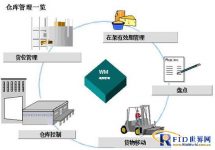
Warehousing logistics automation system scheme based on bar code technology
[ad_1]
Industry Status
In order to achieve effective customer service, companies must have the ability to quickly respond to their customers’ special business needs. In order to reduce inventory and increase the fulfillment rate of orders, it is particularly important to adopt selective delivery channels. Due to the influence of geography and other factors, direct shipment from the supplier of the enterprise to the customer is a common way of operating business. In addition, we must also pay attention to optimizing inventory and equipment. The utilization of various resources and space, so as to achieve some management of logistics operations.
The most common technical topic in warehouses today is barcode, accompanied by data storage, transmission, intelligent software, computer platforms, and communication networks. Regardless of where the logistics flows, we can automatically record the flow of logistics. The combination of barcode technology and information processing technology helps us use warehouse space reasonably and in some ways, and provide customers with the most information in a fast, correct, and low-cost manner. good service.
System introduction diagram
Summary of WM functions
Cargo position management: provide detailed control and management to every position;
Warehouse control: according to the pre-defined warehouse access control rules, realize scientific warehouse access;
Goods movement: support various warehouse and special procedures;
Inventory: support for dynamic pin inventory and cycle inventory for positions;
On-shelf validity management: For commodities with shelf life requirements, shelf life control and management can be carried out.
Typical industry users
Fujifilm Corporation-Wireless Scanning System in SAP WM Environment
Implemented the SAP WM+RF barcode system for the Fujifilm Logistics Center, which greatly improved the efficiency and accuracy of its warehouse. After using this set of solutions, the efficiency of warehouse utilization has been greatly improved, and the accuracy of warehouse entry and exit has reached 99.94%, making warehouse inventory extremely easy.
Hecheng Sanitary Ware (China) Co., Ltd.
Implemented the SAP RF SAP console barcode system for the warehouse management department of Hecheng Sanitary Ware, which greatly improved the efficiency and accuracy of its warehouse. After using this set of solutions, the efficiency and accuracy of warehouse management have been greatly improved, and the accuracy of in and out of the warehouse has reached 100%, and warehouse inventory has become extremely easy.
solution
Print label, print method and content reference
Using centralized printing, call the corresponding content from the production order system one day in advance to print the relevant content labels,
Paste method
A product comes off the production line, after being tested, the pre-printed label is affixed to the product and the packaging box.
Goods produced by the B-factory are sent to the temporary storage area of the warehouse
How to print labels
A It is recommended to double-row, and the side-by-side label content format is consistent, so that it can be easily pasted to the product and the content of the box is unified. Save investment, easy to print and paste.
Labels of products B and small boxes are printed with a 104MM width printer, and large boxes are printed with a width of 168MM to print labels with a width of about 160MM. Two columns of the same content are printed and attached to the two corners of the box to facilitate scanning. Both corners have barcodes. Can be scanned. At the same time, the wide format printer can also be used as a backup for the 104 narrow format printer.
Use code128 code, the content of the bar code includes: production time, serial number, product model, and the bar code is unique to facilitate future product inventory tracking and system expansion
Pallet label printing can be considered for future system expansion, this project will not be considered for the time being
Packing area scan
It is recommended to use a wireless barcode scanner to facilitate on-site work and avoid cable interference. At the same time, only a PC workstation is required to complete the input. The network structure diagram is as follows:
The number of scanning guns is configured according to specific requirements to facilitate the scanning and input of packaging points
The wireless scanning access device is connected to the PC by keyboard or serial port to facilitate the system to receive data
The wireless scanner has a two-way feedback function, which can simply determine whether the scanned data is accurate, such as scanning the barcode on the trademark to be packed. First judge whether there is a repetition with the previous one. If there is a repetition, use the light and sound to warn the manual processing; if there is no repetition, it will be automatically stored in the system database.
Packing requires that the products in the same box are exactly the same. If any inconsistency is found, an alarm will be issued
Product warehousing scan
The equipment adopts batch processing barcode scanning terminal, and transmits data regularly through batch scanning
The terminal system recommends the DOS operating system to avoid unnecessary trouble caused by WinCE in practical applications in the simplest and most practical way; upload data to the system in txt format, and then hand it over to the background for processing
Before entering the warehouse, the terminal should download the corresponding data content from the PC for comparison during scanning
After the whole box of products with barcode labels are delivered to the warehouse, the warehouse manager scans the packing list with the batch terminal and compares it with the data on the terminal. If it is OK, it will be stored in the warehouse. If there is a problem, it will be taken Corresponding measures
Outbound scan
Use the same batch terminal
Before leaving the library, download the contents of the same day to facilitate comparison
When the product arrives in the outbound temporary storage area, the custodian will scan the barcode of the packing box, enter the information and get the comparison, confirm the outbound, if there is an error, take corresponding measures
inventory check
Warehouse management uses scanners to scan the boxes of products in the warehouse. For each box scanned, the system automatically verifies the information in the database, and if it is correct, it passes; if a problem is found, it manually enters the terminal to the final terminal The data shall prevail, then upload it to the PC and update the database.
Return goods into storage, internal use out of storage, etc.
The warehouse clerk’s processing method and data transmission method are the same as that of new products in and out of the warehouse, but the return or requisition menu can be made on the terminal interface, which can be used for reference
[ad_2]