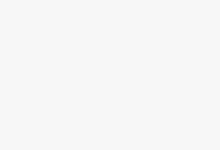
RFID Warehouse Management System
[ad_1]
Preface
Military logistics is an important branch of the social logistics system. It refers to the fact that military materials needed by military forces in life, training, duty, and combat are finally delivered to the troops through financing, transportation, packaging, processing or production, storage, and supply. It is consumed and used to realize the whole process of its space transfer. The accuracy, speed, safety, and control of military logistics are not only a guarantee and support for modern battlefield military operations, but also determine the outcome of a war. Military logistics must build a system based on combat needs. How to achieve the accuracy, speed, safety, and control of the system is the goal that all countries pursue at all costs and develop high-tech.
Although the application of RFID technology in military logistics is an old topic, practical applications have become feasible in recent years, mainly due to the development of integrated circuit technology and the maturity of communication networks. RFID is an automatic identification system that automatically recognizes targets and collects data through non-contact radio frequency signals. It can identify high-speed moving targets and simultaneously recognize multiple targets. It does not require manual intervention, is quick and convenient to operate, and can adapt to various harsh environments. No matter where military materials are in any link of procurement, transportation, storage, use, or maintenance, commanders at all levels can grasp their information and status in real time. RFID can collect and exchange data between the reader and the electronic tag at a very fast speed; it has the ability of intelligent reading and writing and encrypted communication, a unique password in the world, and strong information confidentiality, which requires accurate and fast information for military logistics. , Safe and controllable provide a practical and feasible technical approach.
Current situation and problems
The military warehousing department manually records warehouse changes not only time-consuming and labor-intensive, but also has a high error rate; the current paper records are not easy to keep and back up, which greatly reduces the security of the data; because they are all manual operations, the inventory records are recorded. The inefficiency of update and query results in reduced inventory accuracy; slow delivery and inventory speed make the overall work efficiency inefficient.
In the face of the above problems, the goals to be achieved by the RFID warehouse management project:
Combine the department’s logistics management with radio frequency identification technology to efficiently complete various business operations, improve logistics management, and increase efficiency and value;
Improve the recognition rate of each link in the processing process, without opening the box for inspection, and identifying multiple items at the same time, improving the efficiency of logistics operations;
Reduce the operation cycle, improve the real-time performance of operation data, and dynamically grasp the operation situation in real time, so as to realize the visual management of the whole process of warehousing;
The use of radio frequency technology can greatly improve the efficiency and accuracy of the picking and distribution process, and accelerate the speed of distribution, reduce labor and reduce distribution costs;
To this end, Beijing Ruili Yingfang Technology Co., Ltd. combined domestic and foreign military logistics RFID systems and key technologies, as well as their years of application experience in the civilian field, and formulated a set of solutions for a certain military storage department to realize the visualized management of warehousing materials. Solution: Seal the electronic label into a card shape in the RFID warehouse, stick it on the package or pallet of each goods, and write the specific information of the goods, storage location and other information in the label. At the same time, the detailed information of the delivery party can be written when the goods enter and leave the warehouse, and fixed or portable card readers are installed in the warehouse and various distribution channels to identify and detect the flow of goods.
2.system introduction
2.1 System structure diagram
620)this.style.width=620;” border=0>
Figure 1 System structure diagram
As shown in the process:
1.Warehouse management staff make RFID electronic tags; paste the tags into the warehouse items
2.When entering the warehouse, the warehousing personnel use the handheld machine to scan and input the spare parts information, and store the information into the system through the handheld machine
3. When leaving the warehouse, the system scans and checks the items out of the warehouse through door antennas or handheld computers.
4. Both equipment acquisition and equipment maintenance can be filed in the system using handheld devices.
5.Real-time query of inventory equipment status, quantity and other report information through the system
The RFID warehouse management system is composed of business management software, RFID tag issuance system and RFID tag identification collection system. These systems are connected to each other to jointly complete the various processes of item management. The back-end database management system is the core of the entire system, and RFID identification collection is the basis and means to realize the management function.
The background management software is composed of a central data server and a management terminal, and is the data center of the system. Responsible for communicating with the handheld, converting and inserting the data uploaded by the handheld into the database of the back-end business warehouse management system, and centrally storing and processing label management information, issuing labels and collected label information.
The RFID label issuance system is composed of a special printer for electronic labels and label production management software, and is responsible for completing the information writing of location labels, item labels, and box labels and printing of label surface information.
The dedicated electronic label printer adopts an industrial-grade thermal transfer printer with a built-in non-contact reader, which can print pre-set content information on the label surface while writing information on the label chip. The core of the label production management software is the label production function dynamic link library, which is embedded in the back-end system to provide the back-end warehouse management system with the development interface function for operating the printer to make labels. Based on the dynamic library, an independent label making software is also provided, which can manually input label data to facilitate temporary label making.
The RFID tag identification collection system can collect tag information through a handheld or a fixed-position terminal, complete the storage of tag data, and exchange data with the management center through RFID middleware.
2.1.1 Door access
620)this.style.width=620;” border=0>
As shown in the figure, when exiting and entering the warehouse, the infrared sensor is triggered when passing through the doorway, the reader will automatically start the top, left and right antennas to scan the incoming and outgoing goods, and they can be read out completely without opening the box. All incoming and outgoing goods
2.2 System equipment introduction
2.2.1 RFID electronic tags
620)this.style.width=620;” border=0>
We use alien 9554 UHF paper labels, which have been widely used in warehouse management. For some metal spare parts, we will also use metal labels
2. 2.2 UHF handheld
620)this.style.width=620;” border=0>
This product is a handheld UHF reader-RW915 developed based on Teklogix7527 handheld terminal. Its characteristic is that the read-write distance can be adjusted according to the power, the frequency is adjustable, and it supports ISO18000-6 B and ISO18000-6 C (EPC Class 1 Gen 2) protocols. It can be applied to multiple fields and multiple occasions. The product has high industrial grade, long working time and standby time.
Features:
Adopt large-scale LCD indicator, strong interface expansion ability
Rugged industrial-grade handheld data collector, in line with industrial dustproof and waterproof IP54 standards, with 1.2-meter free fall protection against falling, large capacity, and reliable information storage
Low power consumption, using rechargeable lithium batteries, the power lasts for more than 10 hours
Ultra-high frequency data collection, fast, read and write at 100 tags/sec, read and write distance is about 2 meters
2.2.3 Door access equipment
620)this.style.width=620;” border=0>
Reader antenna
The UHF reader can be flexibly customized according to customer requirements in the working frequency range of 860~928MHZ. With a reading distance of up to 8M and a reading speed of 100KM/H, it can be used in wind, frost, rain, snow, salt , Fog, acid-base, humidity, vibration and other harsh environments. Under normal conditions, the recognition accuracy rate is 99.9999%, and the number of card readings is more than 50 cards per second, which is a relatively stable product among similar products. The product.
2. 2.4 RFID label printer
620)this.style.width=620;” border=0>
SL4000r(TM) MP2 is based on the 5r multi-technology platform and patented MP2 RFID smart coding technology, providing true Gen 2 coding that meets EPCglobal Gen 2 specifications. MP2 complies with EPCglobal Gen 2 hardware certification standards and provides the most advanced encoding technology on the market. It supports EPCglobal Class0, 0+, 1, Gen2 and Philips UCode 1.19 standards, adapts to global frequency requirements and has industry-leading performance.
main feature
● Patented multi-location RFID connection device, which can optimally print a variety of labels
● With advanced RFID calibration function, it can identify tags and mark damaged tags
● Built-in EPC logo simplifies label design and system settings
● The integrated, multi-protocol UHF RFID encoder verified by EPCglobal meets global frequency requirements
2.3 System software introduction
2.3.1 Software structure
620)this.style.width=620;” border=0>
2.3.2 System function
This system uses electronic tags to mark and manage each object that needs to be managed in its management cycle. Managers can use this system to understand and control the nature, status, location, historical changes and other information of each managed object (item) in real time, and take corresponding management countermeasures and measures based on this information to improve the operating level and management of the user unit The purpose of quality.
According to requirements, the system includes several modules: system management, label making, warehousing management, outgoing management, inventory management, allocation management, return management, and report analysis.
System management: system settings and system user information and permissions.
Label production: Generate electronic labels for each item based on the cargo information entered in the warehousing list and label production application form, print the label serial number, product name, model specification on the label surface, and record the detailed product information in the chip.
Inbound management: When entering the warehouse, the warehouse manager will check each item according to the order list, and after the inspection is passed, it will be delivered to the warehouse by the warehouse clerk. The warehouse clerk uses the handheld to scan the shelf location labels and the labels on the warehousing items and enter the number of items for warehousing registration. The data is recorded in the warehousing operation data table in the handheld, and then the items are placed in the designated storage location.
If you need to put items in the packaging box for storage, you also need to scan the box label to update the handheld box list.
After all items have been put in the warehouse, hand the handheld to the administrator, who will import the warehouse data into the back-end management database to complete the warehouse operation.
After this process, the location, quantity, specification and model of each item in the warehouse can be found in the warehouse management software at a glance, realizing the visualization of the warehouse status.
Outbound management: When leaving the warehouse, the warehouse manager queries the storage status according to the picking application, and then makes a pre-stocking list; the keeper takes out the items in the designated warehouse according to the pre-stocking list, and uses the handheld to scan the location label Register the outbound information with the item tag, and record the data in the handheld outbound data table; after all outbound items are taken out, upload the outbound information to the host, compare with the pre-outbound list, and log in according to the actual amount .
Inventory management: Use hand-held data collection terminals to collect data, such as item labels, display shelves, item quantities, etc. The system can automatically generate or manually select and generate inventory task tables according to the product classification set in advance, and perform inventory operations. Inventory operations mainly scan product labels and corresponding location information. After the data is uploaded, the system will automatically list the products that have been on the market and the products that have not been on the market, and perform operations such as inventory profit and inventory loss according to demand.
Allocation management: When there is an allocation situation, different allocation procedures are selected according to the allocation situation.
Maintenance management: When the equipment is damaged or returned to the factory for repair, the device information needs to be written into the label with the handheld to record the complete information of all spare parts.
Report analysis: Perform statistical analysis on system data and generate related reports.
3 System characteristics
1. Combining the entire warehouse management with radio frequency identification technology can efficiently complete various business operations, improve warehouse management, and increase efficiency and value;
2. Improve the recognition rate of items in and out of the warehouse, without opening the box for inspection, and identifying multiple items at the same time, improving the efficiency of in and out of the warehouse;
3. Reduce the inventory cycle, improve the real-time performance of data, dynamically grasp the inventory situation in real time, and realize the visual management of inventory items;
4. The use of radio frequency technology can greatly improve the efficiency and accuracy of the picking and distribution process, and accelerate the speed of distribution, reduce labor and reduce distribution costs;
5. Accurately grasp the material situation and optimize the reasonable inventory.
At present, the level of informatization of warehouse management in our army is generally not high, and most of them are manual management. Only some warehouses have realized barcode management. The most advanced application at present is a two-dimensional barcode system. Although the bar code system is advanced, compared with RFID technology, it has the disadvantages of slow recognition speed, small information carrying capacity, large size, and easy damage. Therefore, the application of RFID technology to warehouse management is bound to be the future development direction.
[ad_2]