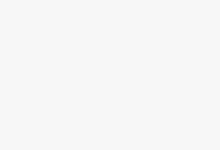
RFID warehouse management system solution
[ad_1]
Application background
Traditional warehouse management generally relies on a non-automated paper document-based system to record and track incoming and outgoing goods. The internal management of the warehouse is completely implemented manually. Therefore, the efficiency of warehouse management is extremely low, and the warehouse that can be managed The scale is also very small. With the popularization of computer applications, most of the enterprise warehouse management data materials have begun to use computer data systems for management, but the data is still collected and statistically organized by first recording on paper and then manually inputting it into the computer. This not only causes a lot of waste of human resources, but also due to human factors, the data entry speed is slow and the accuracy rate is low. With the continuous development of the scale of the enterprise, the number of types of materials managed by the warehouse is increasing, and the frequency of in and out of the warehouse has increased sharply. Warehouse management operations have also become very complex and diversified. The traditional manual warehouse operation mode and data collection method have been unable to meet the requirements of the warehouse. The requirements for fast and accurate management have seriously affected the efficiency of the operation of the enterprise and become a major obstacle to the development of the enterprise.
introduction
At present, RFID technology is bringing a huge change to the supply chain field. It can identify the incomparable advantages of barcodes such as long distance, fast, hard to damage, large capacity, etc., simplify the complicated work process, and effectively improve the efficiency and transparency of the supply chain. The RFID-based warehouse management system of Shenzhen Aostar Electronics Co., Ltd. introduces RFID technology into the existing warehouse management, and performs various operations such as warehouse arrival inspection, warehousing, outgoing, allocation, shifting, inventory counting, etc. Automated data collection of the data to ensure the speed and accuracy of data input in all aspects of warehouse management, to ensure that the company can grasp the real data of the inventory in a timely and accurate manner, and reasonably maintain and control the company’s inventory. Through scientific coding, it is also convenient to manage the batch and shelf life of items. Using the system’s location management function, you can also grasp the current location of all inventory materials in a timely manner, which is conducive to improving the efficiency of warehouse management.

Application Introduction
3.1. RFID system advantages
The RFID solution for warehousing and logistics pallets of Shenzhen Aosta Electronics Co., Ltd. is specially designed for practical applications in the supply chain. This solution adopts passive electronic tags, with long life, maintenance-free, unique design, and can be well embedded in plastic pallets, and it is not easy to be impacted and worn during the transportation of the pallet. In addition, electronic tags can be repeatedly written into data, which is helpful to solve the warehousing and logistics problems of pallet cargo adjustment and assembly. The tags can be recycled, which greatly saves users’ costs. The system realizes long-distance recognition, fast and reliable reading and writing, and can adapt to dynamic reading such as conveyor belt operation, and meets the needs of modern logistics. Advanced data compression technology is used in the label information processing, so that the electronic label carries the pallet load information (data packet), and only needs to scan the pallet electronic label once to understand the item information, eliminating the manpower required for disassembling and reinstalling the pallet Material resources, save time, reduce the error rate and the probability of damage to goods, realize fast and accurate inventory counting, and improve the overall transparency of enterprise logistics.Improve the reliability of data in the management information system, efficient and accurate data collection, improve work efficiency, partition inventory, real-time timely work guidance, accurate and efficient use of scarce resources, and improve production capacity
3.2. Advantages of tray-based digital management
Nowadays, palletization has become an inevitable trend of logistics. Pallet is used by the logistics industry to facilitate the loading and unloading, transportation, storage and distribution of goods. It is a loading and unloading pad composed of a load surface that can carry a number of items and a forklift socket. It is a basic logistics handling device, which has a wide range of application value in commodity circulation, and is known as “moving ground” and “moving cargo platform”. As the basic digital management unit, the pallet is embedded with electronic tags, which will not affect the appearance quality of the goods, but also increase the overall digital average unit number of the goods, which facilitates the realization of accurate digital management of large quantities of goods. The application of electronic tags in logistics distribution centers is based on digital warehouse management application software, computer wireless network technology, and modern logistics three-dimensional high-bay warehouse ideas.
◆ High working efficiency
◆ The damage rate in the logistics process is greatly reduced
◆ Meet the needs of mechanization and automation in the operation process
3.3. RFID forklift application
For logistics application environment, RFID forklift is the best choice
■ When receiving and dispatching, the antenna can be closer to the position of the tag to improve the reading performance
■ The pallet can be tracked continuously in the whole process instead of discrete tracking
■ With the corresponding warehouse management system, it can realize single-step operation control, eliminate manual intervention, improve operation efficiency, improve and strengthen management, and grasp detailed inventory and distribution in real time
Application process
4.1. Storage
When the goods enter the warehouse through the arrival conveyor belt, the reader writes the compressed barcode information of the entire pallet container into the electronic label, and then calculates the shipping position through the computer warehouse management information system, and sends the inventory instruction through the network system Go to the forklift truck system and store it in the corresponding cargo space as required.
4.2. Delivery
After receiving the shipping instruction, the forklift picks up the pallet goods at the designated cargo location. Forklift the front forklift reader to reconfirm the accuracy of the pallet goods, and then send the pallet goods to the conveyor belt at the outbound port, and the conveyor belt reader at the outbound port reads whether the pallet label information is accurate and verifies that the shipment is correct.
4.3. Inventory count
The reader in the warehouse reads the label information of the goods in the warehouse in real time, and checks whether the real-time inventory data is consistent with the warehousing information counted in the database.
4.4. Cargo area positioning and transfer
The reader in the warehouse reads the label information of the goods in real time, and the control center judges the storage area of each goods according to the reader network, counts the usage of the warehouse, and arranges the storage location of the new incoming goods accordingly.
[ad_2]