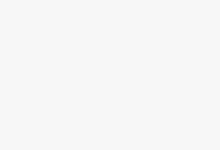
Wide application of warehousing logistics management in various industries
[ad_1]
1. RFID Warehouse Management Information System
At present, market competition is becoming increasingly fierce. How to improve production efficiency and reduce operating costs is of utmost importance to enterprises. Warehousing logistics management is widely used in various industries, designing and establishing a complete set of warehousing management processes, improving warehousing turnover rate, reducing the occupation of operating funds, turning frozen assets into cash, reducing the cost caused by warehousing elimination, and improving the company An important part of production efficiency.
Warehouse management systems usually use barcode labels or manual warehouse management documents. These management methods have obvious disadvantages:
Barcode management: easy to copy, not stain-proof, not moisture-proof, and can only be read at close range. Manual entry: cumbersome work, large amount of data, easy to make mistakes and omissions, and increase labor costs in the warehousing link. The workload of manual inventory is large, resulting in a long inventory cycle, missing or stolen pallets, and it is not possible to discover in time. RFID technology is bringing a huge change to the supply chain field. The identification distance is long, fast, not easy to damage, and bar codes such as large capacity are incomparable. The advantage of simplifies the complicated work process and effectively improves the efficiency and transparency of the supply chain. The RFID warehouse management system introduces RFID technology into the existing warehouse management, and automatically collects the data of each operation link such as warehouse arrival inspection, warehousing, outgoing, allocation, warehouse shifting, inventory counting, etc., to ensure The speed and accuracy of data input in each link of the warehouse management ensure that the company can accurately grasp the real data of the inventory in a timely and accurate manner, and reasonably maintain and control the company’s inventory. Through scientific coding, it is also convenient to manage the batch and shelf life of items. Using the system’s location management function, you can also grasp the current location of all inventory materials in a timely manner, which is conducive to improving production efficiency and reducing operating costs, which is very important for enterprises. With the application of RFID technology, electronic tags are sealed into a card shape and attached to the packaging or tray of each pallet, and the specific information of the pallet, storage location and other information are written in the label. At the same time, the detailed information of the delivery party can be written when the pallet enters and exits the warehouse, and fixed or portable card readers are installed in the warehouse and various distribution channels to identify and detect the circulation of pallets. The RFID warehouse management system is composed of business management software, RFID tag issuance system and RFID tag identification collection system. These systems are connected to each other to jointly complete the various processes of item management. The back-end database management system is the core of the whole system, and RFID identification collection is the basis and means to realize the management function. The background management software is composed of a central data server and a management terminal, and is the data center of the system. Responsible for communicating with the handheld, converting and inserting the data uploaded by the handheld into the database of the back-end business warehouse management system, and centrally storing and processing label management information, issuing labels and collected label information.
The RFID label issuance system consists of a special printer for electronic labels and label production management software, which is responsible for completing the information writing of location labels, item labels, and box labels and printing of label surface information. The electronic label special printer adopts an industrial-grade thermal transfer printer with a built-in non-contact reader, which can print pre-set content information on the label surface while writing information on the label chip. The core of the label production management software is the label production function dynamic link library, which is embedded in the back-end system to provide the back-end storage management system with the development interface function for operating the printer to make labels. Based on the dynamic library, an independent label making software is also provided, which can manually input label data to facilitate temporary label making. The RFID tag identification collection system can collect tag information through a handheld or a fixed-position terminal, complete the storage of tag data, and exchange data with the management center through RFID middleware.
The introduction of RFID radio frequency technology has made enterprise warehouse management more transparent and more efficient. Encapsulate the electronic label in a barcode label, stick it on the packaging or tray of each tray, and write the specific information of the tray, storage location and other information in the label. At the same time, the detailed information of the delivery party can be written when the pallet enters and exits the warehouse, and fixed or hand-held readers are installed in the warehouse and various distribution channels to identify and monitor the circulation of the pallets. The main advantages are:
RFID warehouse management information system labor can be reduced by 20-30%; 99% of warehouse products are visualized, reducing the risk of missing goods; improved supply chain management will reduce work and service time by 20-25%; improve the accuracy of storage information and Reliability; Efficient and accurate data collection to provide operational efficiency; Automatic collection of incoming and outgoing data, reducing human error; reducing enterprise warehousing and logistics costs. Today, with the rapid development of logistics automation technology, with the help of RFID fast scanning, barrier-free reading and other features, data collection and processing can be carried out quickly and accurately to achieve standardization and efficient operation of warehouses. Realize quick check and find goods, intuitive storage, scientific and reasonable. Through modern advanced network technology, real-time sharing of warehouse management information such as inbound, outbound, and inventory is realized in the course of enterprise operations. It is convenient for the company to supervise the pallets; it is convenient for the warehouse to put in, out, count, and pick the pallets; it is convenient for the company to understand the situation of the company’s pallets in the warehouse.
(1) Document scope
1. Comprehensive introduction
2. Functional requirements
3. Non-functional requirements
(2) Document readers
This document is mainly aimed at: project implementers, project managers, developers, testers or document writers. This document is a reference document for technical implementation projects, an informal implementation plan, and the final implementation plan is subject to the contract attachment.
(3) Explanation of key terms and abbreviations
1. RFID: (Radio Frequency Identification) radio frequency identification;
2. B/S architecture: (Browser/Server) browser/server architecture. 【Tentative】
2. Comprehensive introduction
(1) System function introduction
Figure 1 Overall functional framework diagram
The functions of the warehouse management system are shown in the figure above. It mainly includes six functional modules: daily management, warehousing management, query management, shifting management, outgoing management, and printing management.
(2) Analysis of system investment benefits
1. Warehouse entry and exit eliminate the tedious work of scanning one by one, and the speed has been greatly improved.
2. The bar code label on the cargo space is difficult to visualize in the warehouse, and the forklift driver is easy to put the cargo space in the wrong place. The wireless PC and reader on the forklift can ensure that the target cargo position on the shelf is correct.
3. The forklift interacts with the host through a wireless PC, and can grasp the position and status of each forklift in real time. The forklift scheduling can be more flexible and the utilization rate of the forklift can be maximized.
4. The forklift driver receives the warehouse instructions and the shortest path guidance through the wireless PC, which can put the pallets on the shelf and pick the goods out of the warehouse faster and more accurately, which can shorten the forklift driver’s working time in the warehouse.
5. When the pallet cannot be placed on the target cargo location due to various reasons, the forklift driver can put the pallet in other cargo locations. By reading the cargo location label association and wireless PC interaction with the host, the real-time accuracy of inventory information can be ensured. Avoid the original cumbersome process when the target cargo space cannot be placed, and the inventory is inaccurate due to the busy work of the forklift driver and the failure to record the target cargo space.
6. Major losses that may result in shipment errors.
7. When the pallet storage pallet is not specified by the system, but the forklift truck determines the storage location of the pallet, the real-time storage information can be submitted to the host system through the RFID forklift, which is compared with the manual recording of the traditional solution and then entered into the computer solution. The real-time and accuracy of inventory have been greatly improved, and the efficiency has also been greatly improved. In traditional warehouse inventory, each box of pallets needs to be scanned at close range. The use of RFID technology will greatly simplify the above procedures. The results of the inventory can be transmitted to the system through the wireless network for recording, eliminating the need for manual entry.
(3) Role function division
Daily management, warehousing management, query management, relocation management, outbound management, printing system administrators, management clerk warehousing operations, query management, relocation operations, outbound operations, printing
(4) Restrictions on design and implementation
The system needs to be used as a subsidiary subsystem of the company’s existing ERP system, and is connected to the OA office system.
(5) Business process introduction
Figure 2 The overall operation process of the finished product library
1. Detailed description of the process:
① Arrange according to customer pallet requirements;
②The warehousing pallets are sorted, picked and packaged according to the needs of customers; (packaged
Two kinds of mixed installation and complete installation, according to the needs of customers)
③The packaged finished products are stacked on pallets with RFID (the pallet information is written into the RFID through the RFID terminal), and transported by a manual trailer or forklift for warehousing operations;
④When the warehouse is in the warehouse, the reader installed at the warehouse will read the RFID information and read
Take the tray information and transfer it to the management system database;
⑤By querying the warehouse information management system, printing the warehousing list to determine the pallet storage area;
⑥The forklift combines the handling operations to carry out the shelf operation, that is, the pallet is placed in the designated cargo position, and the recorded information is transmitted to the management system database through the transmission device;
⑦In-warehouse management and inventory of pallets in the warehouse, the warehouse information system stores all the information of the warehouse pallets, and comprehensively monitors the status of the pallets and the occupancy status of the cargo space;
⑧When the pallet is out of the warehouse, the forklift operator enters the pallet number or pallet information, and queries the cargo position where the pallet is taken to carry out the unloading operation;
⑨The pallets out of the warehouse are shipped and distributed, and finally the customer signs for the pallets, and the warehouse management system
The system records the receipt status of the pallet in real time.
2. Specific procedures for important links such as warehouse entry and exit:
①Warehousing process
The pallets that need to be stored are stacked on pallets with RFID and transported to the warehouse by manual trailers or forklifts for storage; when entering the warehouse, a reader installed at the entrance of the warehouse reads the RFID information and reads the pallet information Incoming to the warehouse management system database; the warehouse management system allocates the cargo space according to the availability of the cargo space, prints the warehousing list, and guides the forklift operator to carry out the shelf operation, that is, the pallet is placed in the designated cargo space.
Figure 3 Finished product warehouse warehousing operation process
②Outbound process
When the pallet is out of the warehouse, the forklift operator enters the pallet number or pallet information to query the location of the pallet to be taken off the shelf; the pallet out of the warehouse is shipped and distributed on the platform; the yellow part indicates the operation process Relevant documents; the red part represents the information flow of the warehouse management system.
Figure 4 Operation process of finished product warehouse outbound
3. Goods location positioning code:
01 A 02 03
Aisle shelf depth
Figure 5 Cargo position code format The goods position code has a total of 6 digits.
The first and second digits represent the passage of the warehouse. The range is 01~07, which respectively represent the 01 to 07 channels of the warehouse, and it is designed to be two digits for easy expansion. The third digit represents the two rows of shelves on both sides of the aisle, range A or B, representing the left and right sides of the aisle respectively. The fourth and fifth digits represent the depth of the warehouse. The range 01-19 represents the depth of the warehouse from 01 to 19, where 01 indicates the position of the shelf closest to the exit aisle, and 19 indicates the position of the shelf closest to the entrance aisle. The sixth place represents the level of the shelf. The value is 1~4, 1 represents shelf 1 layer, 2 represents shelf 2 layer, 3 represents shelf 3 layer, 4 represents shelf 4 layer. There are only 3 and 4 floors of bridge type shelves.
Figure 6 is a schematic diagram of the cargo location code, an example of the code: the second floor cargo location code of the shelf pointed to by the arrow is 03A0702.
Figure 6 The layout design of the three-dimensional warehouse
3. Functional requirements
(1) Pallet information management:
New pallet storage information, including pallet number, storage time, pallet number, color, station number and other information. Delete the tray information, overwrite the tray information, the information can choose whether to print.
(2) User information management:
Create new user information, set user permissions, delete user information, user modify login password, query user information, the information can choose whether to print;
(3) Operator information management:
Create new operator information (including job number, skill level, etc.), set operator authority, delete operator information, query operator information, and choose whether to print the information;
(4) Warehouse management:
①Write the information of the tray into the label through the handheld terminal;
②Inbound port: The reader automatically reads the tag ID, pallet belonging information, and transfers it to the computer host. The warehouse administrator enters the warehouse management function option and enters the receiving interface. The interface displays the tags that have been read but not processed. And the relevant records in the database queried according to the tag ID, showing the ID of all the pallets in the batch and the pallet belonging information. The administrator will check these information with the physical object, and after it is correct, confirm the receipt and enter the warehousing interface;
③Warehousing interface: The host allocates storage locations according to the information of the pallets and displays them in a list on the interface. The list can be printed to guide the forklift operation. After the forklift stores the pallets in the cargo space, the forklift operator displays on the printed job sheet Sign to confirm that the job is complete;
④Record the information (work number) of the operator who has completed the warehousing. The database updates the pallet belonging information and confirms the storage. The warehousing process ends;
(5) Inventory inquiry:
Query real-time database information. The inventory information in the warehouse (including product name, quantity, storage time, operator, estimated time of storage, etc.) can be inquired through query conditions such as the corresponding pallet belonging information, date, etc., and the information can be selected whether to print;
(6) Outbound query:
Query outbound information. By entering the information and date of the tray to query the tray (including the information of the tray) within a certain period of time, the information can be selected whether to print. Query the information of the pallet by entering the pallet number; query the pallet out of the time period by entering the date;
(7) Warehousing query:
Query warehousing information. Query the pallet’s belonging information in a certain period of time by entering the pallet’s belonging information and date. Query the pallet by entering the pallet’s belonging information, and the information can be selected whether to print. Query the belonging information of the pallet in the warehouse during the time period by entering the date;
(8) Inquiry about pallets of dull goods:
Query overdue storage trays. Query overdue storage pallet information (including pallet number, customer code, warehousing time for each pallet number, operator, estimated time of delivery, shipping destination, total warehousing) by entering the length of time in the warehouse. This information can be selected Whether to print;
(9) Outbound management:
Information management of the outbound process. ①The outbound administrator enters the outbound management interface, enters the pallet number on the bill of lading, and obtains the pallet’s status in the warehouse, including the time of entry, the number of pallets in the warehouse, the name of the pallet, the code, the destination, and the storage location. The cargo location information can be printed, and the forklift operator can take out the pallet according to the cargo location information; ②The pallet passes through the warehouse, and the reader automatically reads the tag ID and pallet number. The information system pops up the interface to display the pallet information corresponding to the pallet number, including After checking the quantity, pallet name, storage time, destination, etc., with the physical object, confirm the storage; ③Record the information (work number) of the operator who has completed the storage. The outbound process ends;
(10) Relocation management:
Information management in the process of moving the library. ①The warehouse manager enters the warehouse management interface, enters the pallet number to be moved, and obtains the pallet status of the pallet, including the storage time, the quantity in the warehouse, the pallet name, the destination, the current storage location information, and the current idle Position information; ②Specify the target position to be moved, and print the current position information and the target position information of the warehouse, and hand it to the forklift operator to take out the pallet according to the position information, and then store the pallet in the target position , The forklift operator signs on the printed job sheet to confirm that the job is complete. The database updates the cargo location information and pallet information, and confirms the re-stocking; ③Records the information (work number) of the operator who has completed the move. The library transfer process ends;
(11) Print management:
View and manage all printers in the organization, and print according to the required information input conditions. It is mainly used to print out documents such as warehouse receipt, warehouse receipt, stock receipt, business information and so on.
4. Non-functional requirements
(1) Software and hardware environment requirements
The operating environment of the software required by this system, including the hardware platform, operating system and version, as well as other software components or applications coexisting with them, are shown in Tables 2 and 3:
(2) Software quality requirements
The quality requirements of this system are shown in Table 4 below:
(3) Hardware functional requirements
(1) Main components of the system
1. RFID electronic tags
2. RFID printer (optional)
3. RFID fixed reader
4. RFID handheld reader (optional)
5. RFID forklift reading system
6.RFID channel reading system (optional)
7. RFID middleware
8. RFID warehousing logistics management system
(2) The RFID reader required by this system includes 3 types:
1. Access control system for entry and exit: The reading range of the reader required here is more than 3 meters.
2. Handheld terminal: The required reading and writing distance is about 2 meters
3. Forklift terminal: read and write distance of about 1 meter, read pallets and cargo location tags
(4) RFID-based warehouse management system hardware equipment list
The picture is for reference only. The actual product depends on the final plan
Type parameter description reference picture
Working frequency: 902~928MHz (can be adjusted according to different countries or regions)
Size: 200(length)*218 (width)*48(height)mm
RF power: 20~30dBm adjustable
Communication interface: LAN, RS232, RS485, Wiegand
Communication rate: serial port rate 9600~115200bps, RJ45 is 10Mbps
RFID reader reading distance: adjustable, adjustable output power. With anti-collision detection function, card reading can be controlled by input trigger signal or command.
Protocol: Support EPCglobal C1G2 (ISO18000-6C)
Anti-interference and lightning protection design;
Power consumption: average power <20W
Power supply: equipped with 220V AC input, +12V DC output power converter to meet the requirements of industrial environment;
Application software interface: provide API development kit and VC, VB, Java application routines
Connection connector: N (female)
Gain: 12dBi
Circular polarization antenna frequency: 902-928MHZ
Polarization method: circular polarization
Input impedance: 50 ohm
Size: 405×405×35mm
Connection connector: N (female)
Gain: 12dBi
Vertically polarized antenna frequency: 902-928MHZ
Polarization method: vertical polarization
Input impedance: 50 ohm
Size: 610X310X70mm
Each connecting feeder is 5 meters long
Appearance size: 17.5cm length X 7.6cm width X 2.3cm (3.3cm) height
Liquid crystal display: 3.5″ transflective
Network: WIFI or 3G
RFID handset frequency band: 902~928MHz
Maximum reading distance of 5 meters
(Optional)
Maximum write label distance 2 meters
Battery 3.7V lithium battery, 4400mAh (can be used repeatedly)
Industrial protection standard IP65 waterproof and dustproof
Durability: Drop test on concrete floor at a height of 1.5 meters, can withstand three impacts of three directions, six sides, and three drops
Forklift Reader Protocol: EPCclass1 Gen2, Interface: Bluetooth, Rs232, TCP/IP, Frequency: 902~928MHZ
Antenna quantity: can connect 1-4 SMA port antennas, power supply: rechargeable lithium battery 3.0Ah (18V);
VT-635 is based on the Atom N450 processor, designed for the completion of critical tasks in harsh environments, high-industry
Grade vehicle terminal, built-in WIFI, 3G, Bluetooth and other communication and GPS positioning modules, widely used in warehouse forklifts, container
Real-time dispatching, tracking and positioning of heavy industrial vehicles such as box trucks, mining trucks, farming vehicles, and fire trucks.
● 8.4-inch LED backlit high-brightness touch LCD screen
Forklift truck-mounted tabletIntel Atom N450 1.66GHz low-power and high-performance processor
● Fanless aluminum die-casting shell heat dissipation design
PDA computer ● Comply with IP65 dustproof and waterproof standard
● Support 9-30V wide voltage DC input
● Adapt to -30~60℃ wide temperature environment
● Powerful wireless expansion performance: WiFi, WCDMA/CDMA2000, Bluetooth and other communications and GPS positioning
● VESA standard fixed installation
Size: 84 (length) * 54 (width) * 0.8 (thickness) mm
Material: PCB material
Tray electronic label storage capacity: EPC memory: 240bits
Extended memory: 512bits
Frequency: 860-960 MHz
Size: 244(L)*12(W)*13(H)mm
Material: ABS
Storage capacity of electronic label of cargo location: EPC Memory: 240bits
Extended memory: 512bits
Frequency: 860-960 MHz
Anti-metal tag
5. Project implementation and after-sales service
Composition of construction personnel (Party B):
Project execution flow chart:
[ad_2]