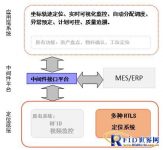
Position-based industrial production management system
[ad_1]
Requirements overview
In modern industrial production, automated production is the main method to improve production efficiency. How to improve automated production efficiency and greatly reduce production costs while improving quality is a thorny issue for enterprises. While automated production introduces lean management of the production process, production defects can be found in the product production process, and production defects are not received, manufactured, or transmitted, and problems can be solved in the shortest time, so that production can proceed smoothly and efficiently. All in all, the production process is becoming more and more complex, and the production management needs to be continuously improved. At present, there are more and more problems that need to be solved in the application of industrial production management information.
(1) Low efficiency of automatic identification: The traditional manual barcode scanning method is used, which has many steps and is prone to errors, and the efficiency is low. An automatic and active identification system is required, without manual scanning participation.
(2) Production scheduling is unscientific: Forklifts, workers, tools, etc. in industrial field production lack real-time confirmation of locations, and they cannot optimize work assignments based on task conditions.
(3) Exception early warning and unreliable quality control: Process errors, loading errors, tool errors, etc. in the production process need to be recorded and alarmed by the positioning system, and quality review information can be provided through integration with the production system.
(4) Lack of visualized management: The materials, semi-finished products, tools, etc. in the production process do not have precise location and time information, so it is impossible to monitor the production process in real time and realize visualized fine management.
(5) The plan is difficult to optimize and the cost is uncontrollable: It is hoped to optimize the production plan and achieve cost control through positioning to simplify the production process, improve production efficiency, and reduce labor costs.
Production process visualization is a magic weapon to solve the above problems, and truly effective visualization is inseparable from the support of high-precision real-time positioning and monitoring systems. On the basis of more than 10 years of real-time positioning and process optimization application experience, Dunn Technology has established a variety of real-time positioning Technology is introduced into production process management, and the industry-leading new positioning-based production process management system is launched.
Implementation plan
This system consists of high-precision RTLS,RFID, Smart factory application system, etc., combined with the customer’s MES/ERP production, and customized on the basic platform according to the specific business flow. Through the high-precision RTLS positioning system, the materials, spare parts, semi-finished products, forklifts, and workers in the production area are accurately tracked and positioned, and the production progress of the current station of the assembly line is tracked and understood, the worker’s confirmation of the process, the tool search and use records , Release confirmation and control, etc. Can greatly provide automatic visual management of the production process, improve production efficiency and quality control.
The high-precision RTLS will be configured according to the specific needs of users. It can provide a high-precision (less than 30 cm) UWB positioning system to achieve positioning with an accuracy of up to 10 cm; a medium-precision (about 1 meter) 2.4G ranging positioning system to meet sub-meters Level positioning requirements; integrate the user’s original barcode/RFID positioning system to meet the needs of regional perception.
System functions
Visualization of industrial production |
|
• Precise positioning of materials, parts, semi-finished products, and tools,personnel; • Record production and quality data, locationinformation,scheduleVariety,Stay time |
• real timeTrack semi-finished products, The report is in the pipelinesuperiorstatus; • For stagnant components and semi-finished products,abnormalqualitystateWait forinitiativeCall the police; |
• Through 2D or 3D simulation of factories and assembly lines, process visualization and seamless integration with MESFISERP systems are realized. |
|
ProcessAnd quality control • rightProductAssembly informationconductproductconfirm; • Track the manufacturing status of the product; • Tool Quick FindAnd the correct use of records; • andPMSorEMSIntegration provides quality control functions. |
Materials andSemi-finished product management • Real-time understanding of the specific location and last time of the material; • rightForklift workconductProductionoptimizationScheduling, reasonable allocation; • Match production scheduleAnd materialsin stock,Reasonable control of inventory; • Low inventoryreal timeremind,Ensure production operation. |
Advantages
1. Real-time visualization of the production process, active positioning and identification. After joining the RTLS positioning system, active positioning coordinate-level positioning can increase the visualization rate of the production line from 30% to 80%, and further promote the intelligentization of the factory.
2. Refined management of products and tools and equipment, real-time status controllable. All batches of semi-finished products and tools are accurately positioned, and preset programs are imported in advance, and the location and availability are monitored to effectively control the production progress.
3. Real-time control of warehousing plans to effectively control inventory risks. Real-time feedback of the usage data of materials and semi-finished products, effectively integrate with the production planning system, improve inventory utilization efficiency, and analyze inventory requirements with data.
4. Exception warning and process improvement to ensure production quality and safety. Real-time monitoring of production process data, early warning of abnormal processes, interception of the transmission of defects, can reduce the error rate by 8%, and can prevent driving accidents.
5. Improve production efficiency and reduce the time loss of personnel errors. Active real-time positioning of personnel reduces the flow of personnel and the time for confirmation of procedures, which can increase per capita production efficiency by 5%, further increase production capacity and reduce costs.
Application area
Company Profile
Jiangsu Tangen Technology Co., Ltd.-a leading provider of wireless positioning technology products and solutions in China, was established in 2004. The company has a professional technology research and development and project implementation team, providing professional positioning products, application solutions and technical services for ports, automobiles, electric power, airports, military, petroleum, retail, discrete manufacturing, education and scientific research and other industries, and improve the management of the industry. Level of chemistry and automation.
[ad_2]