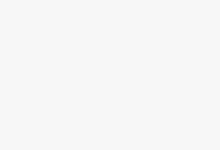
RFID solution for packaging material manufacturing production line
[ad_1]
The packaging industry production line is generally continuous and belongs to a standard continuous production enterprise. The raw materials of the enterprise are mainly plastic particles and related additives. The particles are melted and extruded at high temperature and high pressure to form a film or sheet. Large film rolls are generally required The final product can only be formed after re-cutting and packaging. The specific schematic diagram is as follows:
The application of RFID in production mainly focuses on the slitting process from large rolls to small rolls, and the grouping process between small rolls and small rolls. That is, the RFID label of the large roll is attached to the core of the large roll, and the product electronic code in the label records the identity information of the large roll. When the large roll is slit, the information system can automatically learn the slitting through the RFID reading device Large volume identity information; After the small volume is slit, the RFID tag of the small volume is attached to the core of each small volume. The product electronic code in the label records the large volume information and station information of the small volume. As the basis for the grouping of small rolls, when small rolls are grouped (that is, when materials of the same specification are placed on a tray), the RFID reader senses the data of the RFID tags in the small rolls, and generates the RFID tag code of the tray based on these data. Recycle all small rolls of RFID tags before warehousing, and use pallet RFID tags as the basis of warehousing logistics. Similarly, in the process of warehouse management, the RFID reader antennas installed on both sides of the warehouse aisle are used to complete the reading of the RFID tags on the finished product pallets when entering the warehouse. The use of RFID equipment and RFID tags can realize the unavailability of finished products. People are on duty to enter the warehouse; the outbound operations are similar, and the daily inventory is mainly completed by reading the RFID tags of the inventory trays by the handheld device.
(2) Coding scheme
Barcode management has been used on many BOPP production lines before, and the code value is 39 code. The bar code generation rules are as follows:
It is planned to split the above production batch numbers, according to the EAN.UCC coding rules, adopt the GTIN coding method, and combine the use of application identifiers to link the batch number, production date, net weight and other information in the production process to form the final RFID code.
The specific schematic diagram of the application in the above process is as follows:
Three, program implementation steps
It can be said that the biaxially oriented film production line is a typical packaging material production line. There are still certain difficulties in implementing RFID projects on the BOPP production line. First of all, RFID technology is in a stage of gradual improvement, and related technologies have not yet been applied on a large scale. Corresponding rules and standards are still being formulated, and there are certain risks in such large-scale use in production-oriented enterprises. Secondly, the actual operability of RFID technology in enterprise production and application requires further practice. Once again, the industrial production environment of an enterprise is different from that of a laboratory, requiring RFID-related equipment, electronic tags, and related technologies to have higher reliability, stability and adaptability. At present, suppliers of such equipment are rare, and there is not much room for choice. For these reasons, a lot of work was done before the implementation of the system, and at the same time, the system was implemented steadily and step by step.
(1) Equipment selection test
In view of the fact that there are no successful cases for reference, some RFID equipment has been tested on the production site in the early stage.We have selected two frequencies respectively
The 13.56MHz and 915MHz equipment were tested on site. Through the tests in the processes of large volume identification, small volume grouping, and storage and reading, it was preliminarily decided to use 915MHz equipment in the system plan. The main reason was that the 13.56MHz equipment was used. The recognition distance is not ideal enough,
The position of the label on the tray is relatively strict, which is not conducive to the flexible operation of personnel. In addition, the antenna is susceptible to interference from the external environment. However, 915MHz equipment is not perfect. It is found that the reading stability of 915MHz tags is not enough, especially when the tags are obstructed by objects. In addition, the cost of the 915MHz tag is much higher than that of the 13.56MHz tag, which is too expensive.
(2) RFID equipment simulation operation experiment
In order to ensure the stable and reliable operation of related equipment, a simulated operation test was carried out. Two BOPP production lines that have been put into production were selected for trial operation under simulated conditions. At the same time, the original barcode system was operating normally, and the RFID system operating data and barcode operating data were compared every day. After about one month of simulation operation, the plan of the 915MHz device was confirmed.
(3) Trial run experiment of RFID system
At the beginning of the year, a new BOPP production line put into production at the Asian Packaging Manufacturing Center was put into trial operation, and the RFID system was simultaneously trial run. After many further adjustments and modifications to related equipment, the system has gradually entered normal operation.
[ad_2]