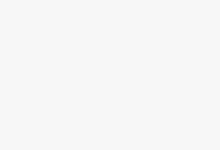
RFID warehouse management
[ad_1]
I. Overview
The RFID warehouse management system is a platform for cargo identification, tracking, management and inspection of cargo information based on RFID identification technology. The system combines advanced RFID identification technology with computer database management and query to automatically identify cargo information. The application of the system can greatly save manpower and material resources, facilitate management, improve efficiency and accuracy, and facilitate data statistics.
Traditional warehousing uses manual methods. The recording method is cumbersome, inefficient, error-prone, and relatively expensive, which is particularly inconvenient for statistics and management.
It is not convenient to receive the goods if the order is not properly filled.
The semi-automated warehouse management system needs to record the entry and exit of the warehouse before entering the computer. The human factor is relatively large, the accuracy is not high, and the forged data is prone to appear.
The requirements for standardized operation of personnel are relatively high, and human resources are wasted.
In all walks of life, cargo storage management has always been a thorny issue for enterprises. Faced with the work of entering and leaving warehouses that must be repeated every day, warehouse management plays a vital role in the entire supply chain of an enterprise. If the correct purchase and inventory control cannot be guaranteed, it will lead to an increase in management costs and service quality. It is difficult to obtain guarantees, thus affecting the competitiveness of enterprises; traditional simple and static warehouse management can no longer guarantee the efficient use of various resources. Today’s warehouse operations and inventory control operations have become very complex and diversified. Relying only on manual memory and manual entry is not only time-consuming and labor-intensive, but also prone to errors, causing unnecessary losses to the enterprise. At present, many warehouse management are mainly realized based on the corresponding standardized manual operations and computer semi-automatic management. The shortcomings are obvious, that is, a large amount of manpower is required to standardize the placement of items, find materials, regularly organize inventory, and register in and out of the warehouse. It makes the storage management problem very cumbersome, wastes a lot of time, and the production efficiency of the enterprise cannot be maximized.
The reasonably designed RFID warehouse logistics management system we provide will find a good solution to these problems.
Use the RFID warehousing logistics management system to implement the whole process control and management of each link of the warehousing, and realize the RFID electronic label management of the quantity, specification, date, warehouse number, warehouse area number, etc. of the goods, and the entire receipt and delivery , And other standardized operations in each link, RFID technology is introduced into warehousing logistics management, removing the steps of manual writing and input, and solving the phenomenon of outdated and lagging warehouse information. The combination of RFID technology and information technology helps companies make reasonable and effective use of warehouse space and provide customers with the best service in a fast, accurate, and low-cost manner.
The modern warehouse management system based on RFID automatic identification technology can effectively manage the warehouse process and space, realize batch management, fast in and out of warehouse and dynamic inventory; help warehouse managers in the inbound, outbound, mobile, and Inventory, finding materials and other operations are fully controlled and managed, effectively using warehouse storage space, improving warehouse storage capacity, and ultimately increasing the utilization rate of warehouse storage space, reducing inventory costs, and enhancing market competitiveness.
2. System function
This system uses electronic tags to mark and manage each object that needs to be managed in its management cycle. Managers can use this system to understand and grasp the information of each managed object customer, quantity, specification, date, etc., and take corresponding management countermeasures and measures based on this information, so as to achieve the purpose of improving the operation level and management quality of the user unit. It can be widely used in warehouse management of enterprises and institutions.
According to requirements, the system includes several modules:
System Management
Label making
Warehouse management
Outbound management
Inventory management
Transfer management
Three system characteristics
Advancement: Adopting the most advanced RFID technology in the world today, incorporating advanced management concepts and forward-looking considerations. The system adopts advanced international standards, supports and is compatible with multiple RFID protocols, and is upgraded to the EPC Class1 Gen2 that is most likely to be accepted by all users in the logistics system
Very strong integration: It has the ability to integrate with popular e-commerce platforms; it has the ability to integrate the internal business of the enterprise and the external resources of the supply chain.
Scalability: extremely strong scalability; the internal data structure and process of the system are designed for comprehensive enterprise informationization, which can facilitate the realization of friendly connection and data sharing with the information system that the enterprise will increase in the future. Throughput and response speed are only limited by network bandwidth, and the system itself is unlimited.
High security: There are perfect permissions settings, which can be easily realized through the software management platform; a perfect security log, which records the operation records of each user’s important behavior.
Good interface: The system will provide a standard user interface for information management, parameter setting, question inquiry, data maintenance and other functions.
Convenient maintenance: The equipment is of high quality, basically maintenance-free; it has excellent maintainability and extremely low maintenance costs.
Both methods require the storage of goods to be very standardized and require regular inventory, which is inconvenient.
Failure to provide managers with real-time, fast, and accurate inventory information in order to implement the most reasonable decisions may result in loss of customers.
[ad_2]