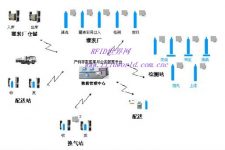
Suggested solutions for industrial gas cylinder safety and circulation retail management system based on rfid technology
[ad_1]
Project background
With the rapid development of industry, industrial gases have been increasing in my country in recent years. However, there are many problems in the industrial gas retail/wholesale market. Industrial gases are flammable, explosive, and toxic. The rational use and management of industrial gas cylinders When it comes to the safety of life and property, improper handling will cause irreparable loss of life and property. The asset and safety issues of the bottled industrial gas market have attracted attention from relevant state departments.
In order to regulate the bottled market, my country has introduced a series of governance measures. Such as: steel cylinders are placed under the trusteeship of industrial gas companies, and they are uniformly inspected; increase the business access threshold to prevent unlicensed operations; strict workflow management, strengthen safety management, and so on. These measures have undoubtedly brought many benefits to regulating the market, but human factors still account for a large proportion of management.
How to use high-tech means to strengthen market safety management, market supply management, and reduce operating costs, so that various measures of the enterprise can be implemented truly and effectively, and to strengthen management is an urgent problem that needs to be solved.
The main problems in the circulation of industrial gas cylinders
For a long time, due to poor management of gas cylinders, loss of assets, outdated and inefficient distribution systems, high management costs, diversified property rights and difficult management, loopholes in the internal workflow of enterprises, illegal profit-making, and rampant black gas have become prominent problems in the bottled LPG market. .
Specifically, security and anti-counterfeiting issues, property loss issues and management issues:
1. Security and anti-counterfeiting issues:
1. At present, the gas cylinder filling industry generally has many problems such as unknown number of gas cylinders, unclear safety status, and unclear property rights information. Cylinders are circulating in the society and it is difficult to implement safety responsibilities, causing great safety hazards.
2. Regular safety inspections cannot be implemented, or gas cylinder users do not use gas cylinders in accordance with safety requirements or illegally modify or refurbish gas cylinders, resulting in a large number of gas cylinders on the market that have not been inspected normally, some of which may have been damaged to varying degrees , And cannot be identified and verified, and there are serious security risks.
3. Some units and individuals fill or pour gas between gas cylinders without permission. Some licensed gas cylinder filling units operate in violation of regulations, resulting in overfilling or wrong filling of gas cylinders, resulting in gas cylinders Accidents occurred in large numbers.
2. The loss of property and the problem of not being able to trace back:
1. The number of internal gas cylinders in the industrial gas filling unit is unknown, and it is difficult to distinguish the internal gas cylinders from the external gas cylinders, which may easily cause the loss of their own property.
3. Management efficiency and cost issues:
1. The dynamic management of gas cylinders entering and exiting the filling station, inspection station, and ventilation station cannot be realized, and the inventory status, production and sales status cannot be controlled and inquired in real time.
2. It is difficult to strictly control the circulation of gas cylinders between various operations within the enterprise, and gas cylinders that have exceeded their service life or have been judged to be scrapped may enter the filling and circulation links.
3. The historical records of the circulation process of gas cylinders inside and outside the enterprise cannot be inquired. The root cause of the problem cannot be determined when needed, and the hidden danger of accident cannot be discovered in time, which may produce more serious consequences.
4. Although existing enterprises have partially used modern management methods, there is a gap in the integration of information applications and actual needs.
Plan to achieve goals
Perform dynamic statistics and management of gas cylinders entering and exiting the filling station and the gas exchange station, and the industrial gas company can know the production and sales status of the gas at any time
Statistics and certification of internal gas cylinders of industrial gas companies to prevent confusion or loss, dynamic statistics and analysis of inventory cylinders and spare parts
The circulation of gas cylinders that have not passed the safety inspection can be restricted to ensure the safety of people’s lives and property.
It can confirm and manage the daily work of the industrial gas company, such as hazard source inspections, and the presence of personnel on duty.
Technical basis of the project
RFID (Radio Frequency ID) is a “radio frequency identification” technology, which is a non-contact automatic identification technology. The basic principle is to use radio frequency signals and their spatial coupling and transmission characteristics to realize automatic identification of stationary or moving objects to be identified, and to obtain related data for identification, statistics, and processing by the back-end system. At present, the frequency used by RFID spans multiple frequency bands such as low frequency (LF), high frequency (HF), ultra high frequency (UHF), and microwave.
RFID is an easy-to-control, simple, practical, and flexible application technology. Its unique advantages are beyond the reach of other identification technologies such as barcodes, magnetic cards, and IC cards. It can support both read-only work mode and read-write work mode without contact or aiming; reading can be completed in the moving process; supporting simultaneous reading and distributed data collection; storing information can be changed freely; working freely in each Under a harsh environment; a high degree of data integration can be carried out. In addition, because the technology is difficult to be counterfeited, RFID has a very high security protection capability. This technology can complete information input and processing without manual contact, optical visualization, and manual intervention, and the operation is fast and convenient.
RFID technology has matured and has been widely used worldwide. Typical application areas include: automatic identification and management of railway car number; automatic toll management of vehicle and road traffic; automatic identification and management of air storage containers; automatic identification, sorting, and transfer management of passenger air parcels; automatic control of product processing on production lines (Mainly used in the automated assembly line of large factories) and the automated management of logistics and warehousing, etc.
The variety of RFID products is abundant, the cost is continuously reduced, and the scale application industry is expanding. RFID technology developed earlier and faster abroad. There are more mature and advanced RFID systems in Europe, America and Japan. my country’s research on RFID technology has also developed rapidly, and market cultivation has begun to bear fruit.
RFID technology is relatively mature and has a good application foundation. The industrial gas cylinder and retail safety management system using RFID technology is safer, anti-counterfeiting, equipment easier to track and not lost, more efficient in operation, and more transparent and visible in management than traditional management methods. Some applications have been adopted by developed countries.
The overall design idea of the project
The basic goal of the gas cylinder and retail safety management system is to use advanced RFID technology to realize the full-range management of the filling and circulation process of gas cylinders. A special-shaped logo is fixedly installed on each cylinder of the gas company through a dedicated method. Electronic tags for life-time identification of gas cylinders. This system covers not only the management of gas cylinders entering and leaving filling stations, gas exchange stations, and distribution links, but also the status and behavior of each process in the filling and testing process of gas cylinders. Take control to ensure the safety of gas cylinder circulation, eliminate hidden dangers of accidents, maintain the personal and property safety of enterprise employees, and prevent illegal users from making illegal profits.
In addition, through portal technology and existing monitoring system for application integration.
Due to the application of middleware technology, the management system and the equipment are irrelevant. The system can easily replace the RFID electronic tags with barcodes, and the selected equipment supports the identification of RFID tags and barcodes at the same time.
The main content of the construction
1.Safety standards, testing standards, and application standards formulation
2. A data management center (platform system)
3. RFID middleware system development
4.Deployment and information collection system of various business nodes and terminal systems
5. Application integration with existing video surveillance systems.
RFID security logo
Identification of industrial gas cylinders
The only corresponding to the identification electronic tag of the industrial gas cylinder is a group of data information closely related to the gas cylinder. The label can be flexibly installed during installation, so that it can be removed and reinstalled during detection. The data in the label is stored through encryption, so the reinstalled label can be guaranteed to be the label of the system.
Relevant enterprise operators can create files, edit and maintain this information through the system software. All operators and management personnel involved in the filling and circulation of gas cylinders can inquire part or all of the information through tag reading and writing equipment or management software according to their authority.
User identification and management
All users in the system are issued with readable and writable electronic tag user cards as the basis for identification and transaction. All users must first go to the company to go through the relevant procedures, receive the card and recharge. The delivery personnel send air to the door, confirm and deduct the corresponding amount of the user card through the tag handheld reading and writing device, and correspond the bottle number to it; or in the industrial gas station, the user can collect and return the gas bottle with the card, and the reading and writing device automatically judges the user card Whether it is legal and whether the number of gas cylinders on the card meets the requirements. When the conditions are met, the device automatically modifies the relevant information in the card, and the transaction data is immediately reported to the central management system.
Identification and management of operation personnel
Operators involved in system operations can be divided into the following categories:
1.Industrial gas station receiving and dispatching managers
2.Incoming management staff of filling station
3.Cylinder inspector
4.Cylinder filling personnel
5.Cylinder in and out management personnel
6.Equipment inspection personnel
7.System Information Manager
8.Decision-making or business management personnel
9.System management and maintenance personnel
For 1 to 6 types of personnel, the system will issue a unique user card for each employee, and the system will automatically determine its legality and authority when performing operations, and control its operations. After each operation is completed, the reading and writing device will report its identification code and operation information to the central management system of the system. So as to achieve real-time tracking and inspection of all personnel operations. For the 7th to 9th types of users, the system directly checks the identity and authority through the user name and user password.
The overall structure of the RFID industrial gas cylinder safety management system
Introduction to the process of filling and circulation of gas cylinders
The schematic diagram of the gas cylinder filling and circulation process under the management of the gas cylinder safety management system is shown in the figure below.
Schematic diagram of gas cylinder filling and circulation process of gas cylinder safety management system
When the user returns the bottle, the handheld device determines whether the gas cylinder is a legal gas cylinder. Under no abnormal conditions, modify the current circulation status of gas cylinders to “at gas station”. Then send it to the filling station. The operator in charge of entering the filling station uses a handheld device to register the received gas cylinder into the station. If there is a problem with the gas cylinder, the handheld device will start an alarm through text and sound, and the operator is asked to send the gas cylinder to the bottle inspection program. After the operator confirms, the cylinder is automatically set to the state to be inspected. In addition, if the incoming operator considers it necessary to inspect the steel cylinder based on actual judgment, the inspection can also be completed through the handheld device, and the steel cylinder will also be changed to a pending inspection state. If the cylinder enters the state to be inspected, the cylinder will be locked by the system before the registration of the inspection result is completed and the conclusion is qualified. If the steel cylinder is found at any link other than the bottle inspection, the handheld device will alarm and require the operator to deal with it. Cylinders that pass the bottle inspection and do not require bottle inspection can enter the filling process. For the sake of safety, the operator shall check and register with the handheld device again before filling to eliminate the steel cylinders that have entered the process due to the negligence of the previous operations. After the filling is completed, the operator uses the handheld device to register the filling result. If a problem is found, an alarm will be issued. When the filling weight does not meet the specified error requirements, it must be sent back to the filling process. The filled steel cylinders are then sent to the designated warehouse, and the warehouse management personnel use the handheld device for warehousing registration. The outbound registration is carried out before the cylinders are sent to the industrial gas station. Then, when the user provides a valid user card and the number of gas cylinders that can be collected meets the conditions, the user can withdraw the gas cylinders, and the handheld device is responsible for determining the user’s identity and registering the bottles.
User ventilation process
Uniformly replace the industrial gas supply certificate printed with RFID electronic tags or bar codes, and do a good job of registration, so that the industrial gas company can keep abreast of the user’s usage.
The user’s industrial gas supply certificate includes a ventilation ticket with an RFID electronic tag or bar code identification, which is scanned during a gas exchange and collected and managed by the industrial gas station staff to provide a basis for reimbursement with the industrial gas company.
When the user is ventilating, the staff of the supply station first scans the RFID electronic tag or bar code of the supply certificate with a handheld device to confirm the user’s identity.
Scan the empty bottles brought by users, dynamically add them to the database, record the empty bottles in storage, and then perform ventilation.
After the user’s changed industrial gas is scanned, it is also dynamically added to the library, so that the database has a record of the daily out of the library.
If the ventilation interval of a ventilation voucher is less than the set number of days, the system will automatically prompt and send out an alarm message to notify the staff to refuse to ventilate for it; at the same time, it also avoids the phenomenon of personal fraud by the staff of the industrial gas station.
Inspection process flow
The detection station mainly includes incineration, pressure measurement, leak detection, shot blasting, painting, etc. The high temperature of the incinerator will damage the label. In order to ensure the uniqueness of the gas cylinder information, remove the gas cylinder label before incineration. Each bottle is attached with an iron clip logo, so that the entire information chain is connected, and the label of the gas bottle is reinstalled, no matter how to ensure the uniqueness of the gas bottle information, and avoid potential safety hazards.
Equipment inspection process
By installing special electronic tags on important equipment, equipment inspection management can be realized, equipment maintenance personnel are urged to conduct regular inspections, and the system automatically records their inspection behavior. If equipment maintenance personnel are found to be dereliction of duty, the system immediately informs relevant management personnel.
From a functional point of view, the system can achieve the following functions:
1. The system has a data management center mainly for production, sales and storage of data, safety production and testing, supply chain data processing, and management of various business systems, and can alert illegal users and equipment. Use Portal technology to integrate the RFID system with the original video surveillance system. Achieve unified display.
2. Perform dynamic statistics and management of gas cylinders entering and exiting filling stations and ventilation stations. With the support of special software, the handheld device communicates with the server of the industrial gas cylinder safety management system of the industrial gas company in real time. The operator can obtain the current gas according to his authority. Some basic information of the bottle. When there are various problems with the gas bottle, the handheld device will send out an alarm through sound and text, and the operator is required to take necessary treatment. At the same time, the server management software of the industrial gas cylinder logistics safety management system automatically modifies the status of the gas cylinders and registers relevant information at the same time. Basic information such as the entry and exit time of the gas cylinder, the operator and the whereabouts of the gas cylinder.
3.Bottling plant (gas filling station) management
The gas cylinder from the gas exchange station is cleaned, the relevant information on the label on the gas cylinder is read through the RFID read-write device deployed in the cleaning line, and the relevant information is submitted to the production management system to enter the gas filling link; bottle inspection is carried out before filling If there is a problem, enter the inspection link, if it is normal, enter the filling line after passing the inspection; after filling, use RFID equipment to conduct corresponding inspections, and all information in the filling process is submitted to the production line management system, which is carried out by the production line management system Corresponding treatment saves labor and time.
Carry out strict process tracking management for the circulation of gas cylinders in the gas station, and provide basic management processes such as pre-filling management, post-filling management, bottle inspection management, and warehouse entry and exit management. Real-time registration and strict judgment of the dynamic information of the gas cylinders flowing through each link, to prevent unqualified gas cylinders from entering the filling link, filling unqualified gas cylinders into storage and other behaviors that violate the normal circulation safety requirements.
4.Bottling plant warehouse management
The gas cylinders in the warehouse are new bottles produced by the manufacturer and the bottles to be flushed returned by the user have a unique electronic tag to identify their identity and write corresponding information. The gas in the warehouse is read through the RFID read-write device deployed at the entrance. The number of cylinders and determine whether the cylinders are legal. Legal gas cylinders will enter the filling production line. If there is a problem with the gas cylinder, it will be sent to the bottle inspection program, the cylinder will be automatically set to the waiting state, and the gas cylinder will be locked by the system.
The filled steel cylinders are then sent to the warehouse, and the RFID equipment deployed on the production line is put into the warehouse for registration. When leaving the warehouse, use the RFID device to read the number of vehicles loaded, and write the corresponding information (such as delivery information) to load the vehicle, and automatically set the steel cylinder to the state of leaving the warehouse.
5.Distribution cylinder circulation management
Mainly for the management of distribution stations and ventilating stations. As the store sales method gradually becomes a large-scale distribution method and the service deepens, this link will be more on-site for gas delivery in the future.
When the user returns the bottle, the RFID device can determine whether the gas bottle is a legal gas bottle. Under no abnormal conditions, modify the current circulation status of the gas cylinder to “at a ventilation station”. Then send it to the filling station. If there is a problem with the gas cylinder, the equipment starts to alarm and ask the operator to send the gas cylinder to the bottle inspection program. After the operator confirms, the cylinder is automatically set to the state to be inspected. In addition, if the incoming operator considers it necessary to inspect the steel cylinder based on actual judgment, the inspection can also be completed through the handheld device, and the steel cylinder will also be changed to a pending inspection state. If the cylinder enters the state to be inspected, the cylinder will be locked by the system before the registration of the inspection result is completed and the conclusion is qualified. If the steel cylinder is found at any link other than the bottle inspection, the reading and writing equipment will alarm and require the operator to deal with it. Cylinders that pass the bottle inspection and do not require bottle inspection can enter the filling process. The desktop read-write device determines whether the user provides a valid user card and the user can withdraw the gas cylinder when the number of gas cylinders meets the conditions. The entry and exit of gas cylinders will be processed by reading and writing equipment at the exit and entrance, and data will be collected.
If the air is delivered to the door and arrive at the user, the delivery personnel use the RFID handheld device to operate the gas cylinder label and change the information. If the user has used the electronic tag certificate, the delivery person can directly use the handheld device to debit the user card, and the data will be submitted to the data center through wireless means. If the conditions are not met, the delivery person can return to the delivery station or the ventilation station. Upload the data in the handheld device to the data center through the computer.
6.Inspection station management
The detection station mainly includes incineration, pressure measurement, leak detection, shot blasting, painting, etc. The high temperature of the incinerator will cause the damage of the label. The important thing in this link is to ensure the uniqueness of the gas cylinder information. This link can be passed The association of the information chain re-installs the label on the gas cylinder.
7.Equipment inspection
By installing special electronic tags on important equipment, equipment inspection management can be realized, equipment maintenance personnel are urged to conduct regular inspections, and the system automatically records their inspection behavior. If equipment maintenance personnel are found to be dereliction of duty, the system immediately informs relevant management personnel.
8.User card management
Management of ventilation customers through contactless cards. At the same time, it provides supporting functions such as card issuance, recharge, and card replacement.
9.Operator management
The operator’s identity is identified through non-contact cards, and the personnel and their operation behaviors are recorded in detail. When a problem occurs, it can maintain complete traceability to implement safety responsibilities to people.
10. The system provides various report output functions according to actual needs, and can quickly output necessary documents such as gas cylinder outbound orders, warehouse receipts, quality inspection notices, and scrap notices.
11. The system provides a complete combined query function, and the operator can quickly retrieve the data information and historical records of interest from the massive data according to various conditions.
Portal application integration
Portal enterprise portal products solve the problem of integrating various enterprise application systems, data resources and Internet resources into an information management platform under the Internet environment, and can be based on the characteristics and roles of each user. Form a personalized application interface.
Portal is a Web-based system that can provide commercial information to users distributed everywhere, and help users manage, organize, and query information related to enterprises and departments. Internal and external users only need to use the browser to get the data, analysis reports and business decision support information they need.
Portal provides a single entry for enterprises to access various information resources of the enterprise, and organically combines enterprise applications, personnel, information and processes.
Therefore, multi-department collaboration, integration of independent and decentralized information systems, so that the various systems of the enterprise can work together to form a complete and efficient whole is the service provided by the Portal enterprise portal.
Through portal technology, gas cylinder safety management and video surveillance management are combined to achieve unified platform management.
Data communication transmission network scheme
The supply process of the industrial gas company includes the main links of filling, warehouse storage, transportation, sales and circulation, and testing. The work process is strictly implemented, and the above nodes are connected to the data management center through the LAN network equipment; such as the distance data of the distribution station or the ventilation station The remote link of the center uses ADSL/ISDN to exchange data with the data center through a private network or VPN; wireless technology is used to send the data collected by the handheld device of the distribution terminal to the data management center to achieve process control and strengthen the management of industrial gas supply , It can conduct patrol inspections on the hidden dangers of each link at the same time, and report the safety inspection results at any time.
The communication among the internal database server, communication server and management terminals of the data center system is entirely based on the existing computer network of the enterprise.
Extended optional functions
Filling weight collection and control module: This module can directly detect the filling weight of the gas cylinder and automatically control the filling process. For companies that have not realized automatic control at all, a full set of filling control solutions can be provided and seamlessly integrated with the safety management system. For companies that already have a certain automation foundation, they can provide interface solutions to ensure the dynamic exchange of information between the two systems. Under normal circumstances, the module needs to be customized according to the user’s actual workstation and site conditions.
Summarize
Because gas cylinders have electronic tags, the uniqueness of gas cylinder information is guaranteed, the safety and anti-counterfeiting supervision of LPG cylinders are strengthened, and cylinders are filed, fixed-point filling, and regular inspections are implemented.
Through the control of each link, through the real-time collection of gas cylinder status information, the status and flow direction of the gas cylinder can be tracked, and the loss of property can be avoided.
Through the deployment of RFID in various links, especially filling, warehousing, and distribution, efficiency has been improved.
1. The data center system adopts large-scale database technology, network technology, and distributed computing technology to establish a central database and various business systems.
2. Use middleware technology to realize the intermediary role between hardware and application programs, and operate various RFID devices and software more smoothly. The framework includes two parts: RFID edgeware and RFID integrated middleware.
3.The deployment and information collection of each node terminal system are deployed using RFID technology
4. Apply RFID technology to establish a monitoring and control system for the entire process of filling, testing, distribution, and circulation of industrial gas cylinders. During the establishment of the entire system, industrial gas companies, equipment and system development suppliers, filling plants, testing stations, distribution or gas exchange stations jointly participated to complete the entire process of automatic information transmission.
5. Use the results of this project as the basis for the establishment of industry standards, promote it in the industrial gas retail industry through the promotion of the government, and strive to participate in the government’s standard establishment work in this industry.
RFID electronic label or barcode
It is affixed to the handle of each industrial gas cylinder. The serial number is written according to the requirements of the industrial gas company. It can represent the cylinder type, inspection date, owner, company’s internal fixed production serial number, service life, etc., and is one by one with the background data management system correspond.
RFID electronic label or barcode printer and electronic label or barcode generation software
It is used to generate serial numbers and print barcodes according to the management requirements of industrial gas companies, or print them on electronic labels.
Note: Due to problems such as transportation and wear of industrial gas cylinders, metal RFID electronic tags or special materials can be used to customize labels with barcodes for industrial gas companies to enhance the service life of the barcodes.
Handheld devices
Wireless handset:
32-bit microprocessor, main frequency: 20MHz;
Real Time Clock
SAM card interface (reserved): a smart card supporting ISO7816 standard T0/T1 protocol.
SIM card interface: SIM card standard supporting GPRS module
Memory
FLASH memory 2 MB (standard configuration), can be expanded to 8 MB without changing the line
RAM memory 2 MB
LCD display with backlight
Meet the requirements that can be used during the day and night;
FSTN, 128*128 dot matrix;
Working temperature: -20 degrees to 70 degrees;
Storage temperature: -30 degrees to 80 degrees;
Buttons (28 buttons in total)
Direction keys 4 confirm key 1 (2 keys 1 function)
8 function keys (including 1 switch key 1 shift key)
Scan key 2 communication key 1
10 number keys
Electronic label identification module
EM module (optional)
Ti module (optional)
RF card interface (optional)
Barcode recognition module
Support one-dimensional barcode
Communication Interface
Standard infrared interface;
Standard RS-232 interface;
Wireless micro power wireless module (optional);
GPRS/CDMA communication interface: (optional);
Standby time
More than 7 days; provide power-saving protection; automatically shut down the POS machine if it is not used within the set time.
Accessories
Rechargeable lithium battery: 1700mAh.
Dedicated charger: PC USB port, or direct 5VDC adapter.
Serial communication line
Charging base
Support user secondary development
Programming language: standard C language
Function support:
Display keyboard communication FLASH storage clock buzzer contactless card wireless module GPRS module function, etc.
Support database search
Detailed programming instructions, example programs, etc.
It has its own compilation system and download program, and supports Windows 2000/windows XP operating system.
Dimensions
175mm*68mm*40mm
weight
Drop test: 1.2 meters drop;
It has the functions of moisture-proof, dust-proof, anti-vibration, anti-fall and anti-electromagnetic wave.
Micropower wireless communication module
Features:
Small size, suitable for embedded installation;
Low price, suitable for low-cost engineering applications;
Adopt very large scale integrated circuit, low power consumption design, SMT production process;
Industrial grade product design, temperature range -30℃~65℃;
The transmission distance is 200 meters.
Overall technical indicators:
Frequency stability: 5ppm
Data interface: RS-232, 485, TTL (customer choice)
Interface rate: 11.92k/1200bps (customer choice)
Power supply voltage: DC 5V
Power consumption: <0.2A when transmitting at full power
Volume: length × width × height = 85mm × 45 mm × 20 mm
Launch index:
Output power: 10mW
Launch time: ≤30ms
Industrial Gas Safety and Retail Management System (software)
1.Database Center Management System
Installed in the management center of the industrial gas company, the SQL database stores, counts, and manages all cylinder information, and customizes various management functions according to the requirements of the industrial gas company. The management center and the industrial gas station can be connected via computer (dial-up or ADSL), or wireless (GPRS or CDMA1X) via handheld.
composition:
Portal management system
Web server
Monitoring center database
Production Information Center
Production control center
2.Subsystems
Cylinder label management
User tag management
Operator tag management
Authentication and information storage for entering and leaving the filling station
Identity management for entering and leaving the filling station
Filling quantity statistics management
Warehouse management
Inspection management
Equipment basic information management
Security hazard inspection management
Gas cylinder safety verification management
Electronic inspection function
Data communication
The data collection terminal can be used as a communication terminal to realize remote control of production and operation activities
The terminal can also realize functions such as positioning, calling, and text messaging
Middleware system
This system middleware is a message-oriented middleware (Message-Oriented Middleware, MOM). Information (Information) is transmitted from one program to another or more programs in the form of messages. Information can be transmitted in an asynchronous manner, so the transmitter does not have to wait for a response. The function of message-oriented middleware is not only to pass information, but also to interpret data, security, data broadcasting, error recovery, locate network resources, find a cost-compliant path, prioritize messages and requirements, and Services such as extended debugging tools.
Milestones
Preliminary preparation stage of the first phase of the project:
1.Complete project feasibility analysis
2.Selection of demonstration project sites, field inspection needs
3.Determine the technical partner, determine the solution
4. Determine the equipment installation plan and testing indicators, and complete the equipment selection.
second stage
1.Complete the detection methods and data standards of each indicator
2. Establish a database system;
3.Complete the platform construction of the information management center
4.Complete the prototype of the system
5.Complete the demonstration and debugging of the equipment
The third phase
1.Complete equipment purchase, on-site installation and commissioning
2. Carry out system modification and complete system trial operation;
The fourth phase of the project trial operation stage:
1. Perfect standards;
2. Through the accumulation of information in the database, make preparations for the promotion of project technology.
If you have any questions, please contact
Document production: Ren Gong
Email: [email protected]
QQ: 479017087
Mobile: 13911533725
http://company.rfidworld.com.cn/rfidworld_company_27961.html
[ad_2]