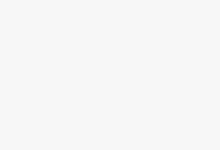
Smart RFID bonded logistics warehouse warehousing solution
[ad_1]
The smart warehousing solution of Siemens Technology automatically collects data from various operations such as warehouse arrival inspection, warehousing, outgoing, allocation, shifting, inventory counting, etc., and through various wireless channels, handheld terminals and vehicle-mounted terminals Upload the collected data to the back-end system in real time to ensure the speed and accuracy of data input in all aspects of warehouse management, to ensure that the company can grasp the real data of the inventory in a timely and accurate manner, and reasonably maintain and control the company’s inventory. Using the system’s location management function, you can also grasp the current location of all inventory materials in a timely manner, which is conducive to improving the efficiency of warehouse management.
The imported bonded warehouse system is a business management system developed by the technology research and development team around me mainly for cross-border import e-commerce, which is suitable for third-party bonded warehouse company management business customization. It is supported by large domestic warehousing and logistics service providers and is more targeted Strong, mainly to solve the domestic cross-border import e-commerce bonded warehouse and direct mail logistics business system solutions.
Side Technology Warehouse Management System is a very user-friendly and excellent management software, providing you with the simplest and clearest warehouse management solutions. Widely applicable to: third-party logistics, foreign trade enterprises, medicine, auto parts, food, clothing, electronics and other industries in the factory for material procurement and storage, production and distribution and requisition, wholesale and retail company commodity procurement and storage, and out-of-stock accounting. It can accurately print special bills for charges in various provinces across the country, and can also easily customize the styles of inbound, outbound, delivery notes, delivery notes and other styles you need, and can output commonly used detailed reports and summary reports, which is to enhance the company’s image , A right-hand man to strengthen management.
Traditional warehouse management adopts manual methods. The recording method is cumbersome, inefficient, human factors are large, accuracy is not high, falsified data are prone to occur, human resources are wasted, management and maintenance costs are high, which makes it difficult to guarantee receipt, inspection and delivery. The correctness of the goods, resulting in inventory, delayed delivery, and further increase costs, so as to lose the opportunity to serve customers, and manual management methods can not provide managers with real-time, fast, and accurate warehouse operations and inventory information, so as to implement timely, Accurate and scientific decision-making.
With the rapid development of today’s information management technology, wireless communication technology, barcode and RFID technology, the era of fully automatic, digital, and real-time warehouse management has arrived. More and more new technologies such as: barcode, wireless communication technology and RFID and other related technologies are gradually being applied in all aspects of warehousing production.
Suibi Technology provides a large number of technical modules, which can be flexibly designed according to your requirements and customized personalized intelligent storage system solutions.
Intelligent warehousing system is a system that is controlled by a computer system, can fully grasp the location of warehouses and materials, and realizes automatic warehousing and warehouse management through trolleys and related handling equipment. The whole work process does not require direct human involvement, which greatly improves work efficiency.
Features of Intelligent Warehousing System
Smart warehousing is a link in the logistics process. The application of smart warehousing ensures the speed and accuracy of data input in all aspects of cargo warehouse management, ensuring that companies can accurately and timely grasp the true data of inventory, and reasonably maintain and control corporate inventory. Through scientific coding, it is also convenient to manage the batch and shelf life of the stocked goods. Using the location management function, you can also grasp the current location of all inventory goods in a timely manner, which is conducive to improving the efficiency of warehouse management.
It is an integrated bonded logistics system for warehousing and customs declaration, which fully meets the customs’ regulatory requirements for bonded warehouses. Professional warehousing system, warehousing operation management throughout the process, system guidance business operations, easy to achieve refined warehousing management. Realize the four-in-one service system of bonded warehouses, general trade, processing trade, and supply chain finance, improve the structure of supply chain services, reduce enterprise operating costs, truly provide customers with professional, efficient and safe service solutions, and create maximum corporate benefits.
Bonded warehouses (bonded storage of imported goods) and export supervised warehouses (bonded storage of goods to be exported) are the basic forms and carriers of bonded logistics. Compared with the two, special areas mainly integrate, integrate, and expand “bonded warehouses” and The function of “export supervision warehouse” means that goods enter the center from abroad to be bonded, and enter the center from China to enjoy export tax rebates. The center can also carry out such as bonded warehousing, simple processing and value-added services, international logistics and distribution, import and export trade, and international For many businesses such as transit and entrepot trade, logistics information processing, the customs also gives bonded warehouses certain port functions.
Applicable business: Bonded warehouse logistics company manages third-party B2C e-commerce model bonded warehouses.
Overview of system requirements analysis:
Warehouse Management System (WMS), as the core business system of technology companies around us, uses computer software to simulate the system process of warehouse management. Its comprehensive requirements must be concise and practical, and improve the quality and efficiency of warehouse management.
The centralized placement of materials in a certain place needs to be managed by scientific methods, and efficient and accurate warehousing operations are realized. Under the premise of ensuring basic efficiency, timely cargo update information is submitted to the server database; the upper management system must ensure During the storage period, the quantity of the goods will not change, and the corresponding entry and exit records and regular inventory information will be maintained.
When storing goods, it is necessary to maximize the use of space, and the labor and equipment must be used to the greatest extent and most effectively. The goods can be easily accessed and quickly located when needed. On the other hand, this management system must implement an efficient and accurate inspection and review mechanism for incoming and outgoing goods, so that a larger number of incoming and outgoing operations can be completed within a limited working time on an error-free basis, saving human resources to the greatest extent Consumption, to avoid the occurrence of errors caused by human factors. In addition, the RFID intelligent warehouse management system must ensure that it can efficiently complete the statistics of the types and quantities of goods, manage the maximum utilization of storage space and ensure the premise of ensuring the correct quantity of materials. Therefore, an efficient inventory function is indispensable.
The composition of the intelligent warehousing system:
One is a computer management system, which is actually a set of software systems. There is a database in the system that can record the inventory status of the warehouse in real time. At the same time, it can issue instructions as needed to guide the various parts of the intelligent storage system for bins to take corresponding actions. Realize warehousing function;
The second is the stacking system, which is similar to equipment such as forklifts and hoists. It can automatically find the position of the shelf through its own sensing device, and can accurately stack the materials through calculation;
The third is the conveying system, which includes many kinds of equipment, such as conveyor belts and other equipment that can automatically complete the conveying of materials.
Through the organic combination of these three systems, the intelligent storage system for bins can realize its functions to the greatest extent and play its role.
Intelligent warehousing system application: suitable for warehousing systems in various industries, currently widely used in manufacturing, e-commerce, and logistics and distribution industries.
The detailed business process after the introduction of RFID intelligent warehouse management system technology:
1. RFID intelligent warehouse management system cargo storage
①Supply preparation stage: Before supplying goods, the supplier loads the goods into the pallet, and then writes the goods information on the pallet into the RFID electronic label on the pallet. The goods information includes product number, batch number, date, quantity, etc. . At the same time, the supplier should also provide the inventory list through the Internet, so that the receiver can check and inspect before the harvest.
②Goods acceptance stage: The goods are transported to the warehouse, and the warehouse staff carry hand-held devices to check, and check the number of pallets in the manifest, the number of goods in each pallet, and the number of boxes in each goods. Each time a pallet is completed, the information in the corresponding RFID pallet tag is modified. When all pallets are checked, the single goods can be put into storage after the inspection is completed.
③Cargo in-place stage of RFID intelligent warehouse management system: After the goods are accepted correctly, the forklift driver will select a suitable cargo space after receiving the in-place instruction, and send out the scanning instruction through the on-board terminal (touch screen) application to control the front RFID reading and writing The scanner scans the pallet electronic label and the cargo location electronic label. At this time, the pallet ID number and cargo location ID number will be displayed on the vehicle terminal. Click “Check Pallet” and the system will give a prompt: whether the pallet has passed the goods receiving stage If it is confirmed that it has been tested, the staff clicks “modify material quantity” to add the new material information to the database. When all the goods are in the warehouse, return to the previous interface, click “bind pallet” to bind the pallet with the scanned cargo location, put the information in the warehouse, record it in the system, and repeat the above operations until all the goods are in the warehouse In place.
2. RFID intelligent warehouse management system goods out of the warehouse
After receiving the shipment order, the forklift driver calls up today’s shipment order on the vehicle-mounted terminal and selects the corresponding shipment order. At this time, the system will prompt the information of the pallet required by the delivery order, including: a list of cargo locations and pallet electronic label numbers. The operator only needs to read the electronic label of the pallet according to the system prompting the cargo position. If the pallet is read incorrectly, the system will prompt an error message and the driver will select the pallet again. If the pallet is correct, select this pallet, enter the material update interface, update the quantity of all related materials under this pallet, and then return to the previous interface, click “separate and bind” to separate the corresponding pallet from the cargo location. When all pallets are out of the warehouse After the update operation is completed, the shipment is completed.
3. RFID intelligent warehouse management system cargo inventory
The staff should regularly check the quantity of goods to ensure that the actual goods are consistent with the system records. Enter the cargo inventory interface, scan the pallet label to obtain the pallet ID, and then click to obtain the inventory, the system will display the number of boxes of all goods in the pallet, and then the staff will scan each box label of this pallet in turn, and the quantity will increase by one for each scan , And finally compare with the quantity given by the RFID intelligent warehouse management system to complete the inventory.
System architecture:
The first data collection layer: RFID Tag, barcode, handheld terminal, vehicle-mounted terminal, fixed and antenna.
The second communication layer: various wireless communication technologies WIFI, Bluetooth, GPRS, 3G, etc.
The third layer of application layer: complete the processing of the collected data, including functions such as inbound management, outbound management, and location management.
The fourth layer of data integration layer: complete the interconnection with other systems in the enterprise to realize data sharing and transparency.
Hardware environment and technology:
(1) Wireless network technology: Through reasonable deployment of wireless APs, wireless signals can fully cover any corner of the enterprise. Such a wireless network can provide storage enterprises with a real-time data transmission path, so that all kinds of information can flow unimpeded.
(2) Handheld terminal and vehicle-mounted terminal: warehouse staff can use handheld or vehicle to complete receiving (goods and pallets), warehousing, shipping (goods and pallets unbinding), goods transposition, goods unpacking, Return processing, inventory counting, etc. The driver of the loading vehicle can use the vehicle to complete the entry (the pallet is bound to the cargo space) and the exit.
(3) RFID technology: RFID identification is a non-contact automatic identification technology. Including two parts: tag and reader. Tag identifies target objects and obtains relevant data through radio frequency signals, can work in various harsh environments, and can identify multiple tags at high speed.
(4) Barcode technology: Barcode has the characteristics of fast recognition speed, high recognition rate and low cost.
The application of the intelligent warehouse management system ensures the speed and accuracy of data input in all aspects of cargo warehouse management, ensuring that enterprises can grasp the real data of inventory in a timely and accurate manner, and reasonably maintain and control enterprise inventory. Through scientific coding, it is also convenient to manage the batch and shelf life of the stocked goods. Using the system’s location management function, you can also grasp the current location of all inventory goods in a timely manner, which is conducive to improving the efficiency of warehouse management.
Warehouse management occupies a core position in logistics management. The traditional warehousing industry is based on the business model of collecting storage fees, and hope that their warehouses are always full. This model runs counter to the purpose of logistics. Modern logistics takes the responsibility of integrating processes and coordinating upstream and downstream. The smaller the static inventory, the better. Its business model is also based on the assessment of the total logistics cost. Since these two types of warehouse management have essential differences in business models, they are difficult to distinguish in specific operations such as warehousing, outgoing, sorting, and tallying. Therefore, we must pay attention to their similarities and differences in analysis and research. Similarities and differences will also be reflected in the structure of the information system. As the manufacturing environment changes, product cycles are becoming shorter and shorter, a variety of production methods are available, and the requirements for inventory restrictions are getting higher and higher. Therefore, it is necessary to establish and implement a supply chain management system, with the help of computerization and information technology to connect suppliers, Manufacturers and customers are closely united to share inventory risks. Warehousing management can be briefly summarized as 8 key management modes: tracking-receiving-checking-storing-picking-issuing-stocking-returning.
The optimal control part of inventory is to determine the business model of the warehouse, that is, to determine the management objectives and management mode of the warehouse (according to the requirements of the previous design). If it is an execution link in the supply chain, it is a cost center. With service quality and operating costs as the control objectives, we pursue reasonable inventory or even zero inventory. Therefore, an accurate understanding of warehouse item information is very important to the system, so we propose to solve accurate warehouse management.
Warehousing management and precise positioning play a very important role in the entire management process of an enterprise. If timely and accurate purchase, inventory control and delivery are not guaranteed, it will bring huge losses to the enterprise, which is not only manifested in the management of the enterprise. The increase in costs will also make it difficult to guarantee the quality of customer service, and ultimately affect the market competitiveness of the company. Therefore, we proposed a new RFID-based warehouse system solution to solve the problem of precise warehouse management.
Drawback analysis and problem improvement of traditional warehousing business process:
1. Traditional business analysis
When warehousing, the warehouse management staff receives the warehousing operation instruction, and according to the conditions of the warehousing items, selects the warehouse and arranges the storage area for the items. Warehousing personnel check the inventory with the inventory and physical objects according to the inventory of the warehousing operations, and check and accept the warehousing items. Use barcode scanning method to count and check the total quantity of goods arrived, unit packaging, etc. After the acceptance is completed, the warehouse operator will store the goods in the designated area according to the location arrangement plan, and the warehouse management personnel will complete the corresponding information recording work and input it into the computer. When leaving the warehouse, after receiving the instruction of the operation, the staff understand the details of the relevant operation and find the storage location of the corresponding goods. The warehousing staff will manually tally the goods according to the outgoing list and gather the items in the shipping area. Check the license plate number and the driver’s certificate, check whether the outbound list is consistent with the attached list, and load the vehicle according to the checked list. Warehouse management personnel complete the corresponding information recording work. When counting, select the warehouses, warehouse areas, etc. to be counted according to the count plan, and formulate a count table to generate a count list. The warehousing personnel manually traverse the warehouses, storage areas, etc. to be counted, and transcribe and fill in the corresponding items in the count list. After the inventory is over, the manager will input the inventory information into the computer and compare it with the data in the computer.
2. Existing problems and improvement plans after using RFID intelligent warehouse management system technology
The biggest problem in the inbound and outbound operations is the need to scan the barcodes of the items one by one during the verification of the items in the warehouse and the outbound tally. The inventory operation needs to record the items on each location and enter the item information into the information. In the system, this increases the error rate after two turnovers. The essence of the problems in these three operating procedures is the efficiency, accuracy and operating procedures of data collection. From the perspective of warehousing efficiency, data collection efficiency and accuracy are crucial. Barcodes need to be scanned one by one, and it takes 2-3 seconds to scan one barcode on average, which will greatly reduce efficiency. The use of RFID electronic tags can realize the automatic entry and exit of items, automatic inventory, increase the accuracy of query and inventory, and speed up the flow of in and out of the library.
3. RFID intelligent warehouse management system uses RFID technology to greatly optimize the above-mentioned warehousing business process by surrounding technology
① In the aspect of warehousing, the check link of the goods and the warehousing items list is scanned by the RFID reader, which improves the checking efficiency. The link between the goods and the cargo space is also completed by the system, and finally the system will submit the corresponding information to the database, reducing the chance of error.
②In terms of outbound goods, outbound goods and cargo location verification, and outbound order review are systematically completed. After the outbound goods are completed, the corresponding goods information in the database will be deleted, and the information will be updated or unused.
③In terms of inventory, employees only need to scan the cargo location and goods. The verification is completed by the system and the verification results are returned. Compared with the manual verification in the past, the efficiency and quality of the inventory are greatly improved.
The functions of the WMS system of the technology around you:
Storage location management: Use a data collector to read the product barcode, query the specific location of the product in the storage location, and realize all-round management of the product.
Through the terminal or data collector, you can check the storage situation, space size and the maximum capacity of the product in real time through the terminal or data collector, and manage the area, capacity, volume and equipment limits of the warehouse.
Product quality inspection: After the finished product is packaged and pasted with a barcode, it is transported to the temporary storage area of the warehouse for inspection by the quality inspection department. The quality inspection department scans the packaging barcode of the unqualified product and makes a corresponding record on the collector for inspection. After completion, connect the collector to the computer and upload the data to the system; generate a quality inspection form for qualified products, and the warehouse staff will perform the production warehousing operation.
Product warehousing: download the warehousing task from the system to the collector, scan the barcode on one of the product packaging when warehousing, enter the corresponding quantity on the collector, and scan the barcode of the cargo location (if the goods are specified in the warehousing task The collector will automatically check the cargo location). After the collection is completed, the data will be uploaded to the system, and the system will automatically process the data. The database records the variety, quantity, warehousing personnel, quality inspection personnel, and cargo All necessary information such as location, product production date, team and so on, the system accumulates the products of the corresponding location.
Material distribution: The ingredient list generated according to different cargo positions contains very detailed ingredient information, including ingredient time, ingredient station, ingredient details, ingredient quantity, etc. The relevant custodians can automatically form an early warning based on these barcode information when picking goods. The details and quantity information of the wrong ingredients can be warned and prompted, which greatly improves the work efficiency of the warehouse management staff.
Product delivery: When the product is delivered from the warehouse, the warehouse staff will find out the corresponding product data from the system and download it to the collector based on the delivery note of the sales department according to the first-in-first-out principle, and formulate the delivery task to the designated location. Scan the barcode of the cargo location (if the cargo location is wrong, the collector will alarm), and then scan the barcode of one of the products, if it meets the conditions of the outbound task, enter the quantity to execute the outbound, and check or record the transportation unit and vehicle information (for Product tracking and retrospective use in the future), otherwise the collector can give an alarm.
Warehouse return: According to the actual return situation, scan the barcode of the returned goods, import the system to generate the return form, and generate the return details and account accounting after confirmation.
Warehouse inventory: According to the company system, the inventory task is formulated in the system according to the warehouse, variety and other conditions to be inventoryed, and the inventory information is downloaded to the collector. The warehouse staff performs inventory by scanning the product barcode in the designated area and entering the quantity. After the collection is completed, the data is uploaded to the system and an inventory report is generated.
Inventory warning: In addition, the warehouse link can set the upper and lower warning lines for the total amount of warehouses and each product according to the actual situation of the enterprise. When the inventory quantity is close to or exceeds the warning line, an alarm will be issued to adjust production and sales in time to optimize the enterprise Production and inventory.
Quality traceability: The data accuracy of this link is closely related to various previous operations. The flow of related products can be tracked at each information point according to various attributes such as production date, variety, production team, quality inspector, batch, etc.; at the same time, the product can also be traced upwards according to related product attributes and operating point information . Information query and analysis reports are based on this system. Multiple clients can be set up as needed, and different authorities can be set for different departments. Whether it is the production department, the quality inspection department, the sales department, and the leadership decision-making department, they can be assigned according to the The authority can query all kinds of reliable information related to production, inventory, sales, etc. in the first time, and can conduct data analysis. At the same time, it can generate and print reports in the prescribed format.
Does wms warehouse management software bring huge benefits to users? Mainly manifested in:
1. Timely data collection, precise process management, fully automated and intelligent guidance, improve work efficiency;
2. Precise location management and comprehensive status monitoring of storage locations, making full use of limited storage space;
3. Goods are put on and off the shelves, fully intelligent, first in, first out, automatically allocates the storage space on and off the shelves, avoiding human error;
4. Real-time control of inventory conditions, reasonable maintenance and control of corporate inventory;
5. Through the automatic collection of batch information, the traceability of the product production or sales process is realized.
More importantly, bar code management promotes the transformation of the company’s management model, from traditional management based on experience to management based on precise digital analysis, post-management is transformed into management in-process and real-time management, which accelerates capital turnover and enhances the supply chain. Response speed, these will definitely enhance the company’s overall competitiveness.
The functional modules of the warehouse management system and abundant open APIs are compatible with the cross-border e-commerce ERP customs clearance service platform, customs supervision terminal, and station system. Applicable to all types of e-commerce bonded warehouses, e-commerce overseas warehouses, e-commerce local warehouses, etc. Cross-border e-commerce customers can use PC and handheld mobile communication terminals to manage their own warehouses anytime, anywhere. The system can be seamlessly connected with the cross-border trade clearance information platform of each pilot city to realize the paperless full declaration of customs data.
The cross-border import transshipment system is a business management system customized for the third cross-border logistics company. The entire business process is controlled and operated through the system for efficient operation.
The Smart Bonded Warehouse Management System of SuiZhou Technology is an intelligent management software designed and developed for the complex material storage management business. Through real-time collection of detailed information of each node of material turnover, it realizes the full-cycle management of material movement from physical objects to financial accounting. The system is designed based on the concept of the optimal total cost of supply chain management. Through the application of labels/barcodes and RF equipment, it makes full use of the Internet of Things and mobile Internet technologies to carry out digital identification and intelligent perception of storage locations and materials, and improve operations in all links Efficiency and accuracy, real-time sharing of information, speeding up material turnover, improving the level of guaranteed supply services and continuously optimizing the inventory structure to reduce inventory costs.
[ad_2]