scan of the goods. The information of the inventory can be transmitted to the back-end database through the wireless network and carried out with the information in the database. Comparing, the generated difference information is displayed on the RFID handheld terminal in real time for verification by the inventory staff. After the inventory is completed, the inventory information is checked with the database information in the background, and the inventory is completed. In the inventory process, the system uses RFID non-contact reading (usually within 1 to 4 meters) to read clothing cargo information very quickly and conveniently. Compared with the traditional model, it will improve a lot of efficiency and inventory accuracy. sex.

3 technical solutions
3.1 Hardware platform
The main hardware devices of the warehouse management system include: UHF fixed readers, handheld readers, electronic tags, application PCs, WEB servers, database servers, etc.
Taking a single warehouse as a unit, the warehouse access management can be managed by a fixed reader, and the inventory and positioning of warehouse materials can be managed by a handheld reader.
3.1.1 Hardware layout
Label placement scheme
Electronic tags are the only signs that mark warehouse goods, so pay special attention to them when placing them. It should be that the placement of the label is directly related to the installation method of the reader antenna and the reading and writing effect of the label. In order to obtain the best read and write effect, the polarization direction of the reader must be consistent with the polarization direction of the tag.
Here, the labels are mainly divided into anti-metal labels and non-metal labels to identify goods with different media. Anti-metal labels are affixed to the surface of metal goods, and non-metallic labels (including cards, stickers, inlays, etc.) are mainly affixed to non-metal goods labels. Goods such as wooden boxes, canvas bags, plastic bags, cartons, etc. can be identified by non-metallic labels.
In warehousing management, pallet-level management is mainly used, that is, the goods on a pallet are used as a unit to complete operations such as storage, storage, and inventory. The size of the standard tray is 120cm*100cm*15cm. Therefore, generally when placing labels, a label is placed on a pallet to identify it, and the placement position is determined according to the specific pallet stacking method. Generally, the stacking height of the goods on the pallet is not more than 80cm, that is, the maximum height of the pallet and the goods stacked is not more than 1m. Let’s take the storage method of pallets as an example to analyze the label placement method.

As shown in the figure, the handheld terminal completes data interaction through the WIFI network. The operator reads the electronic tag on the material through the handheld, and the information of the electronic tag is displayed on the display screen. The handheld device uploads the label information to the wireless AP through the WIFI wireless network, and the wireless AP uploads the data to the background PC through the wired or wireless network, and the PC performs data interaction with the background server through the wireless network.

3.2 Software platform
Operating system: Windows 2000 and above
Data communication: generally use 10/100 Ethernet and RS232 serial port
Database adopts SQLserver2000
The main interface adopts C#/JAVA language programming
The software used by the system includes: warehouse management software, warehouse management software, inventory management software
3.3 Technical architecture

Overall architecture diagram of warehouse management system
4 equipment list
Equipment name
UHF fixed reader (JY-U8910)
UHF Desktop Reader (JY-U8621)
RFID handheld terminal (JY-U7910)
electronic label
server
5 Project implementation method

Guangzhou Jianyong Information Technology Co., Ltd. is a high-tech enterprise specializing in RFID technology research and development and application, management software development and application. For many years, it has been committed to providing complete, systematic and efficient RFID technology and management software integration for domestic and foreign large and medium-sized enterprises Application system solutions.
[ad_2]