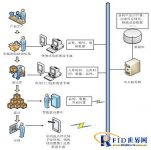
Warehouse management system solution based on RFID technology
[ad_1]
1 Difficulties in warehousing logistics management
At present, market competition is becoming increasingly fierce, and improving production efficiency and reducing operating costs are of vital importance to enterprises. Warehousing logistics management is widely used in various industries, designing and establishing a complete set of warehousing management processes, improving warehousing turnover efficiency, reducing the occupation of operating funds, turning frozen assets into cash, reducing the cost caused by warehousing elimination, and improving the company An important part of production efficiency.
Warehouse management systems usually use barcode labels or manual warehouse management documents to support their own warehouse management. These management methods have obvious disadvantages:
Barcode management, easy to copy, non-fouling, non-moisture-proof, and can only be read at close range and visible range;
Manual entry, cumbersome work, large amount of data and error-prone, increase labor costs in warehousing;
The workload of manual inventory is large, resulting in a long inventory cycle, and missing goods or theft cannot be discovered in time.
2 system framework
RFID is a non-contact automatic identification technology realized by radio frequency communication. RFID tags are small in size, large in capacity, long in life, and reusable. They can support fast reading and writing, multi-eye identification reading, non-visual identification, mobile identification, positioning and long-term tracking management.
In recent years, RFID technology has entered the stage of commercial application. At present, RFID technology has been continuously combined with Internet and communication technologies, and has been applied to many fields such as industrial automation, commercial automation, transportation, logistics, supply chain management, public information services, etc., gradually realizing global item tracking and information sharing, Significantly improve management and operation efficiency and reduce costs. RFID technology is considered to be one of the most promising information technologies in the 21st century.
The purpose of the design of the warehouse management system based on RFID technology is to realize the automation of the goods out/in control, the storage location and quantity statistics of the goods, and the information inquiry process, so as to facilitate the management personnel to carry out statistics, inquiries and grasp the flow of materials, so as to achieve convenient, fast, Safety, high efficiency and other requirements.
3 system composition
The RFID system is composed of three elements: “RFID Tag”, “Reader (antenna + controller)”, and “PC and other advanced equipment”. The “RFID Tag” is composed of an IC chip and an antenna that can store a large amount of data. According to the instructions of “PC and other advanced equipment”, the data stored in the RFID chip can be read or erased by the “reader”.
3.1 RFID electronic tags
Built-in global unique ID, and has 96bit/240Bit space to store user-customized information; waterproof and oil-proof; long service life; long reading distance, tag data can be encrypted, and information is tamper-proof; tags can be erased and recyclable.
3.2 Long-distance reader
The serial port is used to communicate with the computer; the RFID tag reads the cargo information in a non-contact manner, with an accuracy rate of 98%. Read and write distance can reach 8m, working frequency: 900MHz, in line with EPC global Gen2 ISO18000-6C standard, in line with FCC regulations; reliable reading performance, can work in a dense reader environment; tag data rate up to 640Kbps, read per second 1000 tags; signal receiving sensitivity -80dB; mainly used for aviation, highway, fashion, medicine, asset management, anti-counterfeiting, retail, etc.
3.3 Portable short-distance reader
Support protocol standards: ISO18000-6B, EPC Class 1, EPC Class 1 GEN 2; maximum RF output power: 30 dBm; identification card time: single card identification is less than 8ms; read/write card time: read every 8 bytes less than 5ms, Write every 4 bytes less than 25ms; Communication interface: Type B: RS-232, RS485, Wiegand26/34, USB; Working status prompt: buzzer, communication indicator, power indicator, card reading indicator.
3.4 Smart car inventory
It can take inventory of pallets and high-level shelves. It can work continuously for 8 hours on a single charge. It can synchronize with system data via Wi-Fi or GPRS. The reading and writing distance can reach 8m. Working frequency: 900MHz, in line with EPC global Gen2 ISO18000-6C standard, in line with FCC regulations, large reading range and high accuracy.
3.5 Optional equipment
Label printer, cargo location and cargo search touch screen, alarm light, handheld reader
Hand-held reading of RFID tag information can display product information. The reading distance is 1-2 meters, which can realize inventory shift, query, and inventory in the distribution store. Data can be exchanged with the system in real time via WiFi and GPRS networks.
3.6 Management software
3.6.1 Inbound and outbound management software
The data collected by the reader is processed, and it can be connected with the user’s existing application system; at the same time, it can provide customized development of the application system according to the actual needs of the user.
3.6.2 Two-dimensional electronic cargo location management software
Tracking cargo location information, cargo storage location, convenient for cargo location preparation when entering the warehouse, quick search out of the warehouse, ensuring advanced selection, avoiding inventory waste and expiration, and improving warehouse utilization. At the same time, it provides customized development of application systems according to the actual needs of users.
4 system implementation
4.1 Storage
In the finished product packaging workshop, workers first affix RFID electronic tags to the products, and then affix the box label after packing in batches. Those who need to be palletized can also affix the pallet label after the pallet is finished; the general labeling methods are:
Single product labeling
Multiple products are packed together, and the outer packaging is labeled
Pallet labeling and association with single product label or outer packaging label data
The packaged products are put into the warehouse by the loading and unloading tools through the channel composed of RFID readers and antennas. The RFID equipment automatically obtains the warehoused quantity and records it in the system. If there is a pallet label, the information of each pallet is written by the import port reader. Pallet labels, at the same time, form the order data association, and then calculate the location through the computer warehouse management information system (or manually specify the location for the batch at the beginning).
4.2 Delivery
The consignor of the logistics department generates an outbound order according to the invoice required by the sales: that is, according to the outbound priority (for example, the first out of the warehouse before the production date) to query the warehouse for the storage location and inventory status of the outbound goods, if there are customers The designated batch number will be queried according to the designated batch number, and the outbound cargo pick-up position and the corresponding pallet belonging to the goods will be generated.
The consignee brings the outbound order to the warehouse manager, and the warehouse manager checks the information to arrange for the forklift driver to carry out the corresponding product out of the warehouse.
The forklift picks up the goods and passes through the exit gate. The exit gate RFID reader reads the pallet label on the pallet to obtain the outbound information, and verifies whether the product batch number and location listed in the shipped product and the outbound order are correct.
After the delivery is completed, the warehousing terminal prompts the delivery details for the administrator to confirm, and automatically updates the data to the database.
4.3 Inventory
Warehouse management personnel use smart inventory trucks and push them on each shelf or pallet. The inventory truck can read the quantity and type of goods on the shelf or pallet and accumulate them. After the inventory is completed, an inventory report will be generated and provided in the system. The data information is compared with the actual inventory quantity in the warehouse for reference by warehouse management personnel. At the same time, the data information in the system can be modified as needed to ensure that the goods and accounts are consistent.
5 System performance
Labor can be reduced by 20-30%;
99% of warehouse products are visualized, reducing the risk of missing goods;
Improved supply chain management will reduce work service time by 20-25%;
Improve the accuracy and reliability of storage information;
Efficient and accurate data collection provides operational efficiency;
Automatic collection of incoming and outgoing data to reduce human error;
Reduce enterprise warehousing logistics costs.
[ad_2]