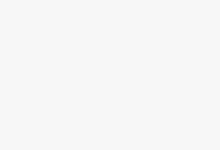
Shanghai Ditong-RFID automated warehouse management system solution
[ad_1]
1 How do companies choose warehouse automation
The benefits of warehouse automation are obvious: automation can speed up processing, improve accuracy, reduce labor costs, improve reliability, and achieve more effective use of warehouse area and space. However, these advantages are not available for free. Automation requires a very expensive investment, and only through the reduction of operating costs can the investment be recovered. This is not an overnight effort. It needs to be considered comprehensively in the medium and long term.
1.1 The pros and cons of warehouse automation
Generally speaking, the automatic storage system (AS/RS) can transport 40-50 pallets per hour in each lane, which is related to factors such as the height and width of the lane, the physical properties of the pallets, and the spacing between shelves. If the elevator needs to replace the tunnel, the time and frequency of a single conversion will affect the operating speed.
Light-duty racks can be used to store cargo boxes. Through automatic storage, 80-100 cargo boxes can be stored in each lane per hour. Nevertheless, through some specialized equipment, the operating speed can be further increased. If the physical characteristics of the equipment and products permit, and there is a real need to increase the workload of the warehouse, two or more containers can be moved per operation.
High-speed sorters can complete 20,000 picks per hour, and some manufacturers even claim higher picking speeds. But it is important to note that the processing speed is closely related to the size, weight and characteristics of the object. When a bar code browser is installed on the RF (radio frequency) terminal and connected to the WMS, the picking speed can be improved by using the RF terminal. Although it is difficult to say exactly how far the RF terminal has improved warehouse operations, this improvement can easily be seen. The work activities of pickers have been more supervised, and the picking is more accurate. Can get more real-time information. RFID tags have more advantages in cargo tracking. Imagine that there are 20 containers on a pallet, and each container contains different goods. With RFID, the information of these goods can be scanned at one time, while the barcodes need to be scanned one by one to determine the nature of the goods, and the scanning speed is greatly improved.
In addition to the perceived benefits mentioned above, automation can also reduce work injuries and cargo damage, improve the company’s image, and reduce dependence on operators, especially when there are special needs and shortages of operators in the warehouse. However, at the same time, automation also has shortcomings: lack of flexibility for changing cargo throughput and types of goods, lengthy project implementation cycles, and deterioration of service quality during project implementation.
It can be seen that automation has brought a higher level of logistics operations, but also brought more execution costs. Therefore, all the pros and cons make it difficult to choose whether to use automation. Then, how to choose the feasibility of warehouse automation? Automation requires very expensive investment, and only through the reduction of operating costs can the investment be recovered. This is not an overnight effort. It needs to be considered comprehensively in the medium and long term. Therefore, the following aspects should be considered when choosing warehouse automation.
1.2 Four questions to consider when choosing a warehouse automation project
1. To review the project, focus on the actual business needs, rather than automation for automation. When considering automation, also consider the manual work that matches it. In fact, basically no three-dimensional warehouse is a real three-dimensional warehouse, any three-dimensional warehouse is a combination of automation and manual. When determining the project, a plan database needs to be established. In general, factors such as warehouse throughput, storage capacity, and the type of goods ordered should be taken into consideration in the next 3 to 5 years.
2. Perform a technical assessment to determine whether automation is appropriate. According to the warehouse throughput and storage needs, it can be determined whether automation is needed and the degree of automation to be achieved.
According to the operation level, warehouse operations can be divided into four levels from low to high: simple manual operations-such as pallet stacking, loading boxes, picking according to paper orders, etc.; machine-assisted operations-using elevators to feed pallets Shelves, or use a straight conveyor to assist in the transportation of boxes; simple automated operations—for example, in warehouses with full pallets in and out, using automatic cranes and simple conveying systems; complex automated operations—including indicator-assisted picking systems, complex Conveying system, high-speed sorting system, etc. As the complexity of warehouse operations and warehouse capacity increase, our choices will also change. For example, when the warehouse handles more than 500 orders per hour, automated operations are put on the agenda.
3. When it is determined that it is necessary to implement automation, the next step is to conduct a detailed review of the equipment’s performance. The optional features of each selected device can be selected only through the “Yes/No” option box. For example, for warehouses that strictly implement first-in first-out, a single-deep automatic storage system is sufficient, and there is no need to use double-deep storage systems or dense crane systems. After such a detailed assessment of the characteristics of the equipment, it is possible to confidently conclude that certain equipment should be discarded.
After this process is over, there may be only two or three more suitable solutions left, and then a comprehensive cost comparison of the remaining two or three solutions. When comparing, consider all related costs. For example, on the basis of considering equipment capital investment, the occupied space, the number of operators, repairs and maintenance are all taken into consideration. The specific costs that may occur include: rent for the area occupied by the equipment, taxes, water, electricity, air-conditioning, fire-fighting equipment, operation and maintenance costs, and labor costs. At the same time, since some of these expenditures are one-time expenditures and some are paid in installments, it is necessary to accurately measure the exact annual operating expenditures of each plan. A more appropriate method is to discount the expenditures related to warehouse automation projects according to the depreciation period of the equipment and the expected rate of return, and compare the discounted cash outflows of each plan. Just like a housing mortgage, the one-time or periodic The cost expenditure is converted into the average expenditure within a certain number of years.
4. Perform sensitivity analysis based on the operating environment parameters and unexpected conditions set during the planning stage. By analyzing whether the final selected plan will change after the operating environment changes, the potential defects of the plan can be found. At this time, the computer simulation test comes in handy. For example, to test the impact of a crane in the automatic storage system on the overall operation after a failure, you only need to enter the relevant parameters. In major automation projects, this is very necessary. It is very easy to test the design on the computer. When entering the contract phase, it is difficult to return after turning around if it is not suitable.
By gradually narrowing the selection range, all types of automation equipment can be taken into consideration. Only through such a thorough analysis can a suitable automation system be selected.
1.3 Implementation and installation of automated warehouse
Obviously, a very important topic about implementation is how long it takes to install and debug. It usually takes no more than one year to build a standard warehouse and install general equipment. If a suitable building can be found, the construction period will be further shortened.
However, the implementation of a fully automated system takes a long time, and the most time-consuming and crucial step is the development of WMS (Warehouse Management System). Don’t underestimate the time it may take, and set unrealistic time limits. In the process of project implementation, it is crucial to ensure the compatibility of warehouses and material handling equipment with WMS. This coordination task starts from the initial process design and runs through the project implementation.
The information system is not compatible with the company’s operational requirements. The most common reason is often that the material handling equipment and WMS are not compatible, or the company’s operational needs are not fully understood during the design phase. It is also very important that the warehouse layout design may be different from your past experience. For example, in a warehouse where pallets are transported by forklifts, if there are enough signs and partitions, it is possible to set up pedestrian walkways connecting them in the roadways. But it is hard to imagine that in the automatic storage system, there will be a situation where connecting channels are opened in the roadways. Asking technical experts in the early stages of the project can effectively avoid related errors.
In short, the work of avoiding the failure of automation projects starts from the early stage of project formulation. Only by doing meticulous and thorough data analysis and reaching agreement on operational goals and customer service levels can everyone work together to ensure the ultimate success of the automation project.
2 Application of RFID technology in warehouse management
With the rapid development of RFID technology, it is being widely used in highway toll collection, attendance, and access control due to its low pollution, abrasion, and scratching, and the label itself is a passive component, small in size, durable and reliable, and rapid and convenient in operation. , Restaurant bookkeeping and identity recognition systems have brought unprecedented convenience to people’s lives.
At present, warehouse management is mainly realized based on corresponding standardized manual operations and computer semi-automatic management. The disadvantages are obvious, that is, a lot of manpower needs to be invested in standardizing the placement of items, regular inventory and check-in/out, which makes the warehouse management problem very cumbersome and wastes a lot of time. Therefore, it is ideal to apply RFID technology to warehouse management, which is also a new application field of RFID technology.
2.1 Warehouse management system based on RFID technology
The purpose of the design of the warehouse management system based on RFID technology is to realize the automation of goods out/in control, goods storage location and quantity statistics, and information inquiry process, so as to facilitate the management staff to carry out statistics, inquiry and grasp the flow of materials. In order to meet the requirements of convenience, speed, safety and efficiency, the system is designed as follows.
1.System composition
The hardware of the warehouse management system based on RFID technology includes: host computer, printer, inbound/outbound reader, location reader, mobile reader, RS-485 interface card, electric control door, alarm detection device, etc. The host computer is installed with management software, which is connected to the warehouse reader and all position readers through the RS-485 interface card and controls them, such as setting permissions, reading records, and statistical inquiries; position reading The writer records the placement of items, the out/in storage reader controls the electric control door, collects items in and out of storage records, etc. The system structure is shown in Figure 12.6. This system uses RFID electronic tags as the identification of items, storing its model, production date, quantity and other information.
620)this.style.width=620;” border=0>
This system management software is developed under the Windows 98 environment and adopts VB 6.0. It mainly includes five modules: system setting, warehousing management, outgoing management, material management and database management.
System settings include functions such as password modification, warehouse area, reader address, serial port and alarm rule setting;
Outbound/inbound management includes functions such as reading/writing electronic tags, adding and deleting records, and generating reports;
Material management includes functions such as material positioning, inventory, statistics and report generation;
Database management performs operations such as browsing, querying, and sorting the database, and can only modify or edit part of the information, such as the degree of damage, remarks, etc., without the right to add or delete any records.
2.The main function of the system and its realization
(1) Material positioning
When items enter and exit a certain area of the warehouse, they need to pass through the location reader of the area. The reader records the item, and the logic circuit determines the direction of the item, as shown in Figure 12.7. The host receives the records and access identification, and modifies the database. If the item enters a certain area, the record is added to the area in the database; otherwise, the record is deleted. This realizes the one-to-one correspondence between the actual location of the warehouse materials and the information in the host database, which brings great convenience for the management personnel to inquire, check, and find materials.
620)this.style.width=620;” border=0>
(2) Outbound/inbound management
Material export/in-warehouse registration is an important link in warehouse management. Once the types and quantities of items are too large, the workload will be large and error-prone, which may cause the loss of national property or corporate property. Based on the principle of prudence, the system adopts dual management of manual inspection and automated office. The workflow of the warehouse management subsystem is shown in Figure 12.8. The advantage of this system is the synchronization of material export/in-warehouse and database addition/deletion, and finally generate reports, which greatly reduces the workload of management personnel.
620)this.style.width=620;” border=0>
It should be noted that the outbound/inbound reader/writer in this system is similar to the position reader, and it is equipped with two infrared receivers to determine whether it is an inbound operation or an outbound operation. In addition, under normal circumstances, the electric baffle works under the control of the “AND” of manual instructions and the instructions of the reader/writer reader. When the reader works abnormally, it can be manually opened or closed.
(3) Material inventory
In warehouse management, regular inventory is an indispensable work. The system is also equipped with a mobile reader. The staff can quickly complete the material inventory task by holding it and patrolling in the warehouse. The specific process is: sub-regional; the reader reads the information of the RFID electronic tag, and sends it to the host as a record and stores it in the new database; after reading an area, the host compares the old and new databases in the area and records the results; enter the next Repeat the above process for one area. After the warehouse inventory is completed, material statistical reports and difference reports are generated to facilitate timely detection of problems.
3.Interface communication design
The host computer is connected to the warehouse reader/writer, position reader and mobile reader through RS-232 serial port or RS-485 serial interface card (networking).
(1) Reader interface protocol
Command/response format “length command word address parameter checksum”, where the length is the number of bytes from “command word” to “checksum”, address allocation is as follows: host address is 00H, out/in library read and write The address of the reader is FFH, the address of the position reader is 01~F0H, and the address of the mobile reader is FEH; the parity is even parity.
The serial port parameter baud rate is 9600, 8 bits, 1 stop bit, no parity.
(2) Interface function
The system uses Windows API communication interface functions to realize data communication between the host and each reader.
4.System security analysis
With the rapid development of RFID technology, various RFID electronic label manufacturers provide users with more and more complete security systems. First of all, the serial number of each label is unique and has been solidified during the production process and cannot be changed. In the communication security, the three-time mutual inductance verification technology conforming to the ISO 9798 international standard is used to verify the legitimacy of the electronic tag and the reader; in the data communication, the DSA algorithm is used to encrypt the data to ensure that the data is not Illegal modification. The authorization method is adopted in the read-write control, that is, the read-write device must first obtain the authorization of the “device authorization tag” to read and write the electronic tag of the system, and the initialization of the electronic tag must be authorized by the superior authorized tag, and only On the designated authorized device. Therefore, there is no problem of password cracking in the authorization method, and the security of the system can be guaranteed as long as the authorization label is not stolen.
Therefore, the correct regulation of the RFID electronic tag management system, and the proper storage and use of authorization cards will ensure the high security of the system.
5.Two points of explanation
(1) Due to the short reading and writing distance of RFID electronic tags, it is necessary to standardize the operation of warehouse managers to ensure the effective reading and writing of data;
(2) The price of RFID electronic tags is more expensive, and there are many types and quantities of items in the warehouse, so it is required to configure the electronic tags reasonably to make the system cost-effective.
2.2 Summary
The design and implementation of a warehouse management system based on RFID technology is a new application of RFID technology. With the continuous development of RFID technology, it is believed that in the near future, its read-write distance will continue to improve, which will bring greater convenience to warehouse management and thus generate more positive social benefits.
[ad_2]