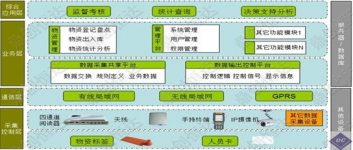
RFID+Barcode Warehousing Intelligent Management System Solution
[ad_1]
Overview of RFID+Barcode
At present, the level of informatization of enterprise warehouse management is generally not high, and most of them are manual management. Only some warehouses implement barcode management. Although the barcode system is advanced, compared with RFID technology, it has slow recognition speed, small information carrying capacity, and large size. , Easy to damage and other shortcomings. RFID has powerful advantages over bar code technology, but RFID also has problems such as relatively high cost at present. Bar code and RFID technology have their own advantages and disadvantages in warehouse management.
According to the needs of warehousing and logistics, Beijing Dingchuang Hengda Intelligent Technology Co., Ltd. has developed an RFID+barcode warehousing intelligent management system using RFID technology and barcode technology in combination with actual conditions. This system reduces user costs, improves work efficiency, and saves resources.
system structure
The system adopts an overall structure based on B/S structure and supplemented by C/S structure to meet the business needs of different users and departments. The back-end database adopts SQL Server 2007, which is reliable, stable and easy to maintain. The network topology of the system is as follows:
System architecture diagram
The RFID warehouse intelligent management system is a comprehensive management platform from the main body. The following integrates multiple independent functional management modules, and the design adopts a four-tier architecture:
Acquisition control layer
It mainly includes the data acquisition and output control equipment at the front end of the system, and the control and management system for these equipment. The RFID reader and antenna cooperate to read the label information on the warehouse materials (the barcode information and the RFID label share a handheld terminal for collection), and upload it to the background management system through the network (wired or wireless) for processing; the camera is used to capture unauthorized out of the warehouse materials Gallery of photos.
Communication layer
It mainly includes the communication network between the front-end equipment of the system and the back-end management system. The network is divided into wired network and wireless local area network.
Business Layer
The business layer is the core processing part of the entire system. The data uploaded from the collection and control layer is analyzed and processed here and then supplied to the business module. At the same time, the input instructions of the business processing module are downloaded to the lower-level hardware execution system. The business modules in this program are mainly two parts: warehouse management and system management.
Comprehensive application layer
The data collected by the equipment is processed and analyzed, and the request processing sent by the user is displayed (statistical query, supervision and assessment), which provides data support for leadership decision-making.
System composition
System selection configuration list
Only the types of RFID equipment required for system operation are introduced here.
Serial number equipment name unit model
1 Electronic label sheet EPC
2 UHF industrial grade handheld (RFID, barcode sharing) DC0681A
3 UHF industrial grade card issuer station DC0661U
4 UHF industrial grade antenna station DC5628
5 UHF industrial grade four-channel reader station DC1634A
6 RFID mobile inventory trolley table customization
7 Barcode printer station is selected according to the situation
System functions
This system uses barcode/RFID electronic tags to mark and manage each object that needs to be managed in its management cycle. Managers can use this system to understand and control the nature, status, location, historical changes and other information of each managed object (item) in real time, and take corresponding management countermeasures and measures based on this information to improve the operating level and management of the user unit The purpose of quality. It can be widely used in warehouse management of enterprises and institutions.
According to requirements, the system includes several modules: system management, label making, warehousing management, outgoing management, inventory management, allocation management, return management, report analysis, and terminal data collection programs.
System management: system settings and system user information and permissions.
Label production: Generate electronic labels for each item based on the cargo information entered in the warehousing list and label production application form, print the label serial number, product name, model specification on the label surface, and record the detailed product information in the chip.
Inbound management: When entering the warehouse, the warehouse manager will check each item according to the order list, and after the inspection is passed, it will be delivered to the warehouse by the warehouse clerk. The warehouse clerk uses the handheld to scan the shelf location labels and the labels on the warehousing items and enter the number of items for warehousing registration. The data is recorded in the warehousing operation data table in the handheld, and then the items are placed in the designated storage location. If you need to put items in the packaging box for storage, you also need to scan the box label to update the handheld box list. After all items have been put in the warehouse, hand the handheld to the administrator, who will import the warehouse data into the back-end management database to complete the warehouse operation. After this process, the location, quantity, specification and model of each item in the warehouse can be found out at a glance in the warehouse management software, realizing the visualization of the warehouse status.
Outbound management: When leaving the warehouse, the warehouse manager queries the storage status according to the picking application, and then makes a pre-stocking list; the custodian takes out the items in the designated location according to the pre-stocking list, and uses the handheld to scan the location label and The item tag registers the outbound information, and the data is recorded in the handheld outbound data table; after all outbound items are taken out, the outbound information is uploaded to the host, and the inventory is compared with the pre-outbound list, and the actual outbound quantity is registered.
Inventory management: Use hand-held data collection terminals to collect data, such as item labels, display shelves, item quantities, etc. The system can automatically generate or manually select and generate inventory task lists according to the product classification set in advance, and perform inventory operations. Inventory operations mainly scan product labels and corresponding location information. After the data is uploaded, the system will automatically list the products that have been on the market and the products that have not been on the market, and perform operations such as inventory profit and inventory loss according to demand.
Allocation management: When there is an allocation situation, different allocation procedures are selected according to the allocation situation.
Return and exchange management: When a customer returns a product, by reading the product label, you can query whether the product belongs to the customer, the sales time and other information, and it is convenient to query the current sales information for effective supervision and management. For products that are confirmed to be returned, the handheld will write the current time into the return time field in the label when reading the label.
Report analysis: Perform statistical analysis on system data and generate related reports.
System Features
1. Combining the entire warehouse management with radio frequency identification technology can efficiently complete various business operations, improve warehouse management, and increase efficiency and value;
2. Improve the recognition rate of items in and out of the warehouse, without opening the box for inspection, and identify multiple items at the same time, improving the efficiency of warehouse in and out;
3. Reduce the inventory cycle, improve the real-time performance of data, dynamically grasp the inventory situation in real time, and realize the visual management of inventory items;
4. The use of radio frequency technology can greatly improve the efficiency and accuracy of the picking and distribution process, and accelerate the speed of distribution, reduce labor and reduce distribution costs;
5. Accurately grasp the material situation and optimize the reasonable inventory.
[ad_2]