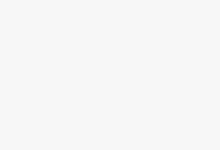
Equipment inspection management solution
[ad_1]
Equipment inspection is to implement relevant management procedures such as the operation and maintenance of enterprise on-site production equipment. The inspection personnel of each post shall complete the inspection operation under the guidance of the system inspection plan. Ensure that the working status and quality of the production site meet the standards, and truly implement the corporate management requirements into the daily work. On the one hand, the requirements of inspections are fed back from the production site of the enterprise. Managers can use the relevant functions of the inspection system and combine the time parameters of the data to better conduct objective statistics and research on the data, and make rapid and accurate data for business leaders. Provide scientific basis for judgment and decision-making. On the other hand, improve the production management level of the enterprise, reduce the cost of equipment maintenance and repair, and extend the service life of the equipment, thereby greatly improving the operating efficiency of the enterprise.
The stable operation of important equipment such as power/communication/production systems is very important, and every failure of the equipment may cause immeasurable losses to the society or enterprises and institutions. Therefore, ensuring the safe operation of equipment assets is the primary task of all units, and equipment inspection is a basic task to effectively ensure the safety of the system. The purpose of the inspection is to grasp the equipment operating status and changes in the surrounding environment, discover facility defects and safety hazards, and take effective measures in time to ensure equipment safety and system stability.
The Weishen Technology Equipment Inspection System is a system that improves the level of equipment maintenance by ensuring the quality of the inspection work and improving the efficiency of the inspection work. The Weishen Technology Equipment Inspection System combines RFID technology to mainly solve the equipment inspection work. There are three important issues in the following: 1. Inadequate inspections, missed inspections, or not on time; 2. Manually filling in inspection results is inefficient, prone to omissions or errors; 3. It is difficult for managers to understand the route in a timely, accurate and comprehensive manner Conditions, it is difficult to formulate the best maintenance and repair plan.
1. System structure
620)this.style.width=620;” border=0>
2. System icon
The inspection terminal is a data collection terminal running Microsoft Windows Mobile, which is equipped with GPS/RFID and wireless communication facilities (GPRS or CDMA). The terminal can communicate with the background management system through wireless communication, combined with the SDIO/CF interface RFID reader, automatically identify the device object, and effectively manage whether the inspection is in place. The background management system provides functions such as task management, facility account management, defect management and analysis, and accepts inspection records and other data from the inspection terminal.
620)this.style.width=620;” border=0>
Three, background management
1. The background management system can manage basic information including facility accounts and team/personnel, and can flexibly customize inspection items, inspection tasks, and defect standard descriptions.
2. The background management system can manage defects. Provide convenient and flexible defect query and processing methods. When users log in to the system with different roles, the system will only list the defects that can be handled by the user in the “Pending” list according to the current personnel’s work authority, and the work is clear at a glance.
3. The back-end management system provides the review function for data modification. For key business data, it needs to be reviewed and verified before modification to ensure the completeness and accuracy of the system data.
4. The background management system can generate statistics, analysis and query reports for historical inspections and defect records. First, you can view all the inspection work records directly in the list; second, the system also provides a variety of reports and charts for powerful viewing and display of the inspection records.
5. Due to the integration of Microsoft SQL Server, the background management system can provide users with powerful and expressive detailed reports, statistical reports, analysis charts, etc. These tables can be output to Microsoft Excel, PDF and other formats. In addition, users can add or remove reports according to their needs without the assistance of developers.
[ad_2]